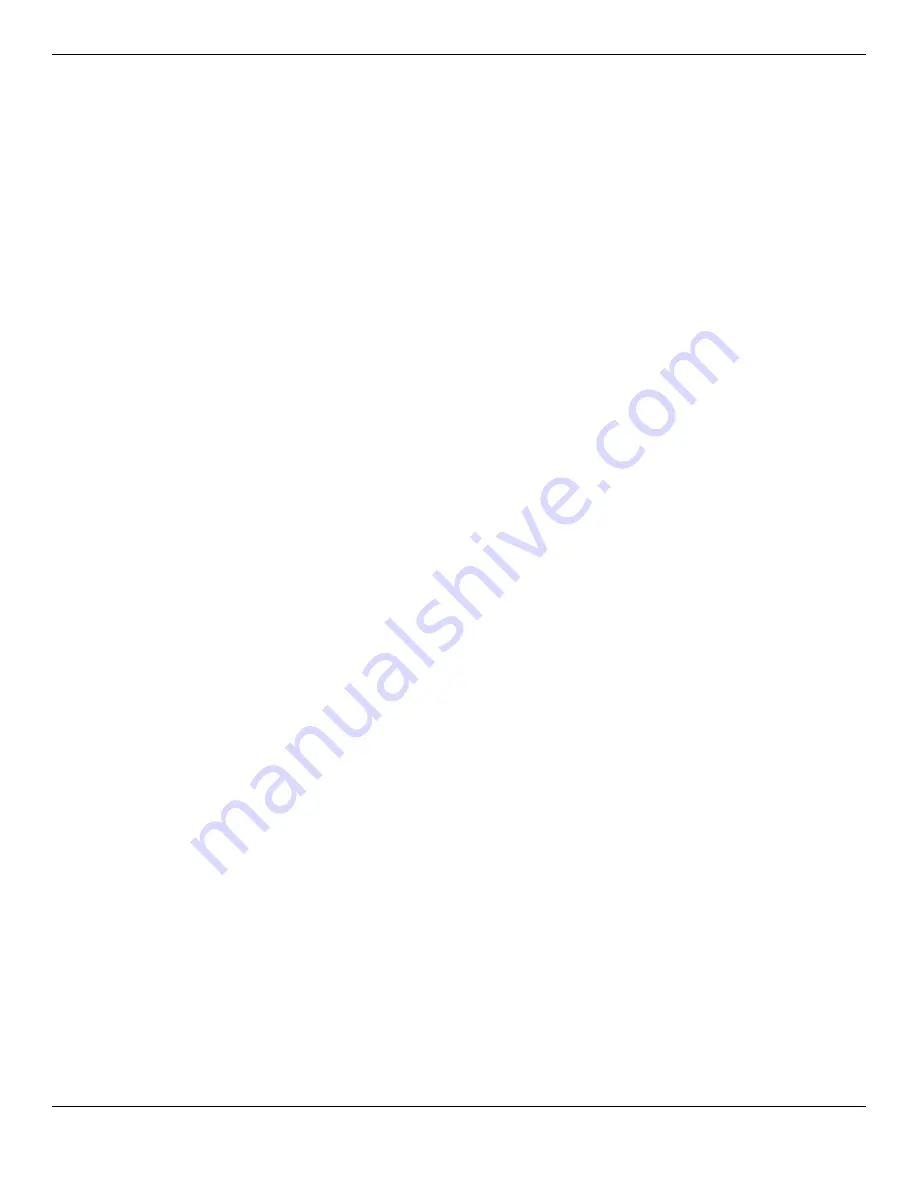
R76 Series of Tire Changers
51
P/N 5900346 — Rev. C — Dec. 2019
Bead Seating
To seat a Tire’s Beads, you put in additional air pressure until you hear a “pop”, which indicates the
Tire Beads have slipped over the Bead Retainers into their Bead Seats.
Remember that a Tire has Beads on
both sides
of the Tire. The Beads have to be seated on both
sides. Bead Seating is not complete until the Beads are seated on both sides of the Tire.
⚠
WARNING
Do not exceed 40 psi to seat a Bead
.
The following procedure assumes the Tire’s Beads have already been sealed. Do not try to seat the
Beads until the Beads have been successfully sealed.
To Seat the Beads
:
1.
Make sure the Air Chuck is clipped to the Valve Stem of the Tire.
2.
Step back from the Tire.
3.
Press and hold down the Inflation Foot Pedal.
Air begins flowing into the Tire.
After a few seconds, you should hear a “pop” as the Beads are seated.
Bead Seating usually requires 7 psi or above.
Some Beads are hard to seat, but never exceed 40 psi to seat the Bead
.
If air pressure in the Tire gets to 40 psi but the Beads are still
not
seated, use the Pressure Relief
Button to remove air down to about 5 psi and then try again to seat the Beads. If you lower the psi
too far, you may lose the Bead seal and have to do that again.
4.
Release the Inflation Foot Pedal.
5.
If the Beads do not seat on a second attempt, either:
–
get a different Tire
–
ask your Supervisor for instructions
–
let all of the air out of the Tire and start again (seal the Beads and then attempt to seat the
Beads again)
6.
If the amount of air pressure it takes to seat the Beads exceeds the manufacturer’s recommended
psi for the Tire, use the Pressure Relief Button to remove air pressure from the Tire, bringing it back
down to the recommended psi for the Tire.
7.
When the Beads are seated, remove the Air Chuck from the Valve Stem and
reinstall the Valve
Core
.