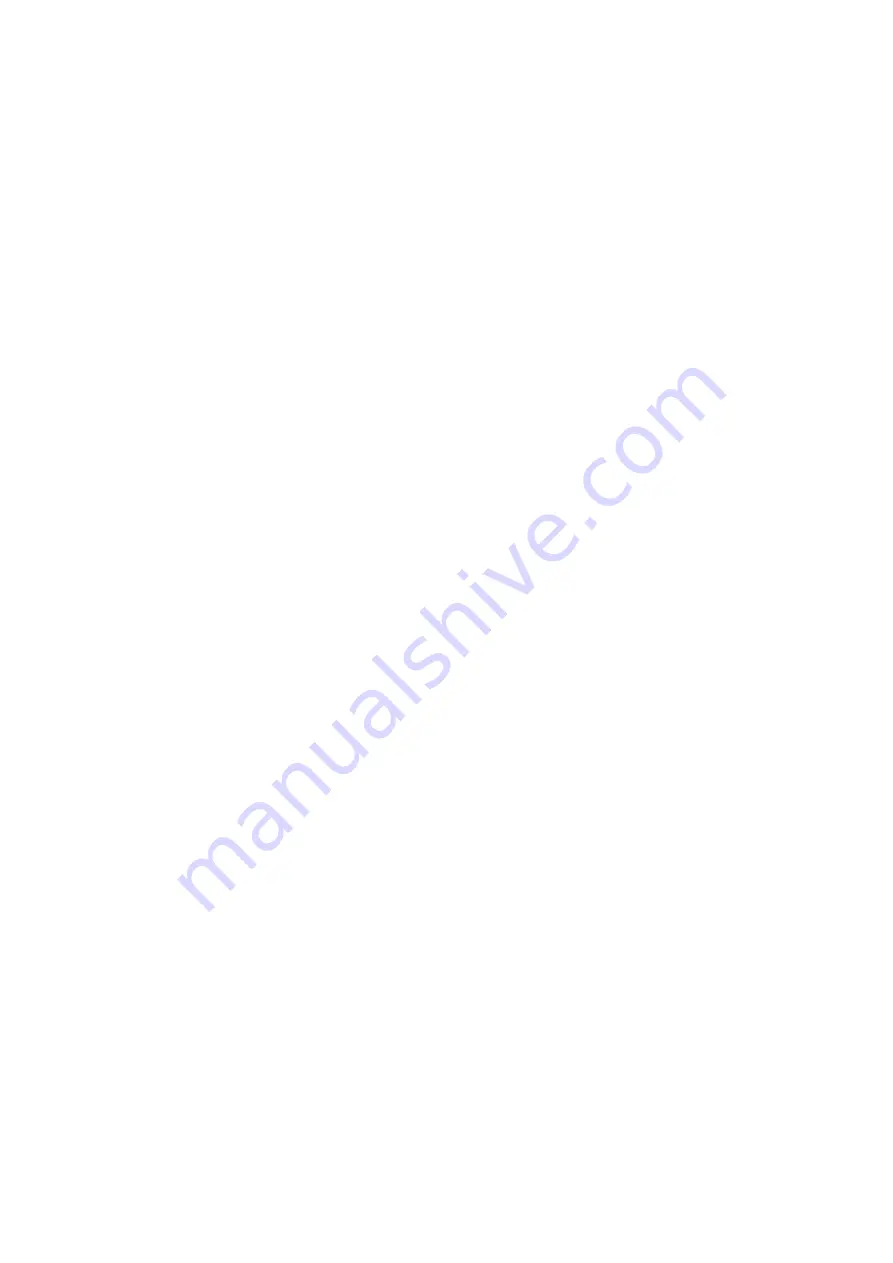
Issue 1.5
Q-Drive Installation Manual
Copyright © 1996 Quin Systems Ltd.
Page 31
In most cases, the inertia and friction can be assumed constant, unless the system has a
changing load. In this case the maximum possible load should be used in the
calculations. The required velocity profile of the motor should be sketched out by
plotting motor velocity against time. The slope of this gives the motor acceleration, and
thus the maximum required acceleration can be found from the steepest slope on the
graph. This acceleration value can then be substituted in the torque equation for a given
motor to see if the motor is powerful enough to do the job.
This can be repeated along the velocity-time plot for all accelerations to give a graph of
torque against time. This can be used to find the average or r.m.s. continuous torque
required by the system. Servo motors are often specified with both a continuous and a
peak torque rating, and they should be chosen such that the torque requirement of the
machine is well within the capacity of the motor. Care must also be taken to ensure that
the maximum speed of the motor is not exceeded.
Note that if too large a motor is selected, the motor inertia is higher than for a smaller
motor. This affects the maximum acceleration that the motor produces. It is not always
the largest or most powerful motor that accelerates the load at the quickest rate. Also
note that maximum power transfer from the motor into the load is obtained if the motor
inertia and reflected load inertia are similar.
The ideal motor should have as high a torque to inertia ratio as possible. Pancake or
printed armature motors are often used because they have low rotor inertias. This is also
another advantage of brushless motors, in that they have low rotor inertias because the
rotor often does not have any electrical windings but consists simply of a permanent
magnet on a shaft. Brushless motors also exhibit better heat dissipation from their
wound stator.