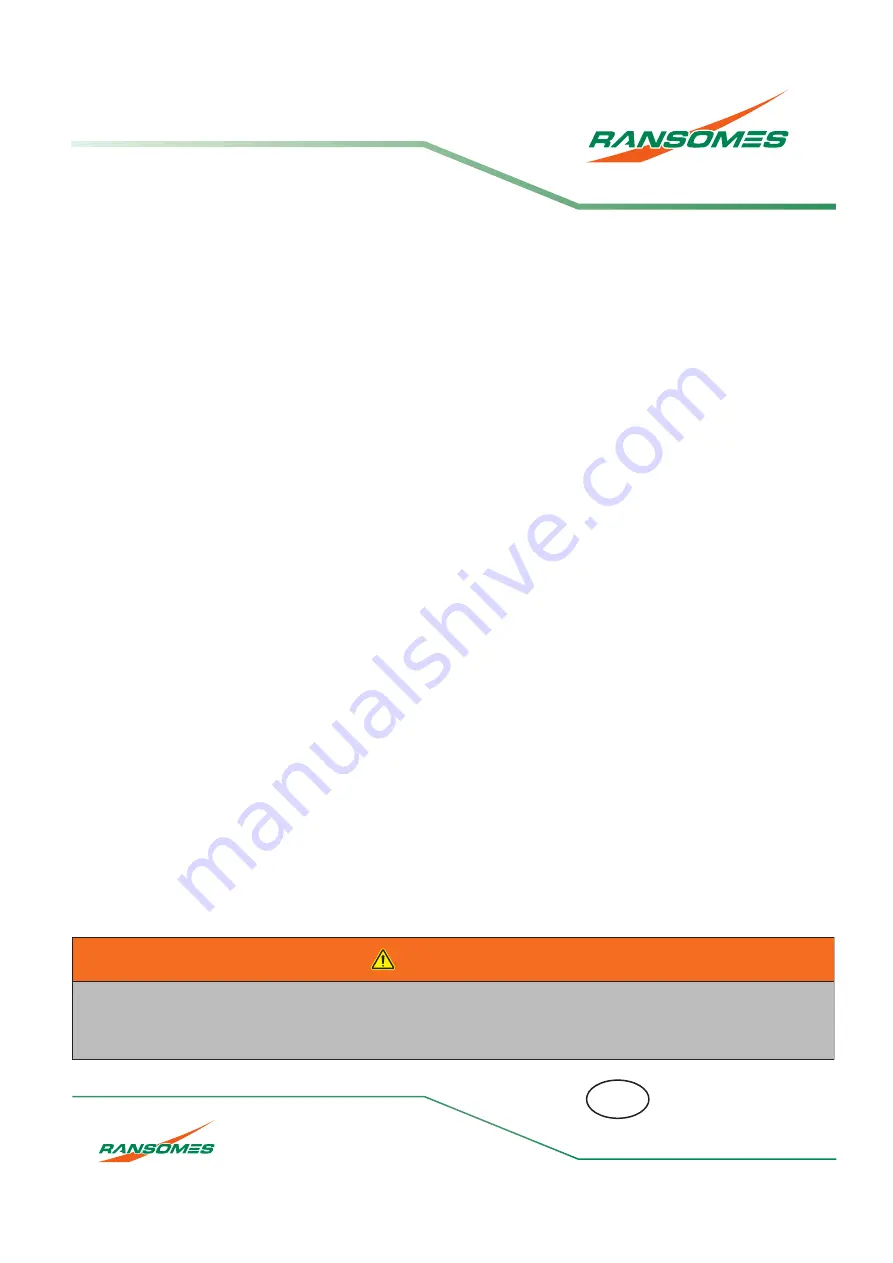
®
®
RJL AFCB
Safety, Operation & Maintenance Manual
Ransomes MT383 Ride on Triple Cylinder Mower
Kubota D1803 - CR - E5
With ROPS Series: NM
Product code:
10007371
With CAB Series: NO
Product code:
10007372
10029754-A-GB
WARNING:
If incorrectly used this machine can cause severe injury. Those who use and maintain this
machine must be trained in its proper use, warned of its dangers and must read the entire manual before
attempting to set up, operate, adjust or service the machine.
WARNING
GB
United
Kingdom
Summary of Contents for MT383
Page 2: ...2021 Ransomes Jacobsen Limited All Rights Reserved...
Page 10: ...en 10 2 INTRODUCTION NOTES 1...
Page 20: ...en 20 4 SPECIFICATIONS MT383 with ROPS MT383 with Cabin B A G D E J J H K F 1...
Page 25: ...en 25 SPECIFICATIONS 4 NOTES...
Page 61: ...en 61 CONTROLS 6 NOTES...
Page 72: ...en 72 8 MAINTENANCE AND LUBRICATION B B C C D E D E A C D E 8 8 8 11 8 5 8 5 8 9 1...
Page 98: ...en 98 9 ADJUSTMENTS...
Page 114: ...en 114 12 QUALITY OF CUT NOTES...
Page 119: ......