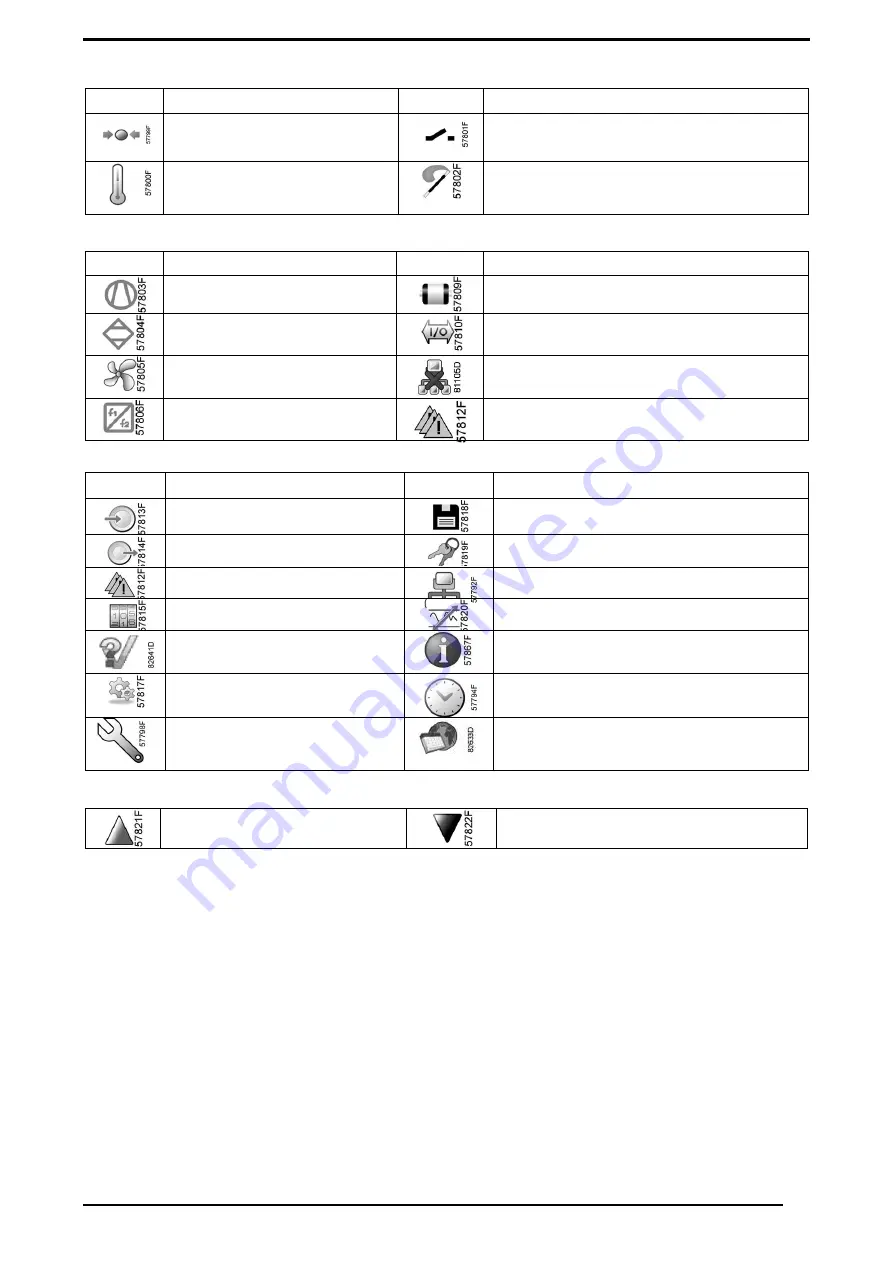
ENGLISH
.
Cod. 9828093052 04 - Edition 02/2018 - 17
Input icons
Icon
Description
Icon
Description
Pressure
Digital input
Temperature
Special protection
System icons
Menu icons
Icon
Description
Icon
Description
Inputs
Event history (saved data)
Outputs
Access key / User password
Protections (Warnings, shutdowns)
Network
Counters
Setpoint
Test
Information
Regulation (Settings)
Week Timer
Service
General
Navigation arrows
Main screen
Function
The Main screen is the screen that is shown automatically when the voltage is switched on and one of the keys is pushed. It is switched off
automatically after a few minutes when no keys are pushed.
Typically, 5 different main screen views can be chosen:
Two value lines
Four value lines
Chart (High resolution)
Chart (Medium resolution)
Chart (Low resolution)
Two and four value lines screens
This type of Main screen shows the value of 2 or 4 parameters (see section Inputs menu).
Icon
Description
Icon
Description
Compressor element (LP, HP, ...)
Motor
Dryer
Failure expansion module
Fan
Network problem
Frequency converter
General alarm
Up
Down