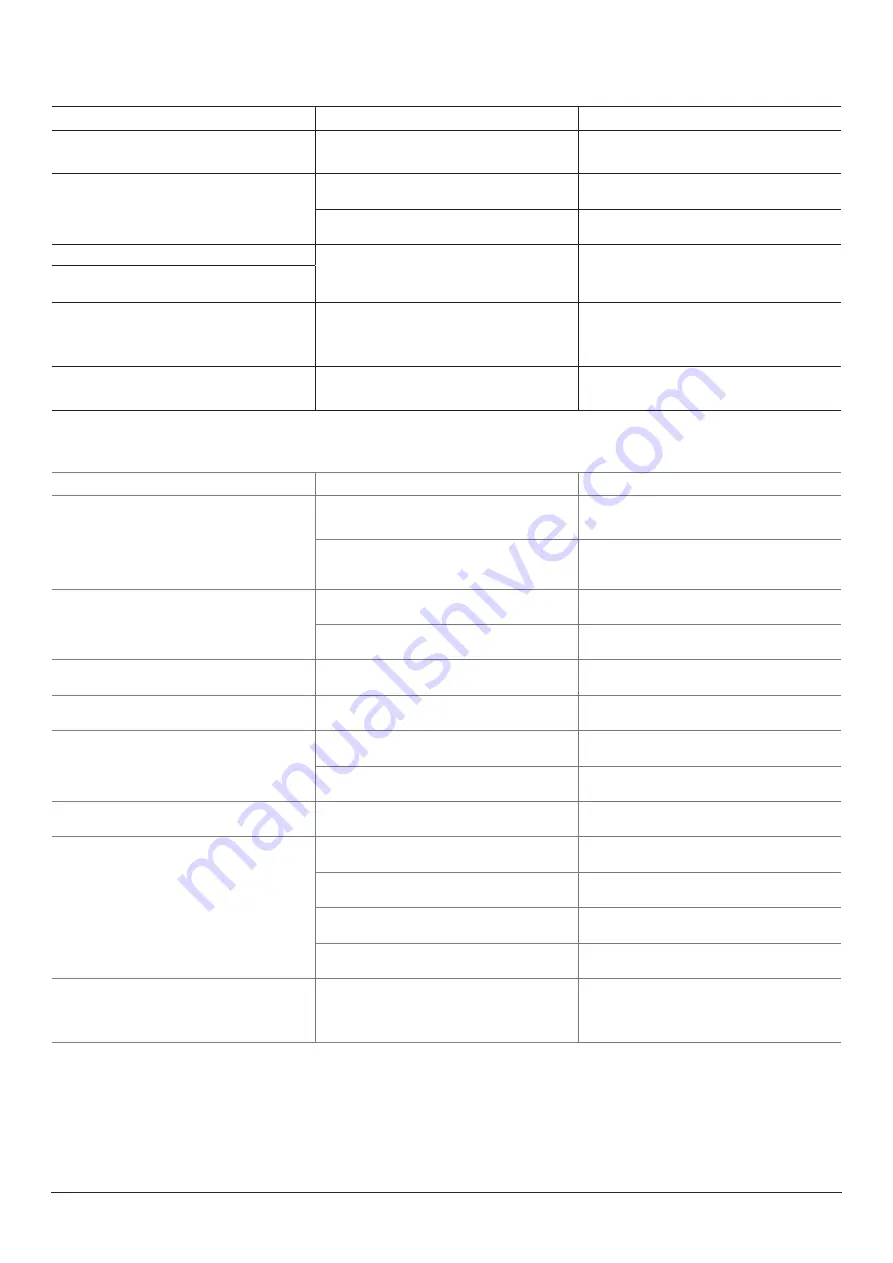
18
Due to our policy of continual improvement, we reserve the right to change specifications without prior notice.
Boiler Issue:
Likely fault(s):
Action to take:
No display visible.
Power off.
Fuse blown.
Check the power and any fuses/ Check the fuses
are 13A. Hold the power key to turn on the boiler.
Odour from drain.
Vent connection tee incorrectly added after sink
trap.
The vent tee (B2) must be on the sink side of any
trap - remove and reposition.
Odour from washer / dishwasher before the trap.
Run a cleaning program on the washer /
dishwasher.
Excess water in vent and tundish.
Boiler components are calcified.
Contact the service agent for a descaling kit, then
follow the descaling guide.
Water takes longer than usual to re-boil.
Water drips from the drain hose.
Drain hose valve faulty.
Ensure the drain hose valve is fully turned off. If
this does not resolve the issue, isolate the water
and power to the boiler, drain the system and
contact the service agent.
The boiler is beeping each time I use the tap.
The filter reminder has activated.
This is normal please refer to.
Does my filter need replacing?
Mixertap troubleshooting tips:
Mixertap Issue:
Likely fault(s):
Action to take:
Slow domestic hot water flow.
Aerator is blocked or partially blocked due to
debris or scale.
Remove aerator - clean and replace.
(see cleaning section of user guide)
Domestic hot water pressure is from a gravity
fed system and is lower than the stated
recommended minimum.
Add a booster pump to the hot water cylinder to
improve hot water flow.
Mixed water temperature is too cool.
Water pressures are unbalanced, hot water
pressure is less than cold.
Reduce the pressure or flow of unfiltered cold
water to the tap to nearer balance the pressures.
Domestic hot water temperature is too low.
Increase the boiler output temperature to help
compensate.
Water is spraying from the spout end.
Aerator is blocked or partially blocked due to
debris or scale.
Remove aerator - clean and replace. (see cleaning
section of user guide).
Water dripping from centre channel on the spout
when not in use.
Flexible hose from tap to boiler does not have a
constant fall back to the boiler.
Check the flexible hose is not looped, kinked and
has a constant fall to the boiler.
Water dripping from outside channel on the spout
when not in use.
If the water does not constantly drip, this is water
remaining in the spout releasing under gravity.
None - this is normal.
If the water does constantly drip the tap valves
most likely need replacing.
Contact the service agent for replacement valves.
Water leaking between the tap body and the
spout.
Damaged or worn spout O-rings.
Contact the service agent for replacement spout
O-rings.
No heated water is dispensed when the HotFob is
placed near the tap.
The data wire connecting the tap to the boiler is
disconnected.
Follow the wire from the tap to boiler. Check the
plugs are firmly connected.
The data wire connecting the tap to the boiler is
damaged.
The wire to or from the boiler needs replacing.
Contact the service agent for parts.
The boiler is not switched on.
Check the boiler has power and the display is not
showing any error messages.
The boiler is not heating to the requested
temperature.
Wait for the boiler to fill and heat until a constant
‘READY’ message is displayed.
The entire tap moves when used.
The tap fixing nut is loose and or gaskets from the
fixing kit have been missed out of the assembly.
Check all the gaskets listed in the tap instructions
are present. The tap is relocated centrally, then
tightened fully using a basin wrench or box
spanner.
Troubleshooting tips: