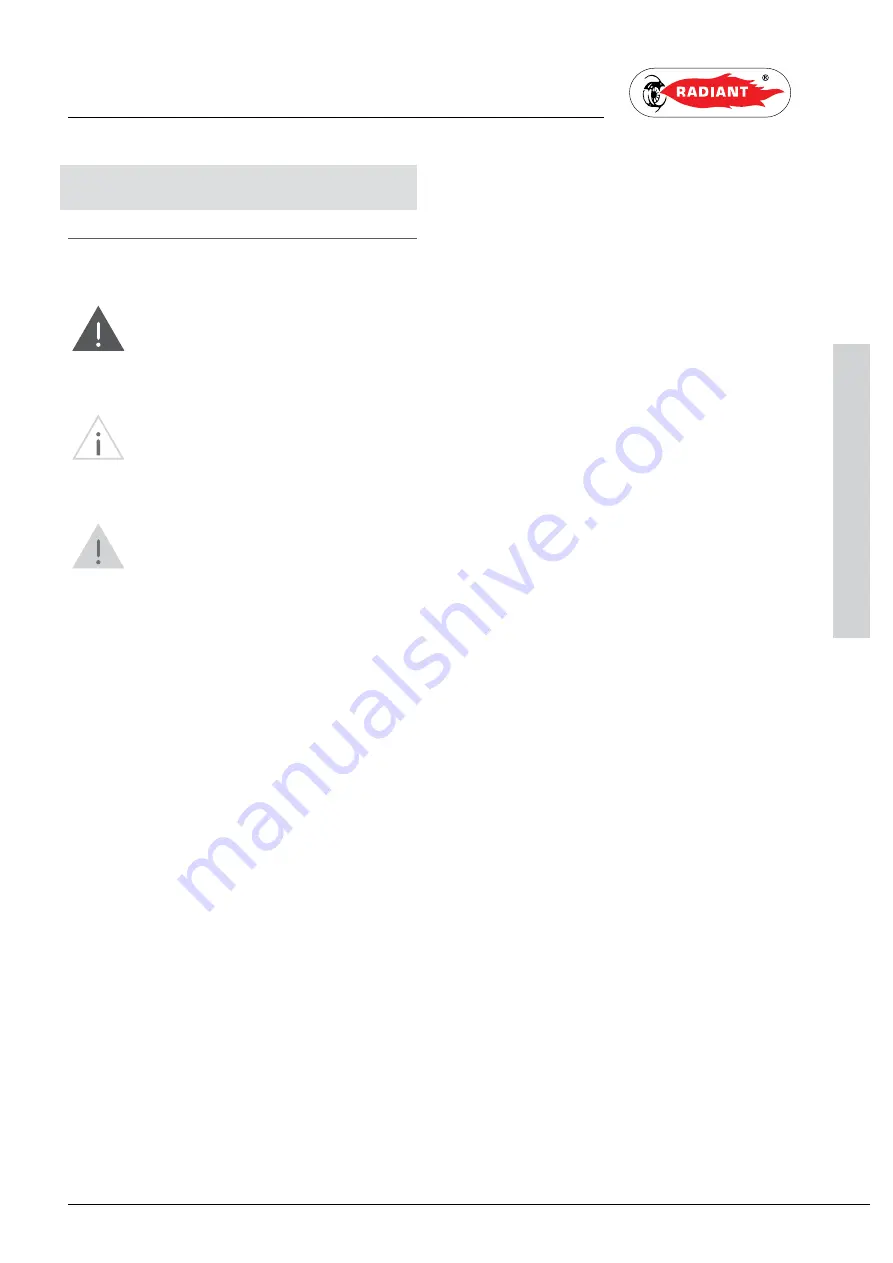
43
R1BK_50-RAD-ING-Manuale-1812.1_SK.3
2 Av
ver
ten
ze gen
er
ali p
er
la m
anu
ten
zio
ne
_s
olo
risc
_co
nd
_E
N
2 Av
ver
ten
ze gen
er
ali p
er
la m
anu
ten
zio
ne
_s
olo
risc
_co
nd
_E
N
2. MAINTENANCE
SUPPOR
T CENTRE
2.2. MAINTENANCE
2.2.7. GENERAL MAINTENANCE
WARNINGS
DANGER
Before each components cleaning or
replacement operation, ALWAYS cut off the POWER,
WATER and GAS supply of the boiler.
WARNING
To ensure greater life span and proper
operation of the device, during the maintenance
operations use only original spare parts.
ATTENTION
To ensure the efficiency and safety of the
device, the maintenance operations must be realized
on an annual basis. The operations described below,
are essential to the validity of the standard RADIANT
warranty and must be performed by professionally
qualified personnel in accordance with current
legislation and authorized by RADIANT.
Please perform the following operations once a year:
› Check that the system’s water PH is between 7 and
8.5;
› check the sealing of the gas components, and
replace if necessary the gaskets;
› check the sealing of the water components, and
replace if necessary the gaskets;
› visually check the flame and the condition of the
combustion chamber;
› if necessary make sure that the combustion
is suitably adjusted and if required proceed as
indicated in section “CO2 VALUE CHECK AND
CALIBRATION”;
› remove and clean the burner from oxidation;
› check the integrity and the position of the sealed
chamber sealing gasket;
› check the primary exchanger, if necessary, clean
it;
› check the operation of the gas light up and safety
systems. If necessary, remove and clean the
flame detection and light up electrodes from
incrustations paying attention to respect the
distances with respect to the burner;
› check the heating circuit safety systems: limit
temperature safety thermostat; limit pressure
safety;
› check the pre-load pressure of the expansion
vessel;
› make sure that the permanent ventilation outlets
are present, correctly sized and functioning, based
on the installed devices. Respect the requirements
provided by Local and National legislation;
› periodically check the integrity of the fume
exhaustion system for safety and proper operation;
› check that the wiring is performed in compliance
with the requirements in the boiler instruction
manual;
› check the wiring inside the control panel;
› check the proper operation of the condensate
draining system, including the devices outside
the boiler such as condensate collection devices
installed along the path of the fume exhaust duct
or neutralization devices for acid condensate.
› check that the liquid flow is not obstructed and that
there are no combustion gas refluxes inside the
internal system.