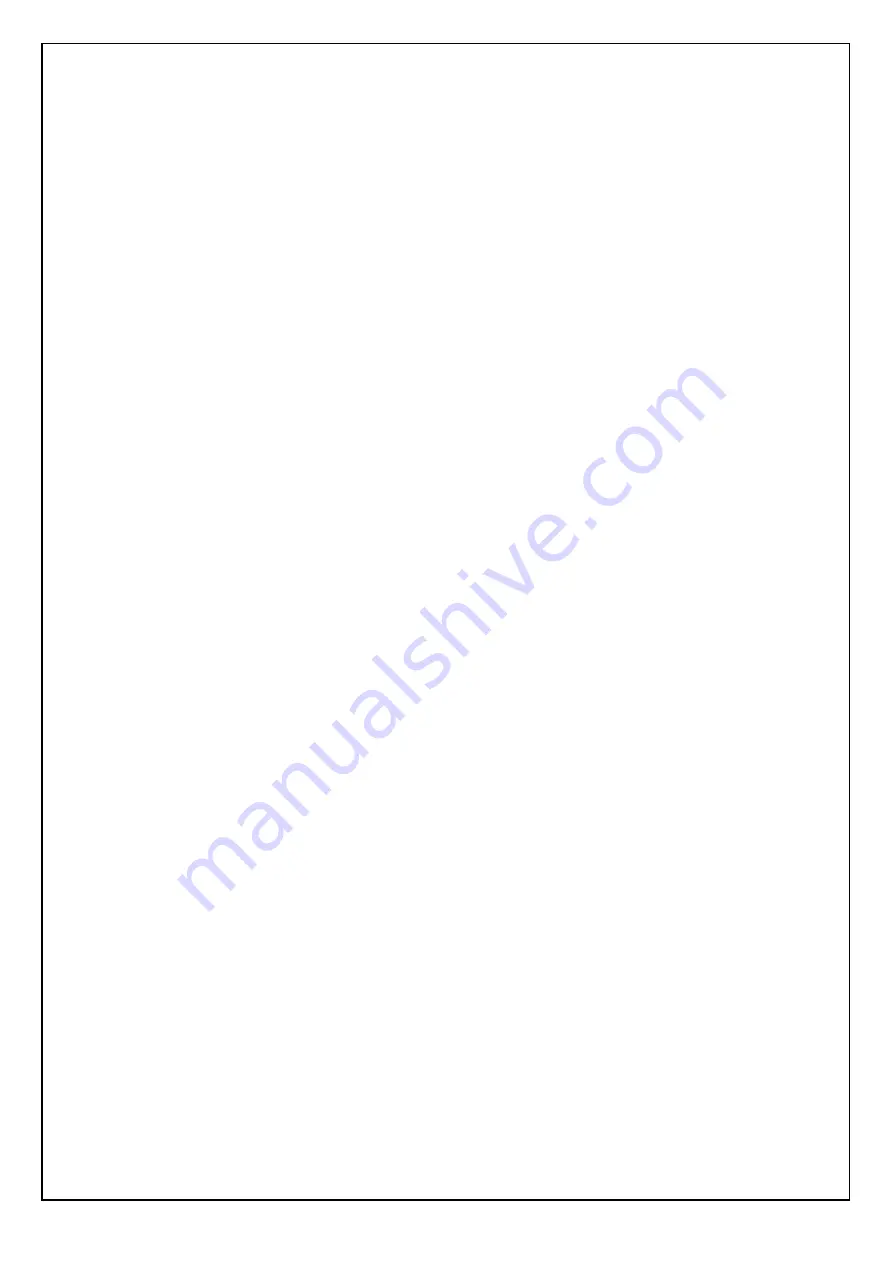
39
5.27
CONVERTING THE APPLIANCE
TO DIFFERENT GAS TYPES
Boilers are factory set to work for use
with Natural gas or LPG gas. This is
clearly marked on the packaging and
boiler data badge.
To convert a boiler from one gas to
another this operation must be carried
out by a qualified competent person,
with all necessary equipment
authorised by th
authorised by the manufacturer.
It will also be necessary to obtain a data badge
conversion kit directly from Ravenheat.
1 - Remove the case.
2 - Check gas mains pressure at the gas
valve test nipple upstream (fig.35)
with boiler operating (sect.6.8).
3 - Adjust fan speed as sect.3
(technical data).
4 - Measure the level of CO
2
as in section
as in section
6.9 and table 10, and adjust to correct
6.9 and table 10, and adjust to correct
data settings information.
data settings information.
5 - Affix new data badge.
6 - Replace in reverse order.
5.28
ELECTRICAL CONNECTIONS
IMPORTANT:
Electricity supply must be as specified in
clause (sect. 4.22).
- When controls external to the appliance are
required, design of the external electrical
circuits should be undertaken by a
competent person. In accordance with the
IEE wiring regulations.
It is essential that all external controls
are VOLT FREE.
Factory fitted internal wiring must not be
disturbed when wiring external controls.
- To gain access to the electrical box remove
the front panel of the case as described in
clauses sect. 8.2.
8.2.
You can slide towards the top the
You can slide towards the top the
instrument panel box and push the retaining
instrument panel box and push the retaining
latches and remove the instrument panel
latches and remove the instrument panel
(sect. 8.24).
(sect. 8.24).
- Heat resistant flexible cable is fitted
- Heat resistant flexible cable is fitted
between the isolator and the terminal block
between the isolator and the terminal block
which is a 3 core cable
which is a 3 core cable of 0.75 mm
2
(24x0,2
mm) to BS 6500.
Make sure all wires to the appliance are
routed away from sharp edges and hot
surfaces.
The cable must be fastened with its cord
anchorage and connected so that it should
make the cable slip from the anchorage
until the current carrying conductors
become taut before the earthing conductor.
Securely tighten all terminal screws and
arrange the cable with slack between the
cord anchorage and the terminal block.
WARNING:
If the supply cord is damaged, it must be
replaced by a service engineer (supply
cord available from Ravenheat).
5.29 OUTDOOR SENSOR
For use, consult Outdoor Sensor
instructions.
6 COMMISSIONING
Each boiler has been through a rigorous
operational testing procedure at our factory
and should not require any further
adjustment, if you are not the installer but
just commissioning this boiler check that the
boiler has been installed in accordance with
these instructions, and the integrity of the
flue
system and the flue seals, as described in
the
flue installation section.
6.1
GAS SUPPLY INSTALLATION
Inspect the entire installation including the
gas meter, test for soundness and purge, all
as described in BS 6891.
In Ireland refer to IS 813:2002.
6.2 ELECTRICAL INSTALLATION
Preliminary electrical systems checks to
ensure electrical safety shall be carried out
by a competent person.
ALWAYS carry out the preliminary electrical
system checks:
i.e. earth continuity, polarity, resistance to
earth and short circuit, using a suitable test
meter.
6.3
INITIAL FILLING OF THE SYSTEM
Open central heating flow and return
valves Unscrew the cap on automatic air
release valve positioned on the top of the
pump housing one full turn (leave open
permanently).
- Close all air release taps on the central
heating system. Press the info button to
display the current pressure (code E08 will
display if the pressure is nil/too low).
- Gradually open stopcock at the filling point
connection to the central heating system
until water is heard to flow.
Summary of Contents for HE 80 T
Page 2: ...2...
Page 21: ...21 4 10 FLUE TERMINAL POSITION...
Page 54: ...10 ELECTRICAL SYSTEM DIAGRAM 54 Fig 55...
Page 55: ...55 11 SPARE PARTS Fig 56...
Page 61: ...61...
Page 62: ...62...
Page 64: ...64 FLOWCHART FOR CO LEVEL AND COMBUSTION RATIO CHECK ON COMMISSIONING A CONDENSING BOILER...
Page 65: ...65 12 1 ANALYSER CHECK LIST...