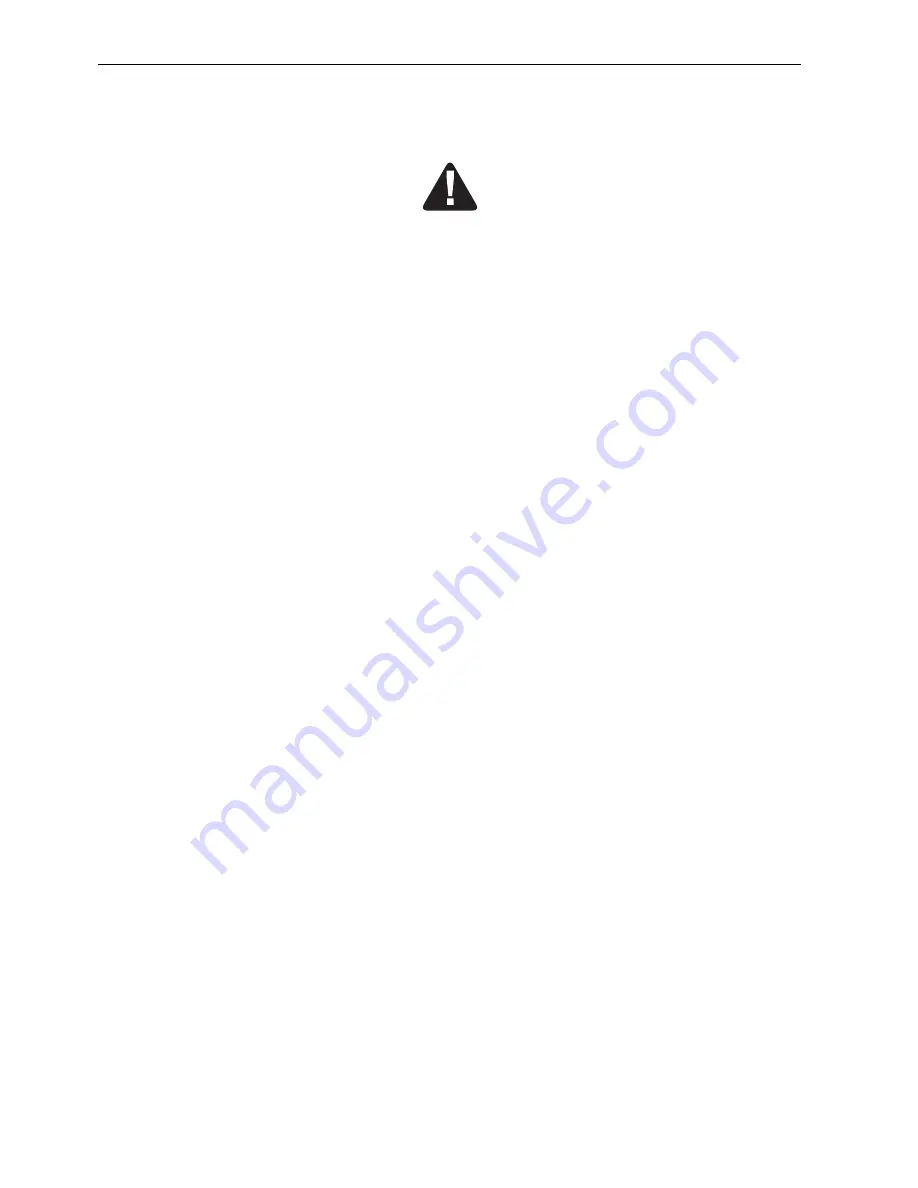
en-6
3
SAFETY INSTRUCTIONS
3.1
OPERATING SAFETY________________________________________________
This safety symbol indicates important safety messages in this manual. When you see this symbol, be alert to
the possibility of injury, carefully read the message that follows, and inform other operators.
3.1.1 OPERATING INSTRUCTIONS
•
Ensure that the instructions in this book are read and fully understood.
•
No person should be allowed to operate this machine unless they are fully acquainted with all the controls
and the safety procedures.
•
Never allow children or people unfamiliar with these instructions to use this machine. Local regulations
may restrict the age of the operator.
3.1.2 SAFETY SIGNS
•
It is essential all safety labels are kept legible, if they are missing or illegible they must be replaced. If any
part of the machine is replaced and it originally carried a safety label, a new label must be affixed to the
replacement part. New safety labels are obtainable from Ransomes Jacobsen dealers.
3.1.3 STARTING THE ENGINE
•
Before starting the engine check that the brakes are applied, drives are in neutral, guards are in position
and intact, and bystanders are clear of the machine.
•
Do not run the engine in a building without adequate ventilation.
3.1.4 DRIVING THE MACHINE
•
Before moving the machine, check to ensure that all parts are in good working order, paying particular
attention to brakes, tyres, steering and the security of cutting blades.
•
Replace faulty silencers, mow only in daylight or good artificial light
•
Always observe the Highway Code both on and off the roads. Keep alert and aware at all times. Watch out
for traffic when crossing or near roadways.
•
Stop the blades rotating before crossing surfaces other than grass.
•
Remember that some people are deaf or blind and that children and animals can be unpredictable.
•
Keep travelling speeds low enough for an emergency stop to be effective and safe at all times, in any
conditions.
•
Remove or avoid obstructions in the area to be cut, thus reducing the possibility of injury to yourself and/or
bystanders.
•
When reversing, take special care to ensure that the area behind is clear of obstructions and/or
bystanders. DO NOT carry passengers.
•
Keep in mind that the operator or user is responsible for accidents or hazards occurring to other people or
their property.
•
When the machine is to be parked, stored or left unattended, lower the cutting units or apply the transport
latches.
•
While mowing, always wear substantial footwear and long trousers. Do not operate the equipment when
barefoot or wearing open sandals.
Summary of Contents for Highway 3
Page 80: ...en 78 10 ACCESSORIES...
Page 93: ......