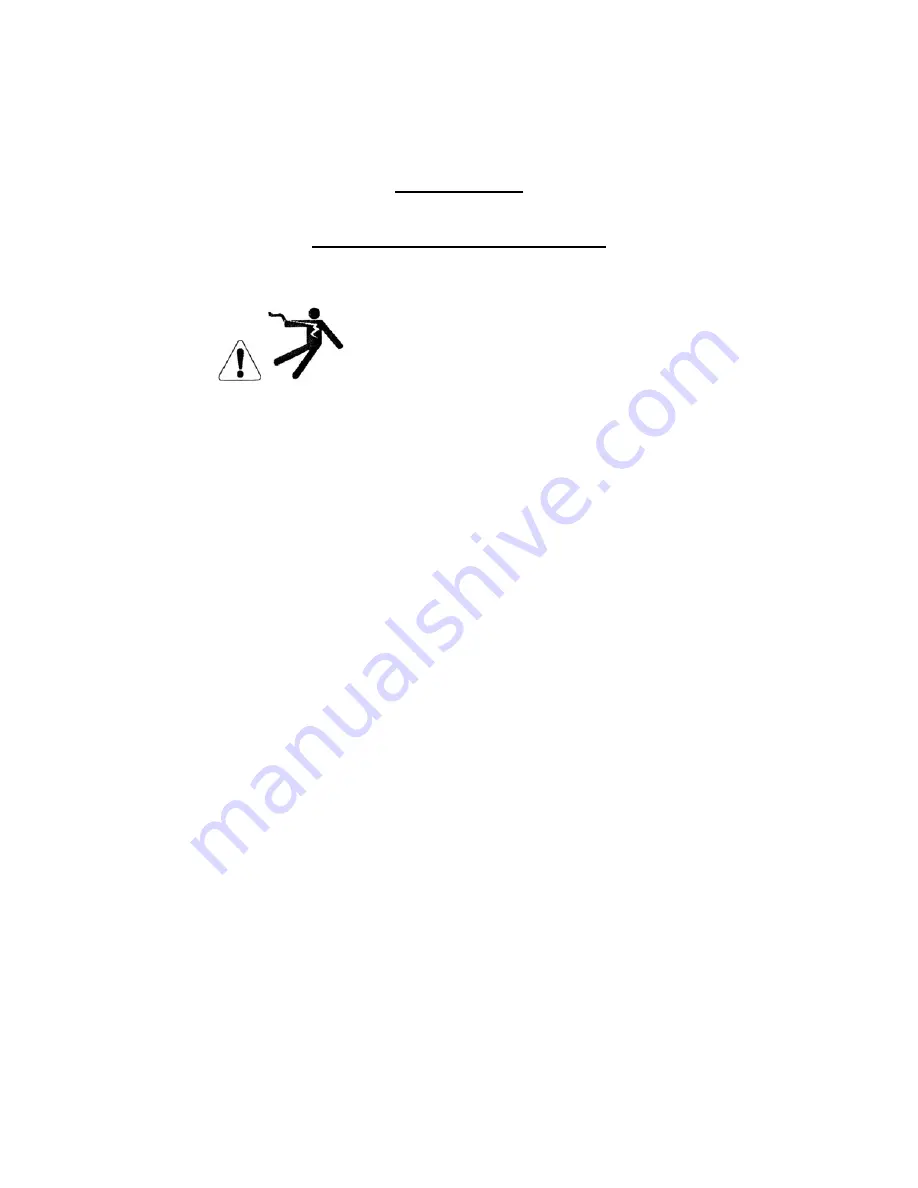
14
Maintenance
Routine and periodic maintenance
WARNING!
ELECTRIC SHOCK CAN KILL
Turn the input power OFF at the mains switch & fuse box and remove mains plug from socket
before working on this equipment.
Have a qualified electrician install & service this Plasma cutting equipment.
Allow machine to sit for 5 minutes minimum after disconnection from mains power to allow the
power capacitors to discharge before working inside this equipment.
Do not touch electrically live parts
1. Periodically (3-6 months depending on use / environment), remove the side/top panels of
machine and clean out machine with a low pressure dry air line paying particular attention
to PC Boards, Fan blades and switchgear
Failure to maintain plant can void manufacturers warranty.
2. Inspect input and output cables & hoses for fraying and cuts, replace if damaged present
3. Keep cutting torch and earth cables in good condition
4. Clean air vents to ensure proper air flow and cooling
5. The fan motor has sealed bearings which requires no maintenance
Summary of Contents for P100HF
Page 1: ...P100HF PLASMA CUTTER OPERATION INSTRUCTIONS www r techwelding co uk ...
Page 2: ...2 ...
Page 17: ...9 ...
Page 18: ...18 ...
Page 19: ...19 ...