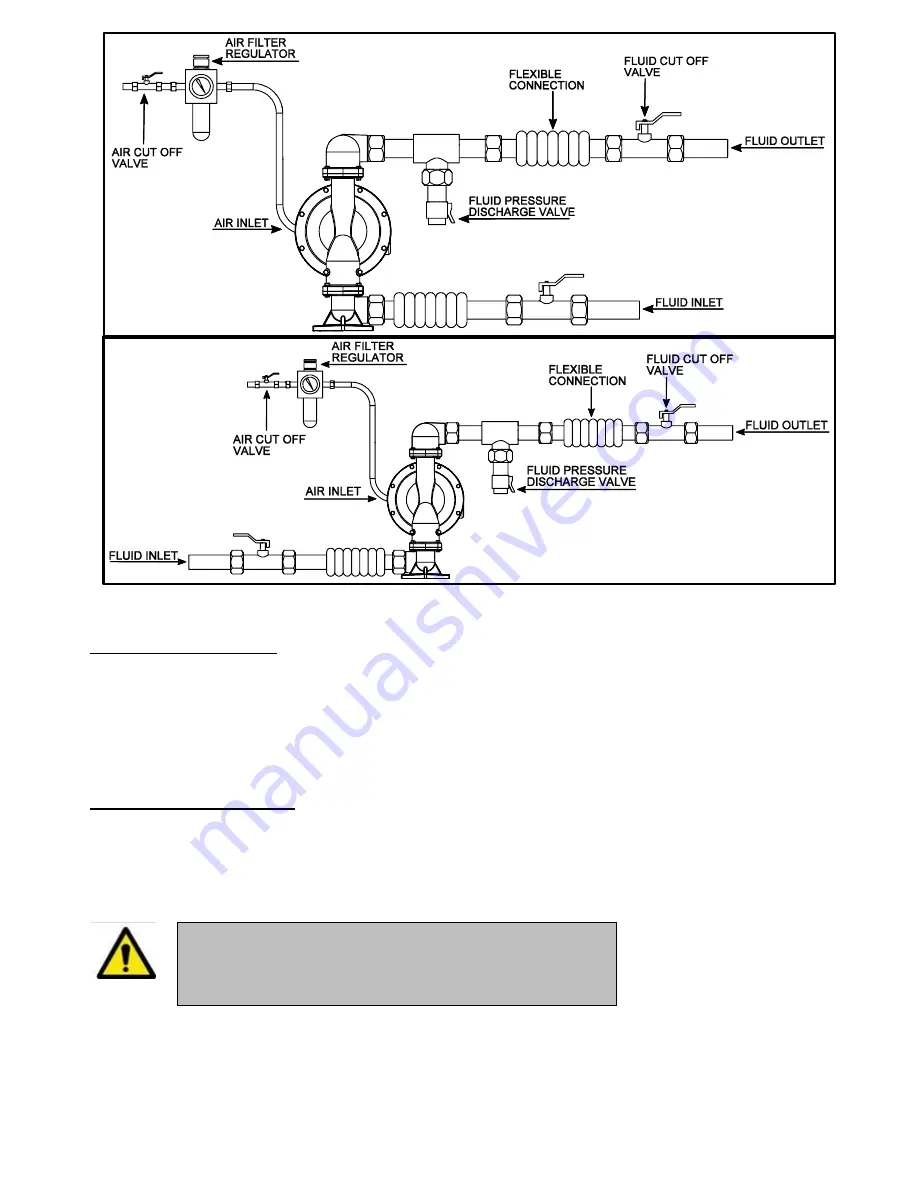
10
Figure 8a - Typical installation scheme
5.5. Fluıd lıne
5.5.1. Fluid suction line
1-
Use a conductive hose or pipe.
2-
Screw fluid fitting into the pump inlet tightly.
3-
If the inlet fluid pressure is more than 25% of the outlet working pressure, ball check
valves will not close fast enough, result will be inefficient pump operation.
4-
At inlet fluid pressures greater than 15 psi (0.1MPa, 1 bar), diaphragm life will be
shortened.
5.5.2 Fluid discharge line
1-
Use a conductive fluid hose or pipe. The pump fluid outlet is 3”. (f).
2- Screw the fluid fitting into the pump outlet securely.
3-
Install a fluid drain valve at the pump outlet.
4-
Install a fluid shut off valve at the fluid outlet.
CAUTION!
Do not over tighten fittings that are used for
connection to the pump. Overtightening may
damage the pump.