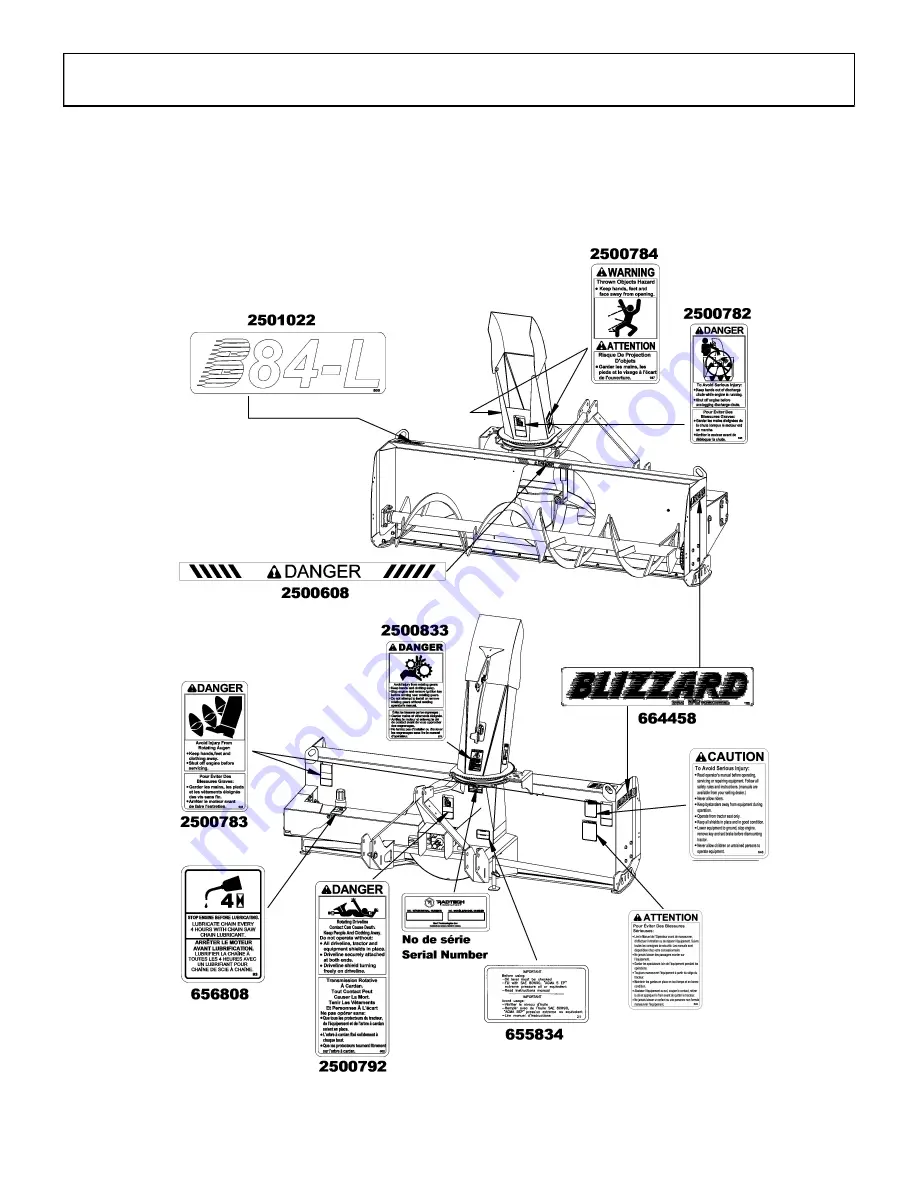
SAFETY LABELS
[11]
IMPORTANT:
Keep all decals clean and legible. Replace all
missing, illegible, or damaged decals.
IMPORTANT:
Decal placement locations shown are
approximate; decals should not be placed in a location where
the operator’s field of view is impeded, and should not cover
any portion of other decals installed in the same vicinity.
INSTALLING OR REPLACING DECALS:
Thoroughly clean
the area where decal is to be placed using mild soap and
water. Allow the surface to fully dry. Remove the backing
from the decal, exposing the adhesive surface. Apply the
decal to the recommended position shown in the diagram
below and smooth out any bubbles.
2500785
2500786
Summary of Contents for BLIZZARD B84C-L
Page 2: ......
Page 10: ...GENERAL SAFETY INFORMATION 8...
Page 11: ...GENERAL SAFETY INFORMATION 9 1 Safety stand 2 Secure point for safety stand...
Page 37: ...PARTS 35 FIG RAD1705006 SNOWBLOWER 84 FRONT...
Page 39: ...PARTS 37 FIG RAD1705007 SNOWBLOWERS 84 REAR...
Page 41: ...PARTS 39 FIG RAD1708001 CHUTE WITH DEFLECTOR...
Page 49: ......
Page 50: ......
Page 51: ......