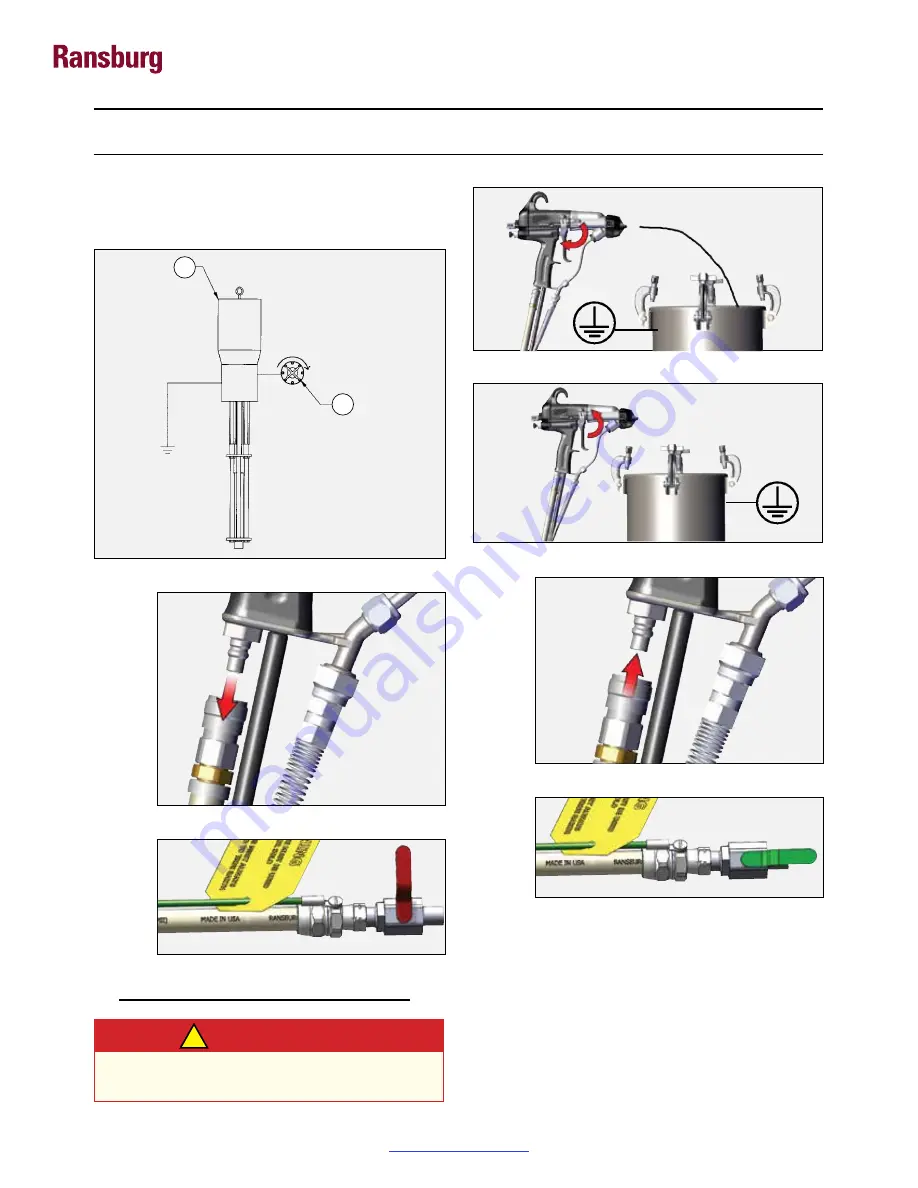
W A R N I N G
!
OPERATION
APPLICATOR OPERATION
1. Set fluid pressure using flow regulator.
2. Disconnect the air to the applicator.
3. Activate trigger to start material stream into
grounded metal bucket or suitable area
.
4. Release trigger stop material flow.
The bucket or area sprayed into must be
grounded to true earth ground.
5. Re-connect air supply.
1 - Fluid Supply
2 - Flow Regulator
6.9 bar (100psig) Max
1
2
OR...
OR...
6. Adjust air pressure.
7. Position air cap to achieve pattern direction.
8. Actuate applicator (with voltage off) to spray
test pattern.
9. As a guide, the tables below show a pressure
at the wall to give 2.7 bar (40 psig) dynamic
at the handle of the applicator with different
hose lengths.
AH-15-01.2
21
Ranflex Applicators
-
OPERATION