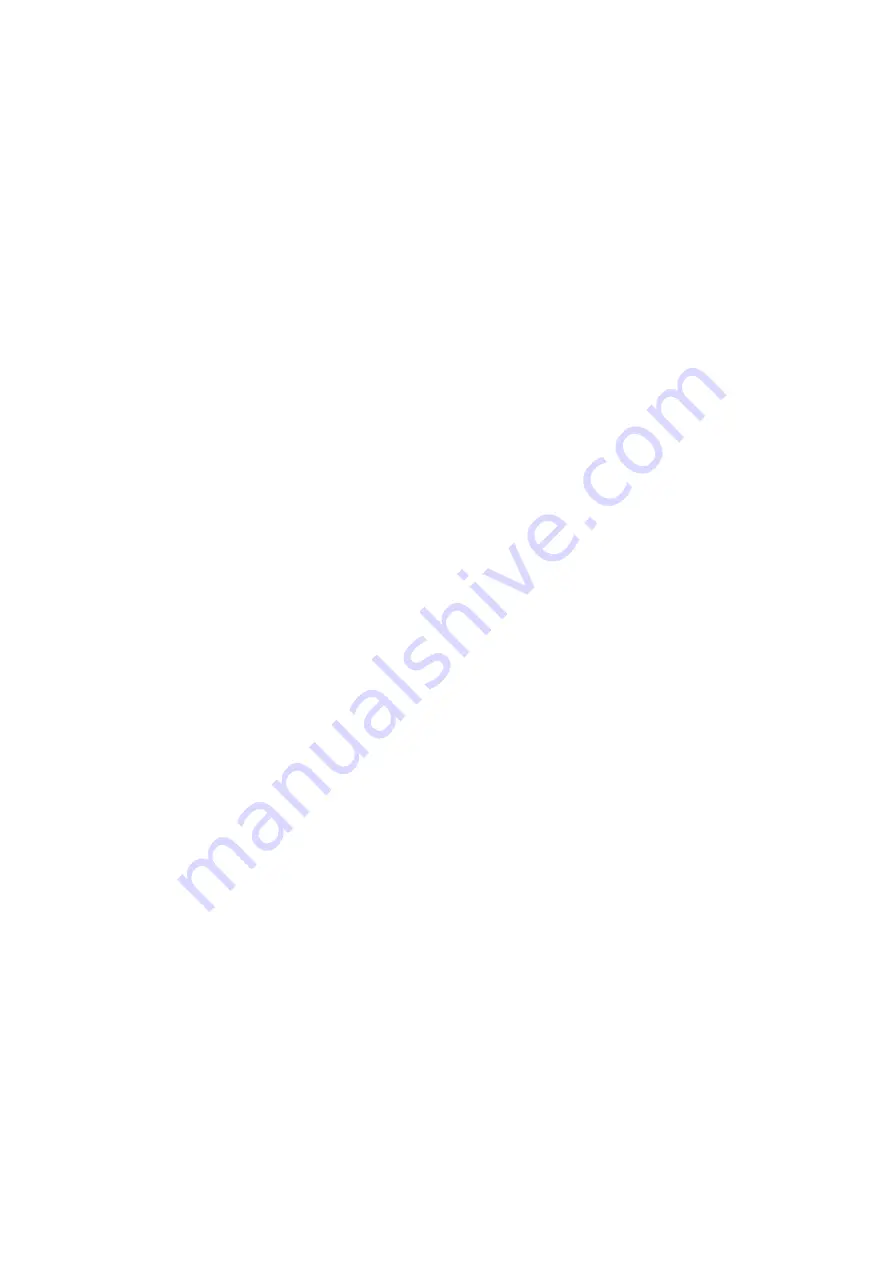
’
1.Service Information
1. Identification
(Engine Serial Number)
... ........ .
1-2
2. Work Safety
... ..................... .
1-2
1) Fire Prevention ...................................
.
1-2
2) Ventilation
... ........................ .
1-2
3) Protection
... ........................ .
1-2
4) Genuine Parts
... ................. ..
1-2
5) Tools
... .................... ...
1-4
6) Recommendations on Service
....
1-4
7) Cautions in Disassembling and
Assembling Components
......
1-6
3. Tools and Instruments
... ........ .
1-8
1) Test Propeller
... ................ ..
1-8
2) Measuring Instruments
... ......... .
1-8
3) Special Tools
... ................. ..
1-10
4. Pre-delivery Inspection
......
1-16
1) Tiller Handle ..................................
..
1-16
2) Gear Shift .................................
...
1-16
3) Gear Oil
... ...................... .
1-16
4) Fuel and Fuel Line ........................
..
1-18
5) Installation of Outboard Motor
(Rigging)
... ..................... .
1-18
6) Propeller Selection ........................
..
1-20
7) Cooling Water Check Port
..
1-22
8) Trim Tab
... ....................... .
1-22
5. Break-In Operation.....................
..
1-24
6. Test Run
... .................... ..
1-24
7. Checks After Test Run...........
...
1-24
2.Service Data
1. Outboard Dimensions .....................
.
2-2
1) Body dimensions
... ................. .
2-2
2) Clamp Dimensions
... ........ ...
2-4
2.
Cooling Water System Diagram
...
2-6
3. Specifications ............................
..
2-8
4. Maintenance Data
... ....... ...
2-12
5. Torque Specifications
... ....... .
2-16
6. Sealant And Lubricant ...........
...
2-17
3.Maintenance
1. Special Tool ............................
...
3-2
2. Inspection Schedule
... ....... ..
3-2
3. Inspection Items
... ............... .
3-6
1) Inspection of Top Cowl
... ......... .
3-6
2) Inspection of Fuel Tank
... ......... .
3-6
3) Fuel System
... ................. ...
3-8
4)
Inspection of Cooling Water Passage
.
3-10
5) Flushing with Water
... ........ ..
3-10
6)
Inspection of Compression Pressure
.
3-14
7) Inspection of Spark Plugs
..
3-18
8) Inspection of Thermostat
......
3-20
9) Adjustment of Throttle Cable
....
3-22
10) Ignition Timing Adjustment
.....
3-24
11) Carburetor Synchronization
.....
3-26
12) Pilot screw adjustment
... ......... .
3-30
13) Replacement of Gear Oil
......
3-32
14)
Inspection of Gear Case (for leakage)
..
3-34
15) Inspection of Propeller
... ......... .
3-34
16) Replacement of Anode
... .......... .
3-36
17) Greasing
........................... .
3-38
4.Fuel System
1. Special Tools
.................. ...
4-2
2. Parts Layout ............................
...
4-4
Fuel line
... .............................. .
4-4
Intake Silencer • Carburetor
... .......... .
4-6
3. Carburetor Inner Passages
....
4-10
1) Idling Passage ..................................
.
4-10
2) Off-Idle Passage ........................
...
4-12
3) High Speed Passage ........................
.
4-14
4) Choking Passage
(#2 and #3 carburetor)
... .......... .
4-16
4. Inspection Items ....................
...
4-18
1) Removing Carburetors
... .......... .
4-18
2) Disassembling Carburetors
.
4-20
3) Cleaning and Inspection
......
4-22
4) Inspection of Fuel Pump and
Needle Valve .....................................
.
4-24
5) Disassembly and Inspection of Fuel
Pump
... ................... ..
4-34
6) Assembly of Fuel Pump
......
4-26
7) Inspection of Fuel Connector
....
4-26
8) Inspection of Fuel Filter .............
...
4-26
9) Assembling Carburetors
......
4-28
10) Inspection of Float Height
..
4-30
11) Installing Carburetors .......................
.
4-30
5.Power Unit
1. Special tools
... .............. ...
5-2
2. Parts Layout ............................
...
5-4
Engine
... ........................... .
5-4
Magneto ...............................................
...
5-6
Electric Parts ................................................
.
5-8
Recoil Starter
... ....................... .
5-10
Intake Manifold · Reed Valve
......
5-14
Throttle ...............................................
...
5-16
Cylinder Crank Case..........................
...
5-20
Piston & Crank Shaft .........................
...
5-24
3. Inspection Items
... ............... .
5-26
1) Removing Power Unit
... .......... .
5-26
2) Removing Flywheel
... ......... ..
5-32
3) Removing Electric Parts
......
5-32
4) Removing Throttle Link ..............
...
5-34
5) Removing Intake Silencer and
Carburetors.....................................
..
5-38
6) Removing Intake Manifold and
Reed valves ....................................
..
5-40
7) Inspection of Reed Valve Ass'y
...
5-40
8) Removing Thermostat and
Engine Anode .....................................
.
5-42
9)
Removing Cylinder Head / Head Cover
..
5-46
10) Inspection of Cylinder Head
.
5-48
11) Removing Exhaust Cover
..
5-50
12) Inspection of Exhaust Cover
.
5-50
Summary of Contents for 50
Page 5: ...Corrosion Zero ...
Page 25: ...Service Data 2 Clamp Dimensions Front View Looking at Raider from inside RIB ...
Page 26: ......
Page 27: ......
Page 28: ......
Page 29: ...Service Data 2 Cooling Water System Diagram ...
Page 30: ......
Page 36: ......
Page 37: ...Service Data 4 Maintenance Data ...
Page 38: ...Service Data ...
Page 39: ...Service Data 5 Torque Specification ...
Page 40: ...6 Sealant And Lubricant ...
Page 44: ......
Page 45: ......
Page 65: ...Fuel System 1 Special Tools 1 Vacuum Pressure gauge P N 3AC 99020 1 Inspecting pressure ...
Page 158: ......
Page 160: ......
Page 162: ......
Page 164: ...6 ...
Page 166: ...6 ...
Page 168: ......
Page 171: ...6 ...
Page 173: ...6 ...
Page 175: ...6 ...
Page 177: ...6 ...
Page 179: ...6 ...
Page 181: ...6 ...
Page 183: ......
Page 186: ...6 ...
Page 188: ...6 ...
Page 229: ......
Page 237: ...OK Troubleshooting ...
Page 239: ......
Page 240: ...Compression ...
Page 245: ...OK Troubleshooting ...