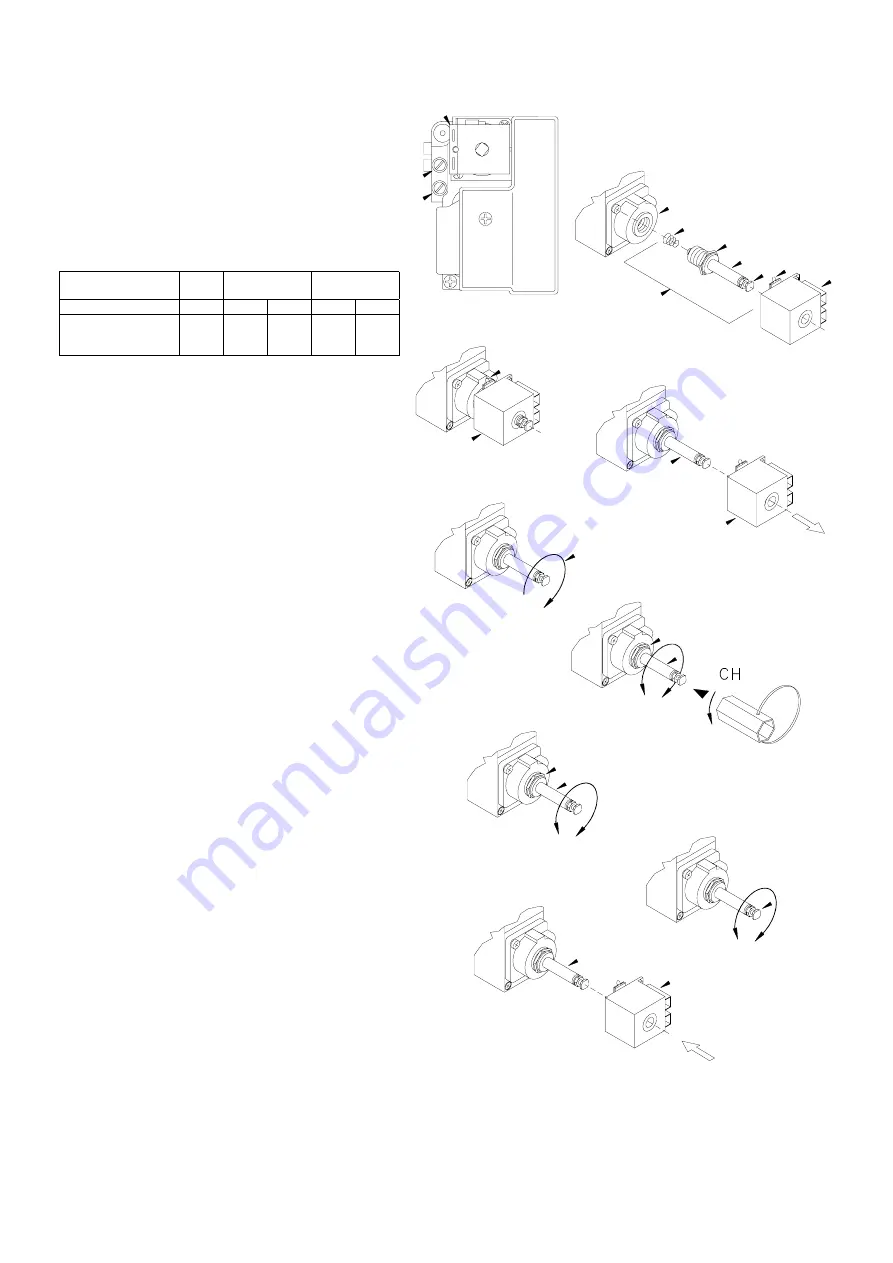
Installation Manual
Wall hung storage boiler – Cod. 99944NA – November 2002
13
REGULATING THE GAS PRESSURE
Maximum and minimum modulation pressures
.
N.B. The following operations must only be carried out
by authorised personnel and are necessary when the
boiler is converted to run on one type of gas or another
or also in cases where the maximum pressure is not
the same as that shown on the plate.
Calibration pressure.
BOILER POWER
RATING
Natural
Gas L.P.G..
Min. Max. Min. Max.
Room sealed
combustion chamber
model
mmbar
4.2 13 5 31
KEY
: (see fig. A)
1) Modulating coil
2) Fastening clips
3) Min. gas pressure adjustment screw
4) Max gas pressure adjustment core
5) Core lock nut
6) Calibrator spring
7) Modulator core
8) Gas valve stabiliser
Fig. B)
Widen locking clips (2);
Fig. C)
Slide out the coil (1) located above the gas
valve;
Fig. D)
Tighten plastic screw (3) by turning it clockwise,
be careful not to break it.
Fig. E)
Use a no.17 spanner to undo the lock nut (5)
which holds the core (4) of the coil in place; undo the
screw and insert a pressure gauge;
Fig. F)
Turn on the boiler, regulate the maximum
pressure by turning the core (4) (clockwise to increase
pressure, counter clockwise to decrease). Once
maximum pressure has been set, tighten the lock nut
(5);
Fig. G)
Adjust minimum modulation pressure with the
coil disengaged: slowly unscrew plastic screw (3) until
the pressure gauge shows the minimum pressure
required.
Fig. H)
Once these operations are completed, seal the
plastic screw with paint or enamel; reassemble the coil
(1) by pressing it back into place; remove the gauge,
tighten the screw and use a soapy solution to check for
any eventual l leaks.
10
9
1
1
4
5
4
3
1
5
4
2
7
4
8
6
4
1
5
4
2
3
1
Fig. A
Fig. B
Fig. C
Fig. D
Fig. E
Fig. F
Fig. G
Fig. H
Summary of Contents for Rmas 24 e
Page 2: ......