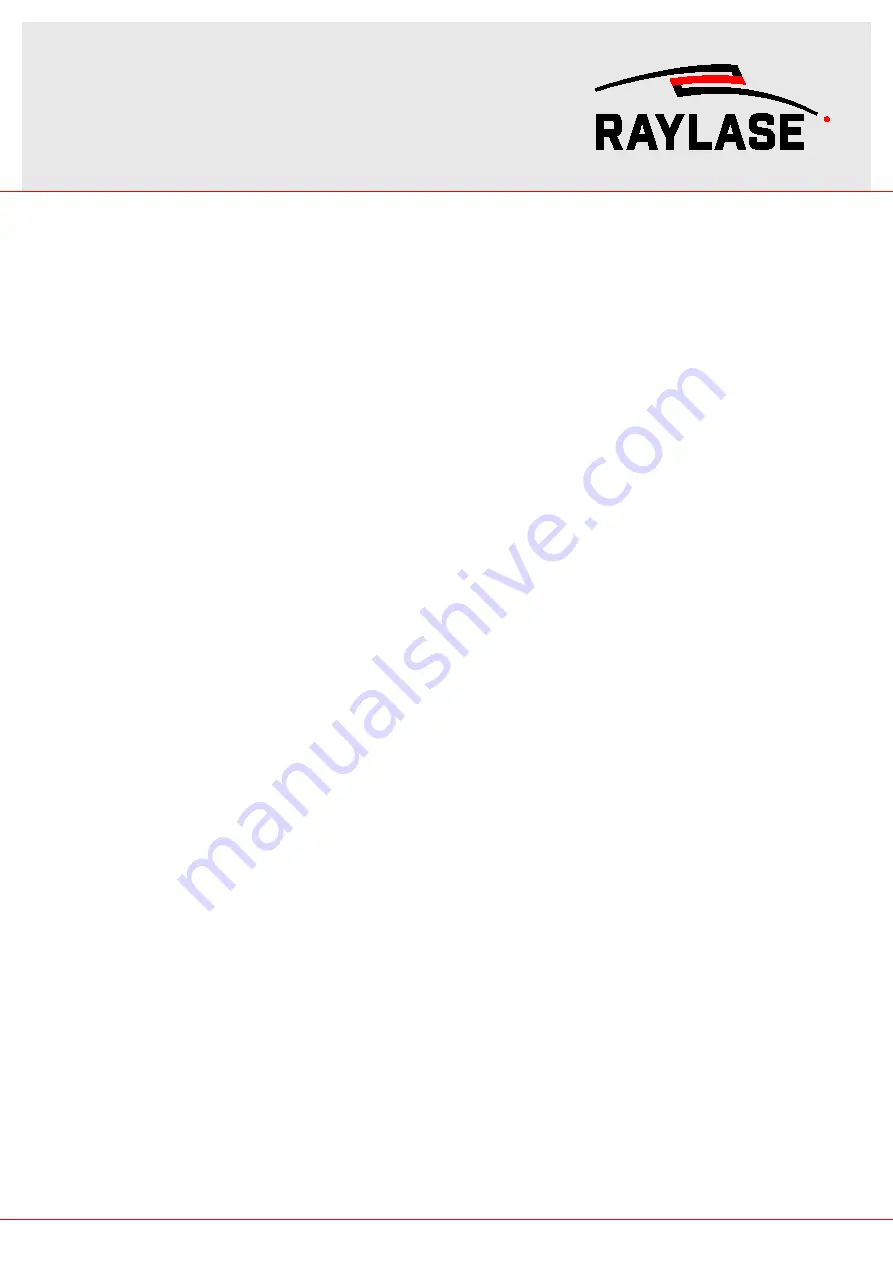
2 GENERAL SAFETY INFORMATION
© 2017 RAYLASE GmbH MINISCAN II
MN102-en / v1.0.3
7
2
GENERAL SAFETY INFORMATION
2.1
Designated use
The deflection unit is intended to deflect laser radiation within an appropriate operating range for the
purposes of material processing.
The deflection unit is designed as a sub-assembly for laser systems and is classed as an incomplete
machine as defined in the Machine Directive. Each product version may only be operated with the
wavelength specified in the type code and with the specified beam diameter (see page 16, Signage).
Depending on the version, the MINISCAN II is designed for lasers with wavelengths of 193 nm to
11,000 nm, and an input aperture of 7, 9, 14 or 20 mm.
2.2
Foreseeable misuse
Foreseeable misuse includes the following:
Use of the deflection unit outside the specifications set out in this manual (see page 17, Technical
data).
Failure to comply with generally recognised technical regulations, as well as electrical engineering,
optical mechanical and laser technology directives, laws and standards.
Lack of or unsuitable fume extraction during material processing.
Lack of or unqualified process monitoring during material processing.
Use of the deflection unit with unsuitable laser protection measures.
Working on the deflection unit without or with unsuitable protective equipment.
Processing of flammable materials.
Installation, operation, maintenance and repair by unqualified personnel.