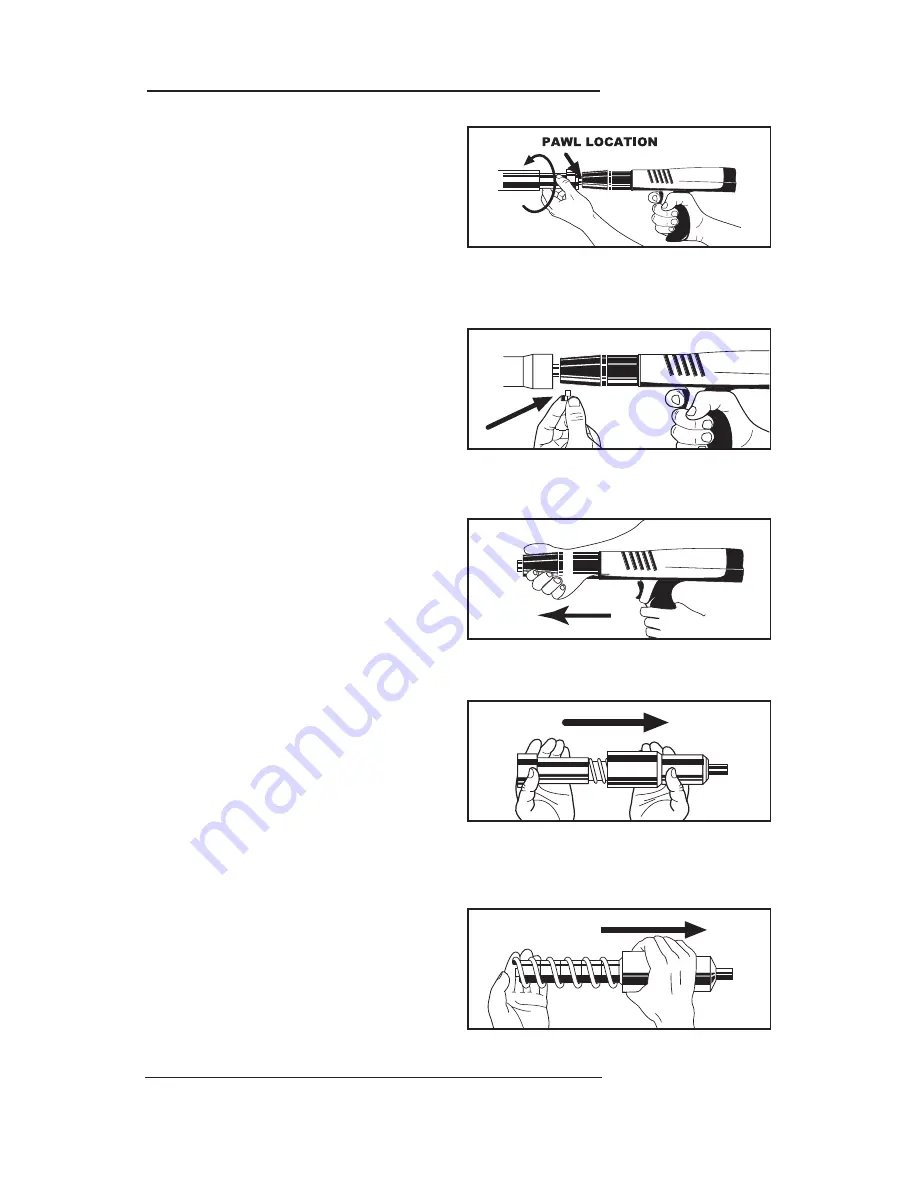
TOOL DISASSEMBLY
1. Unscrew the barrel retention sleeve
and slide it away from the tool housing.
Handle the tool carefully after the
sleeve is unscrewed to prevent the
two barrel pawls from falling out.
2. Remove the two pawls from the slots
in the sides of the tool housing while
holding the retention sleeve forward
toward the muzzle end of the tool.
3. Slide the barrel assembly out of the tool
body. Note the position of the slots on
the side of the barrel and the rod at the
lower rear of the barrel. Also note the
position of the power adjust hole.
4. Remove the retaining sleeve.
5. Remove the return spring.
UNSCREW THE BARREL
RETAINING SLEEVE
REMOVE BOTH PAWLS
SLIDE BARREL ASSEMBLY
OUT OF THE TOOL BODY
REMOVE THE RETAINING SLEEVE
REMOVE THE RETURN SPRING
DISASSEMBLY
15
DISASSEMBLY