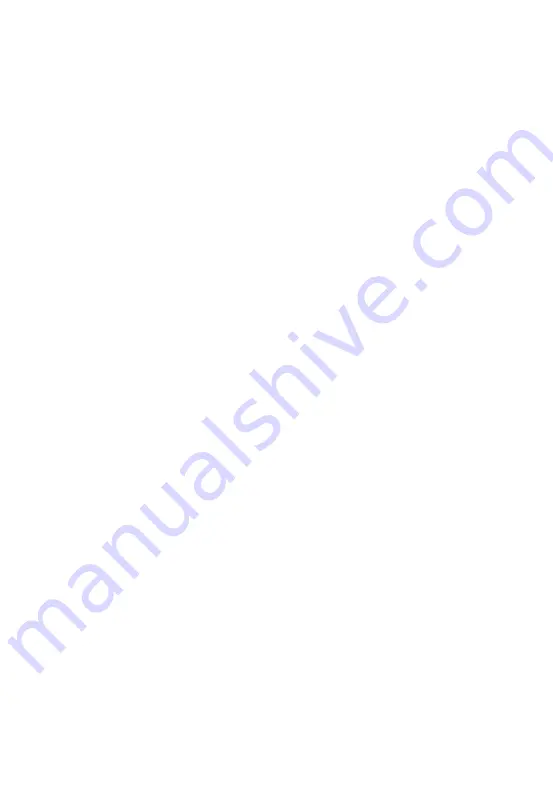
·
1
·
PREFACE
Thank you for purchasing our welder.
This manual contains the information on how to do that. Be sure to read
it carefully before operation. Operate it safely and correctly, you can get
the best results.
All information and diagrams in this publication is based on the latest
products information available at the publishing time. The contents in
this manual may be different from the actual parts due to revision and
other changes. Our company reserves the right to make changes at any
time without notice and without incurring any obligation. No part of
this publication may be reproduced without our Company’s written
permission.
This manual should be considered a permanent part of the welder and
should remain with the welder if resold.
Summary of Contents for RTAXQ1-190
Page 1: ...RTAXQ1 190 RTAXQ1 190D RTAXQ1 190 2 Owner s Manual...
Page 2: ......
Page 9: ...7 2 Model No COMPONENT IDENTIFICATION MODEL NO FINISHED PRODUCT NO SER NO...
Page 34: ...32 XI WIRING DIAGRAM RTAXQ1 190 WIRING DIAGRAM...
Page 35: ...33 WIRING DIAGRAM RTAXQ1 190D...
Page 36: ...34 RTAXQ1 190 2 WIRING DIAGRAM...
Page 39: ......
Page 40: ...93004 X010220 0000...