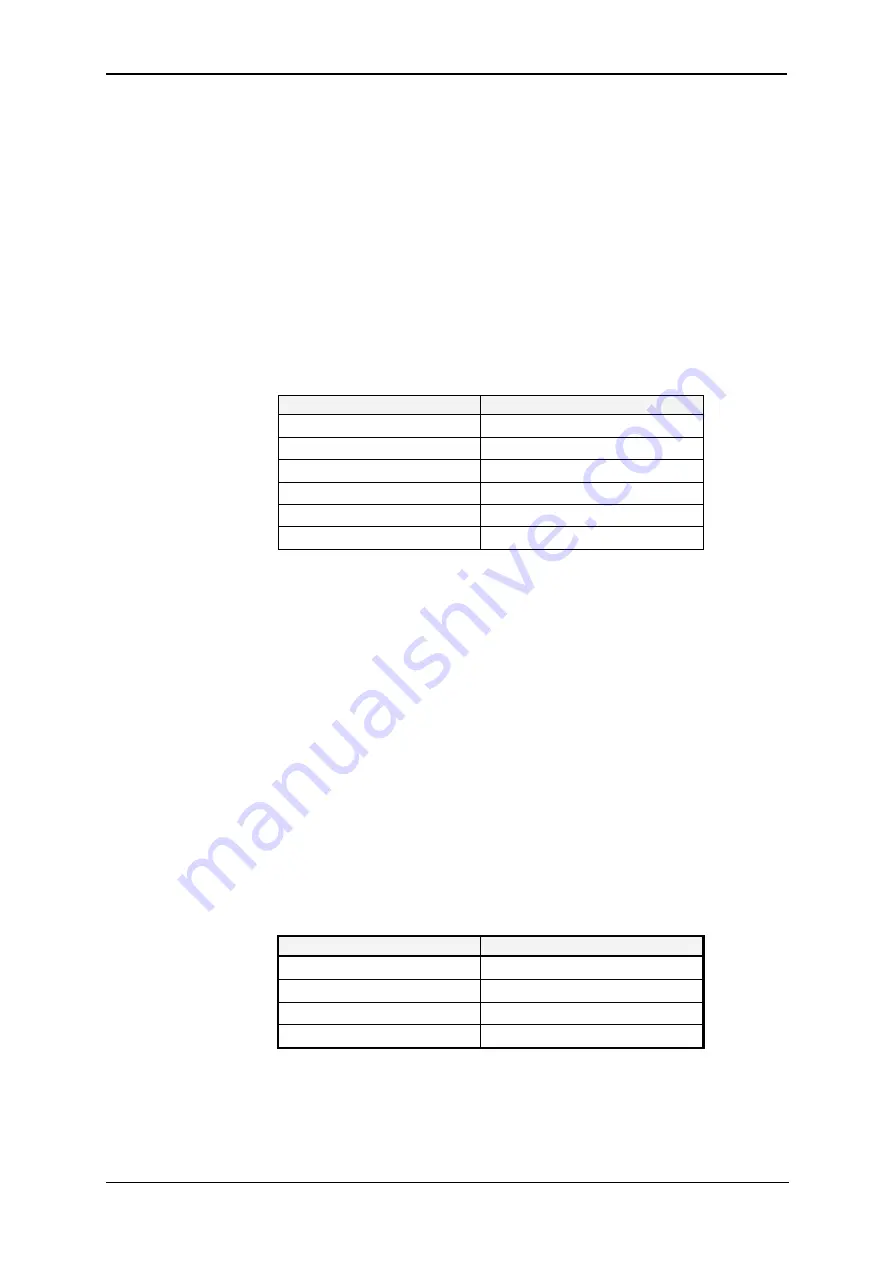
Q150T Sample Preparation System
10473 - Issue 5
32
Q150T - Instruction Manual
5.4
Pulsed Cord Evaporation
This process is designed for preparing conductive carbon coatings for SEM specimens
for X-ray microanalysis EDX and WDX. It is only available with Q150T E/ES models
equipped with the carbon cord insert option.
5.4.1
How to create a 20nm carbon coating
1.
Install the carbon cord insert as described on page 58.
2.
Ensure the stage is fitted with the shorter support shaft to give the maximum
source-to-stage distance.
3.
Create a new profile based on
QT Pulsed cord evaporation
.
4.
Edit the newly created profile setting the parameters as shown in Table 5.
5.
Run the new profile.
Table 5
QT Pulsed cord evaporation parameters for 20nm coating.
Parameter
Value
Pulse Current
50A
Pulses Length
3 seconds
Number of Pulses
1
Out Gas Time
60 seconds
Out Gas Current
30A
Pump Hold
Yes
5.5
Controlled Pulse Cord Evaporation
This process is used for preparing conductive carbon coating using carbon cord.
During the process the coating is built up of multiple thin layers using short current
pulses (see Figure 5-2). This reduces the heating effect on the sample and allows the
FTM to be used to terminate the coating.
5.5.1
Using Controlled Pulse to create a 15nm coat or 2-3nm for EBSD
6.
Install the carbon cord insert as described on page 58 ensuring that the C5421
carbon cord is used. Note the springs in the insert must be removed to ensure that
the cord does not fuse prematurely.
7.
For the default tooling factor to be valid the stage should be fitted so the top of the
sample is 60mm above the base plate.
8.
Create a new profile by pressing the new button in the profile viewer and selecting
Controlled pulse cord
.
9.
Edit the newly created profile setting the parameters as shown in Table 6. If an
EBSD coating is required, set the terminate thickness to the required thickness i.e.
3nm.
Table 6
QT Controlled Pulsed cord evaporation parameters for 25nm coating.
Parameter
Value
Terminate thickness
15 nm
User selectable
Pulse Current
54A
Pulses Length
1 seconds
Pulse Interval
10 seconds
The remaining properties have been optimised for coatings between 2 and 15nm
with the top of the sample 60mm from the base plate. Thicker coatings at this
stage position can be achieved. However this will increase the risk of the cord
fusing before reaching the required thickness. If the cord does fuse it tended to
deposit about 6nm, thus it can cause the required thickness to be exceeded. In
Summary of Contents for Q150T S
Page 92: ......