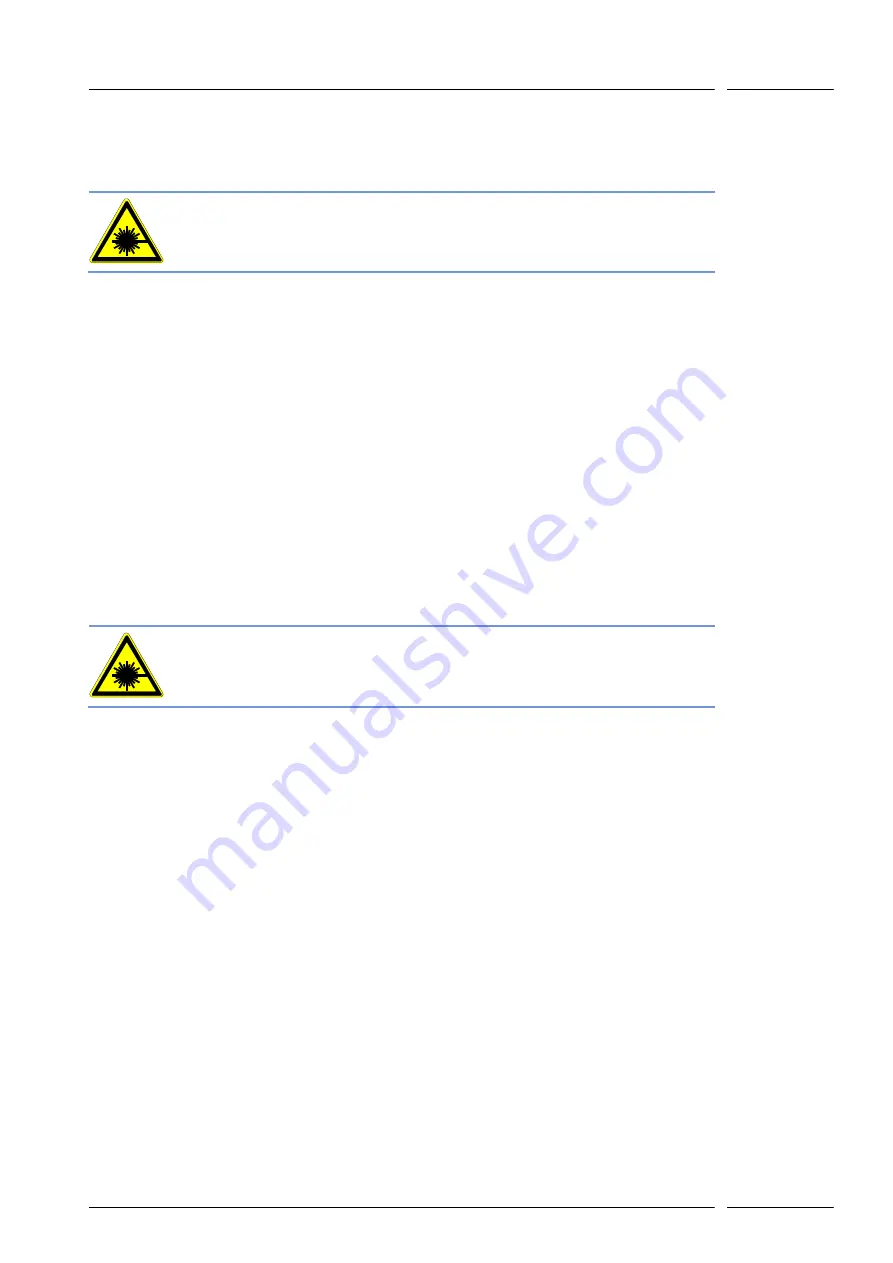
Cleaning
Chapter
6
MN049 / v1.0.0
3-Axis Subsystem AS-50 for Laser Beam Deflection
23
For subsystems fitted with a protection window only
6.2.1
Instructions for cleaning protection windows
Warning:
The laser beam can cause severe injury to the eyes and the skin. Before clean-
ing, make sure that the laser device is switched off and secured against acci-
dentally being switched on.
Fingerprints contain aggressive substances that can damage the optical surfaces. Optical
surfaces should therefore only be touched when wearing suitable gloves or with a lens clean-
ing cloth.
o
Only touch the optical elements when wearing unpowdered latex gloves and only touch the
edges.
o
Blow loose particles from the surface with clean and oil-free compressed air. Note that the
compressed air in workshops can contain oil particles and is therefore unsuitable for clean-
ing the optical system.
o
Moisten a suitable lens cleaning cloth with ethanol suitable for cleaning optical compo-
nents.
o
Place one end of the moistened cloth on the optical system and slowly move it over the
optical components. Do not exert any pressure and do not rub the optical components.
o
Remove any remaining ethanol residue with a dry optical cloth.
o
Repeat the procedure until the surface is completely clean. Use a new cleaning cloth for
each repetition.
6.2.2
Instructions for cleaning focusing lenses and mirrors
Warning:
The laser beam can cause severe injury to the eyes and the skin. Before clean-
ing, make sure that the laser device is switched off and secured against acci-
dentally being switched on.
The optical surfaces are extremely sensitive and may only be cleaned by experienced per-
sonnel.
The procedure for cleaning the focusing lenses in the linear translator is as follows:
o
Mark the installation position of the focusing lens to be cleaned to allow easy re-
installation.
o
Remove the focusing lens from the linear translator.
o
Clean the focusing lens as described above (
page 23, Instructions for cleaning protec-
o
We recommend leaving the lens in the lens holder during cleaning. However, if you do
remove the lens from its holder, when replacing it make sure that the lens is precisely posi-
tioned in the guide on the holder and refer to the data sheet for the specified direction for
the focusing lens. Close the lens holder with a torque wrench with a maximum force of
15 cNm.
o
Install the lens holder in the linear translator. Pay attention to the corresponding markings.
For cleaning the mirrors and the moving lens, we strongly recommend sending the subsystem
to RAYLASE, as opening of the deflection unit or dismantling of the moving lens by unauthor-
ized personnel voids the warranty.
However, if you do want to clean the mirrors yourself, follow the same procedure as for clean-
ing the protection window but with even more care (