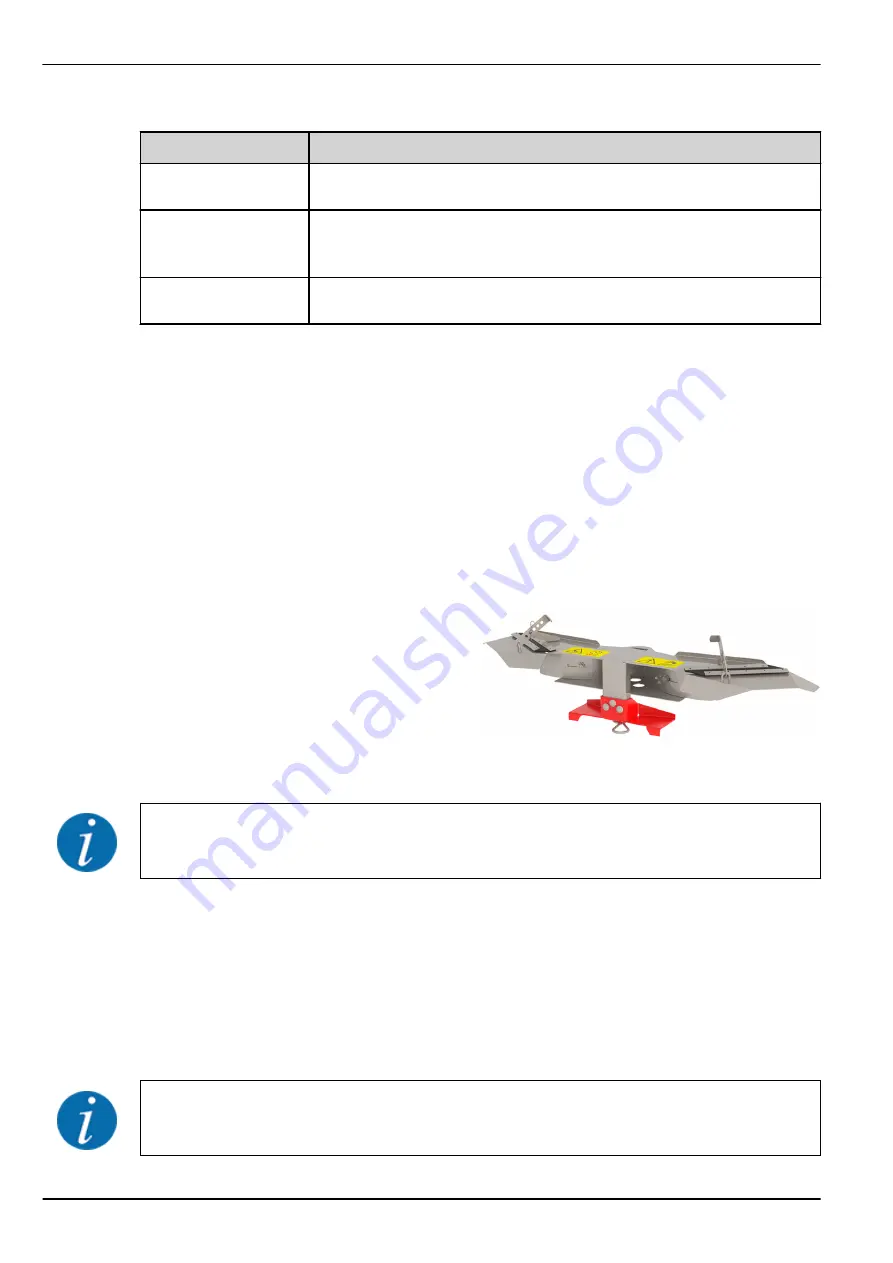
Hopper cover
Application
AP 13
•
Basic hopper MDS 14.2
AP 19
•
Basic hopper MDS 18.2/20.2
•
Extensions: M 430, M 630
AP 240
•
Extensions: M 800, M 1100
4.4.3
Row spreading system
n
RFZ 7
All versions except MDS 8.2
This 7-row spreading system is suitable for depositing dry, granulated fertilizer in rows next to
sprouting plants.
A separate operator’s manual is supplied with the row spreading system.
4.4.4
Row spreading system
n
RV 2M1 for hops and fruit cultivation
The row spreading system is designed such
that an approx. 1 m wide strip is spread,
depending on the fertilizer, for each row to the
right and left of the machine (row spacing:
approx. 2-5 m).
Information about spreading with the special equipment can be found in chapter
spreading system for hops and fruit cultivation
4.4.5
TELIMAT boundary spreading unit
n
TELIMAT T1
The TELIMAT limited border spreading unit is used for remote-controlled boundary and border
spreading from the track (left).
A double-acting valve is required for use of the TELIMAT T1 limited border spreading unit.
Information about spreading with the special equipment can be found in chapter.
the TELIMAT full and limited border spreading unit
4. Machine data
34
5902916
MDS 8.2/14.2/18.2/20.2
Summary of Contents for MDS 8.2
Page 150: ......