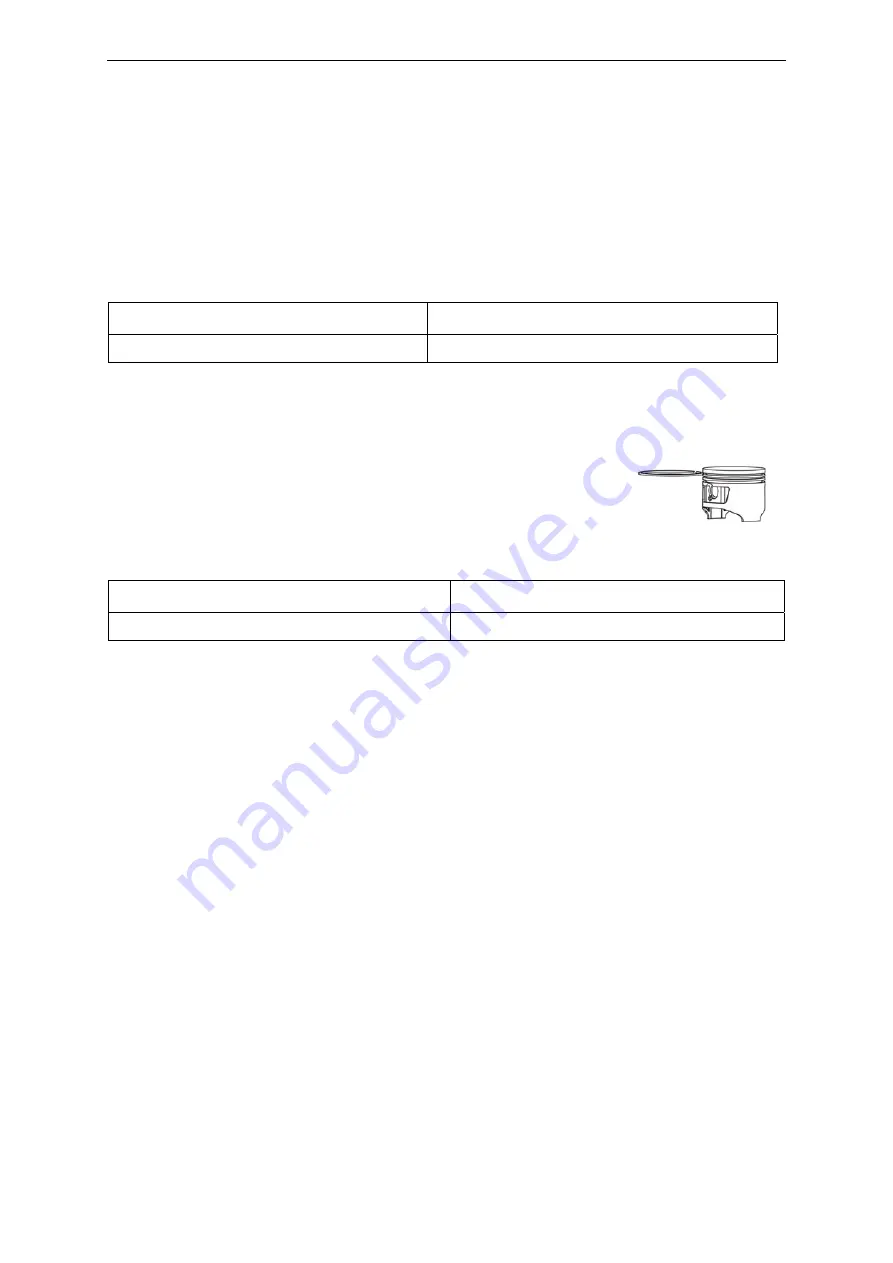
50
Difference between cylinder maximum diameter and piston skirt should be considered as
piston-to-cylinder clearance.
NOTICE: This clearance must be checked before and after repairing.
Check with piston upside down in the cylinder, and inserting feeler between piston skirt
bearing face and wall, then pull the feeler out, if feeling resistance and moving smoothly out,
the thickness of the feeler shall be considered as piston-to-cylinder clearance.
Standard Service
limit
See 1-3Maintenance Standard
See 1-3Maintenance Standard
d) Piston ring side clearance
Check by placing each ring into its groove. The piston ring should be
freely turned without loosening and sticking. Then measure by
inserting the feeler into clearance of the ring and upper and lower face.
Standard Service
limit
See 1-3Maintenance Standard
See 1-3Maintenance Standard
e) Piston ring end gap
Flatly place the piston into the cylinder by pushing the piston head to working position.
Measure the opening clearance with a feeler, that clearance should not be too big or too small,
if it is too big can, cylinder sealing performance will be poor, if it is too small, piston
expanded by heat will be blocked in the cylinder, thus causing piston broken and “sticking”.
If opening clearance is too small, file the opening with fine flat file. Often check in the
cylinder when filing until the proper clearance is got.
Summary of Contents for R80
Page 6: ......
Page 12: ...6 2 DIMENSIONS AND TORQUE 2 1 ENGINE DIMENSIONS 2 1 1 R100 R80...
Page 13: ...7 2 1 2 R160 R180 R200 R210 R225...
Page 14: ...8 2 1 3 R270 R280 R300...
Page 15: ...9 2 1 4 R390 R420 R440...
Page 33: ...27 9 Oil filling label...
Page 64: ...58 ELECTRIC DIAGRAM control box starter motor starter relay charging coil...