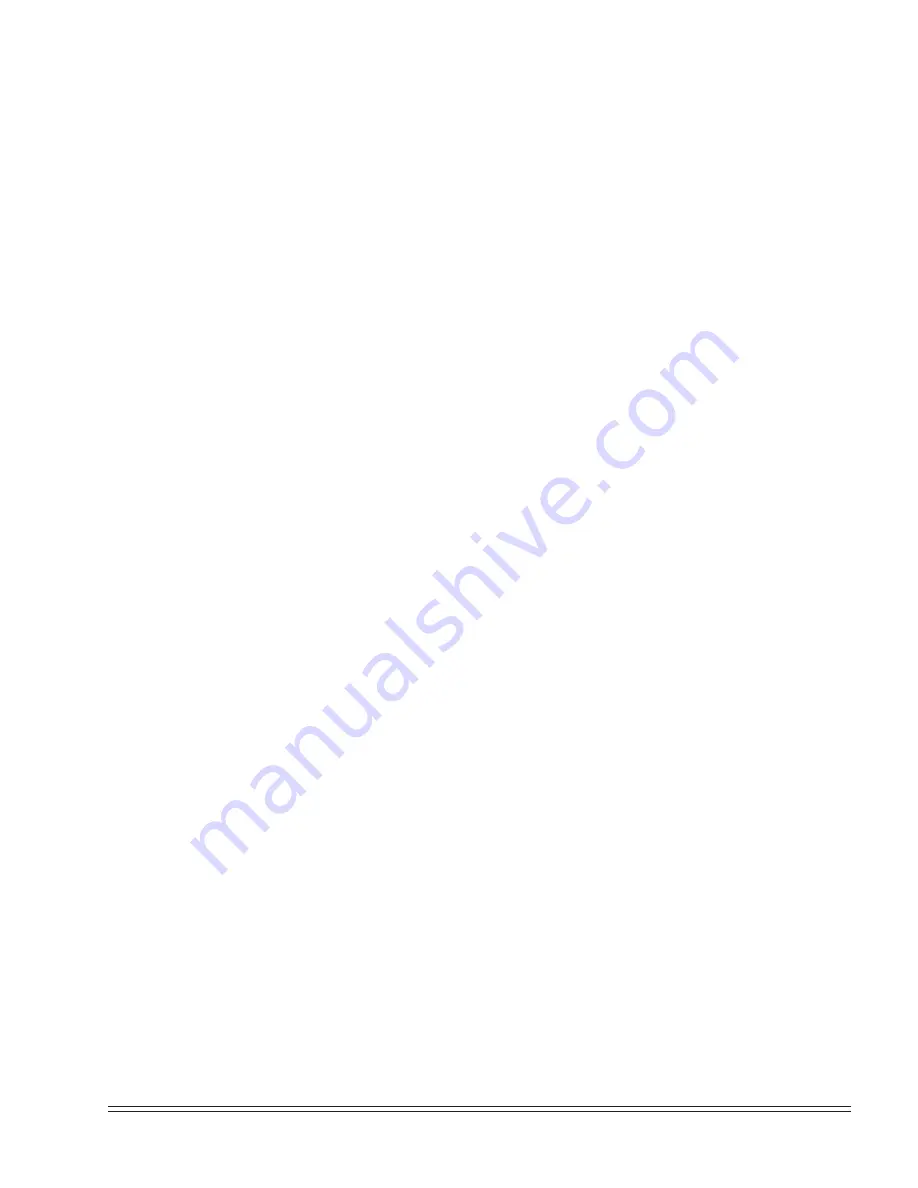
QT/QTS Series
Quincy Compressor
2022208700, September 2018
27
Pressure Switch
The pressure switch detects the demand for compressed air and allows the
motor to start. When the demand is satisfied, the unit stops. Pressure switches
provided by Quincy Compressor are pre-set at the factory and usually do not
require adjustment.
Induction System
Air Intake
A clean, cool and dry air supply is essential to the satisfactory operation of
your Quincy air compressor. The standard air filter that the com pressor is
equipped with when leaving the factory is of sufficient size and design to meet
normal conditions, when properly serviced, in ac cordance with the maintenance
section of this manual.
If, however, the compressor is to be installed in a location where considerable
dust, dirt and other contaminants are prevalent, consult your local Quincy
distributor for advice and optional filters. A condensate trap must be installed as
close as possible to the inlet filter if, as a result of installation or environmental
conditions, there is any risk of moisture forming in the inlet piping. It is the
user’s responsibility to provide adequate filtration for those conditions. Oil
bath filters are not to be used. Warranty will be void if a failure is determined
to be caused by inadequate filtration.
Remote Inlet Filters
Depending on the size of the compressor and the size and construction of the
room in which the unit operates, the air inlet may have to be located outside
of the room. If it is necessary to remotely install the air filter, make the inlet
piping as short and direct as possible. Remotely in stalled air filters can lead
to vibrations in the inlet piping. These vibra tions can be minimized by adding
a pulsation dampener in the inlet piping between the remote inlet filter(s)
and the compressor.
If the inlet is routed to outside atmosphere, the inlet piping should be
equipped with a hooded air filter and designed to prevent condensate, water
or snow from being ingested into the compressor.
All inlet piping should be at least the same size (or larger) in di ame ter
as the inlet connection to the compressor. For every 10 feet of inlet piping or
every 90° bend, increase the inlet piping diameter by one pipe size. The inlet
piping must be thoroughly clean inside. Remove all weld slag, rust or dirt.
Galvanized pipe with threaded or flanged fittings is preferred.
Never locate the compressor air inlet system where toxic, volatile
or corrosive vapors, air temperatures exceeding 100°F, water, or
extremely dirty air could be ingested. These types of at mospheres
could adversely affect the performance of the compres sor system.
Compressed Air Discharge System
The discharge piping should be of the same diameter as the compressor
discharge connection, or sized so that the pressure drop at any point in the
CAUTION !
Summary of Contents for QT Series
Page 2: ......