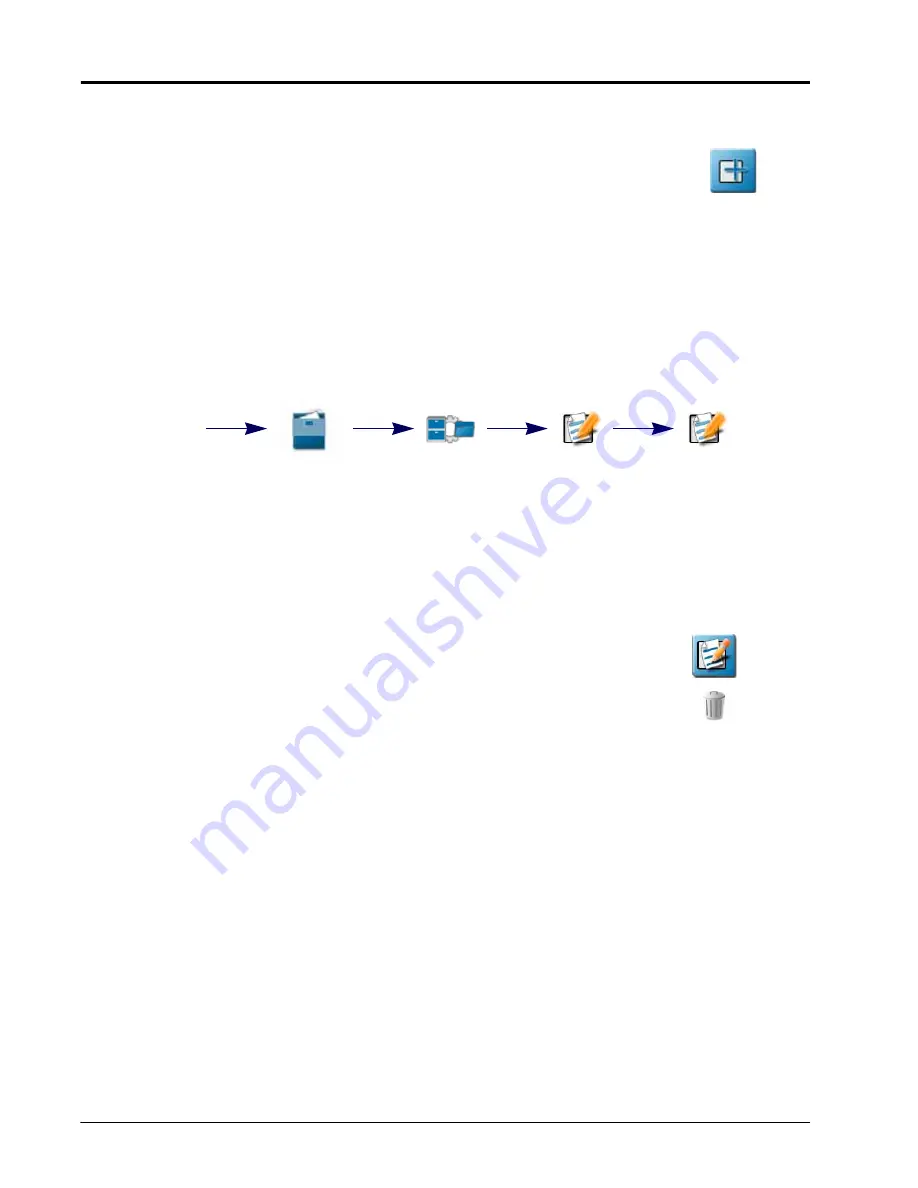
C
HAPTER
7
44
Viper/Viper 4+ Installation & Operation Manual
5. Touch the Grower panel at the top of the display to expand the Grower panel.
6. To add a new:
•
grower to the GFF structure, select the Add button.
•
farm or field to an existing Grower, select the appropriate grower from the list.
7. Touch the Farm panel below the list of available growers to expand the Farm panel.
8. To add a new:
•
farm to the GFF structure, select the add button.
•
field to an existing grower and farm, select the appropriate farm from the list.
9. Touch the Field panel at the bottom of the GFF display to expand the Field panel.
10. To add a new field, touch the Add button to add a field to the selected grower and farm.
MANAGE GROWER, FARM, FIELD (GFF) INFORMATION
To edit current grower, farm, field associations for all files displayed in the Selected Files list:
NOTE:
Review the Selecting Files section on page 43 for assistance with selecting files.
1. Touch the Administrator or User Panel along the top of the Main Panel display to expand the panel.
2. Select the File Manager utility and press the File Manager tab. File Manager will open and display a list of files
currently stored on a ROS device.
3. Touch the Edit button at the top of the Selected Files list.
4. Select the Edit button displayed at the top of the GFF display.
5. Use the file browser to select the desired grower, farm, or field entry to edit.
6. With the appropriate entry selected, touch the Edit button. To delete a GFF entry, touch
the delete button.
RESET GROWERS, FARMS, FIELDS
Select reset growers, farms, fields (GFF) to reset all grower, farm, or field information. To reset grower, farm, field
information:
1. Open File Manager.
2. Press the Arrow next to the desired grower, farm, or field in the all files column to move the desired GFF to the
Files column.
3. Press the Notepad key above the files column. This will open the grower, farm, field manger screen.
4. Press the Delete icon in the reset grower, farm, field cell. A prompt will open asking “This action will
permanently remote all growers, farms, fields and their associations. Do you wish to continue?”.
5. Select Yes to reset all growers, farms, fields and their associations. Press No to return to the previous screen.
Add
Administrator
or User Panel
File
Manager
Edit
Edit
File
Manager
Edit
Delete
Summary of Contents for viper
Page 16: ...CHAPTER 2 8 Viper Viper 4 Installation Operation Manual ...
Page 48: ...CHAPTER 6 40 Viper Viper 4 Installation Operation Manual ...
Page 67: ...File Manager 59 FILE MANAGER ...
Page 68: ...CHAPTER 7 60 Viper Viper 4 Installation Operation Manual ...
Page 112: ...CHAPTER 9 104 Viper Viper 4 Installation Operation Manual ...
Page 174: ...CHAPTER 16 166 Viper Viper 4 Installation Operation Manual ...
Page 176: ...CHAPTER 17 168 Viper Viper 4 Installation Operation Manual ...