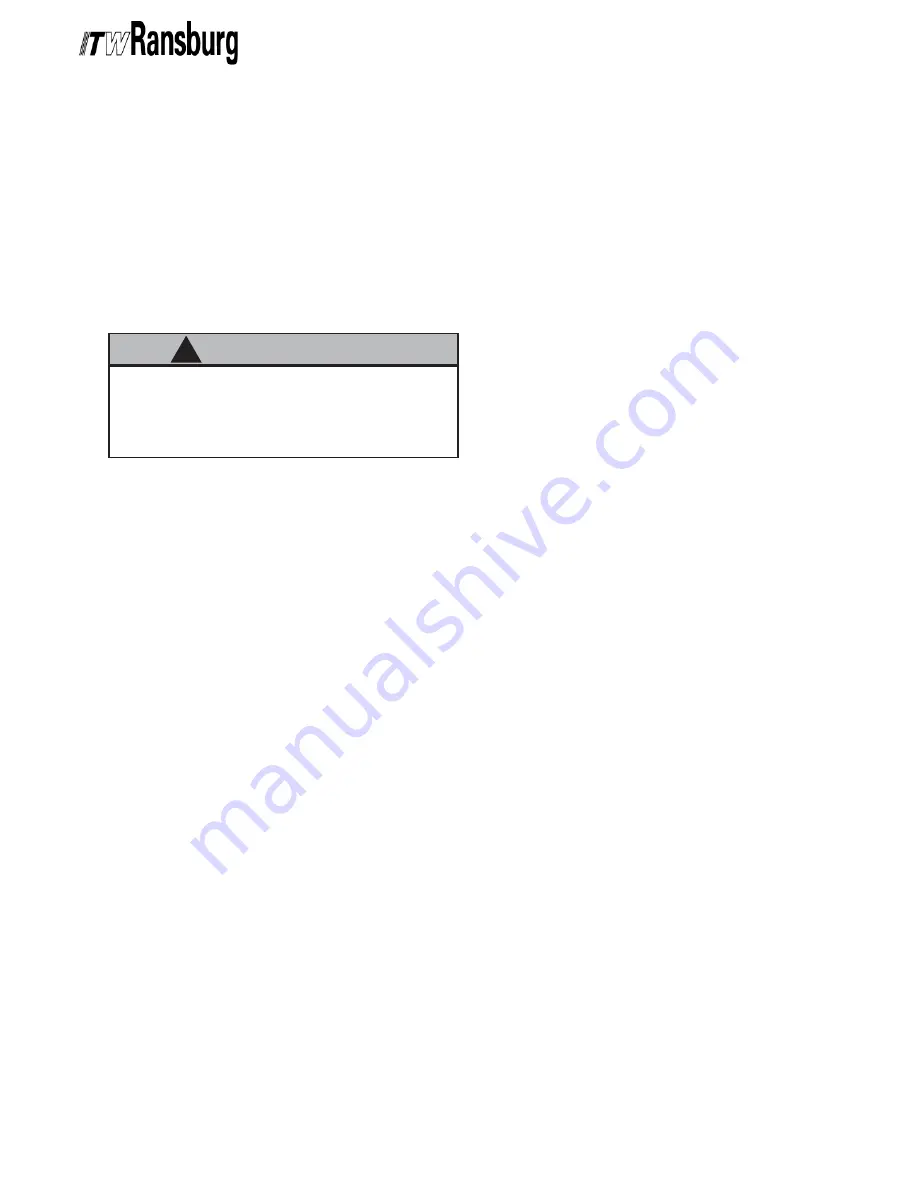
CP-06-01
8
8
8
8
8
MicroPak Controller - Installation
SAFETY GROUND
SAFETY GROUND
SAFETY GROUND
SAFETY GROUND
SAFETY GROUND
Install the ground wire assembly supplied with the
MicroPak Controller from the ground stud on the
rear of the controller to a true earth ground. For
maximum noise immunity, cut the ground wire
assembly to the shortest length required and
reinstall the end lug before making connections.
>
The ground wire assembly MUST
MUST
MUST
MUST
MUST be
connected from the MicroPak Controller
ground stud to a true earth ground.
C A U T I O N
C A U T I O N
C A U T I O N
C A U T I O N
C A U T I O N
!!!!!
LOW VOL
LOW VOL
LOW VOL
LOW VOL
LOW VOLT
T
T
T
TAGE CABLE
AGE CABLE
AGE CABLE
AGE CABLE
AGE CABLE
Standard Low V
Standard Low V
Standard Low V
Standard Low V
Standard Low Voltage Cable
oltage Cable
oltage Cable
oltage Cable
oltage Cable
(A1
(A1
(A1
(A1
(A11791-XX)
1791-XX)
1791-XX)
1791-XX)
1791-XX)
Plug the connector of the low voltage cable
assembly into the appropriate receptacle on the
rear of the controller (see Figure 3). P1 is the
output for the leftmost MicroPak control unit, when
viewed from the front, and P2 is the output for the
rightmost MicroPak control unit, if installed. When
making the connection, line the red dot on the
connector with the red mark on the receptacle and
push in until it clicks. To remove, simply pull back
on the knurled portion of the connector. Attach the
low voltage cable(s) to the stress relief bar using
TR-SSEM-200 cable ties (supplied) as shown in
Figure 3.
Junction Box Cables
Junction Box Cables
Junction Box Cables
Junction Box Cables
Junction Box Cables
(A1
(A1
(A1
(A1
(A11498-XX and A1
1498-XX and A1
1498-XX and A1
1498-XX and A1
1498-XX and A11356-XX)
1356-XX)
1356-XX)
1356-XX)
1356-XX)
The spray gun can be ordered with special low
voltage cables (A11498-XX and A11356-XX) for
splicing to a junction box. This is sometimes done
in the field, to reduce the amount of cable that has
to be replaced if a failure of the cable occurs. The
control unit and gun ends of these cables attach
as described in the standard low voltage cable
section above. Follow the instructions below to
wire the junction box ends of these cables:
Junction Box in Hazardous Location
Junction Box in Hazardous Location
Junction Box in Hazardous Location
Junction Box in Hazardous Location
Junction Box in Hazardous Location
If the junction box is in the hazardous location, an
explosion-proof junction box must be used. In this
case, connect the numbered wires of cable
A11356-XX to the same numbered wire of cable
A11498-XX using a terminal strip inside the
explosion-proof junction box. Ensure the junction
box is grounded to earth ground. Connect wire 18
(braid) of cable A11498-XX to the junction box
(ground). Seal the cable in the explosion-proof
junction box using appropriate explosion-proof
fittings and sealing compound. The exposed area
of the cable braids must be located on the junction
box side of the sealing compound.
Junction Box in Non-Hazardous
Junction Box in Non-Hazardous
Junction Box in Non-Hazardous
Junction Box in Non-Hazardous
Junction Box in Non-Hazardous
Location
Location
Location
Location
Location
If the junction box is in a non-hazardous location,
then it is not necessary to use an explosion-proof
junction box. In this case, use the supplied cable
gland (A11357-02) and gland nut (A11358-02) to
secure the cables at their entry and exit to the
junction box. Install the cable gland in the junction
box and position the cable so that the spring of the
gland makes contact to the exposed braid of the
cable when the gland nut is tightened. Ensure the
junction box is grounded to earth ground. Connect
the numbered wires of cable A11356-XX to the
same numbered wire of cable A11498-XX using a
terminal strip inside the junction box. The braid of
cable A11498-XX will be grounded through its
contact to the cable gland spring and the grounded
junction box. Wire 18, therefore is unnecessary
and may be trimmed off. Connection in this
manner will ensure maximum noise immunity.
Summary of Contents for MICROPAK A11789
Page 2: ...CP 06 01 ...
Page 35: ...CP 06 01 ...