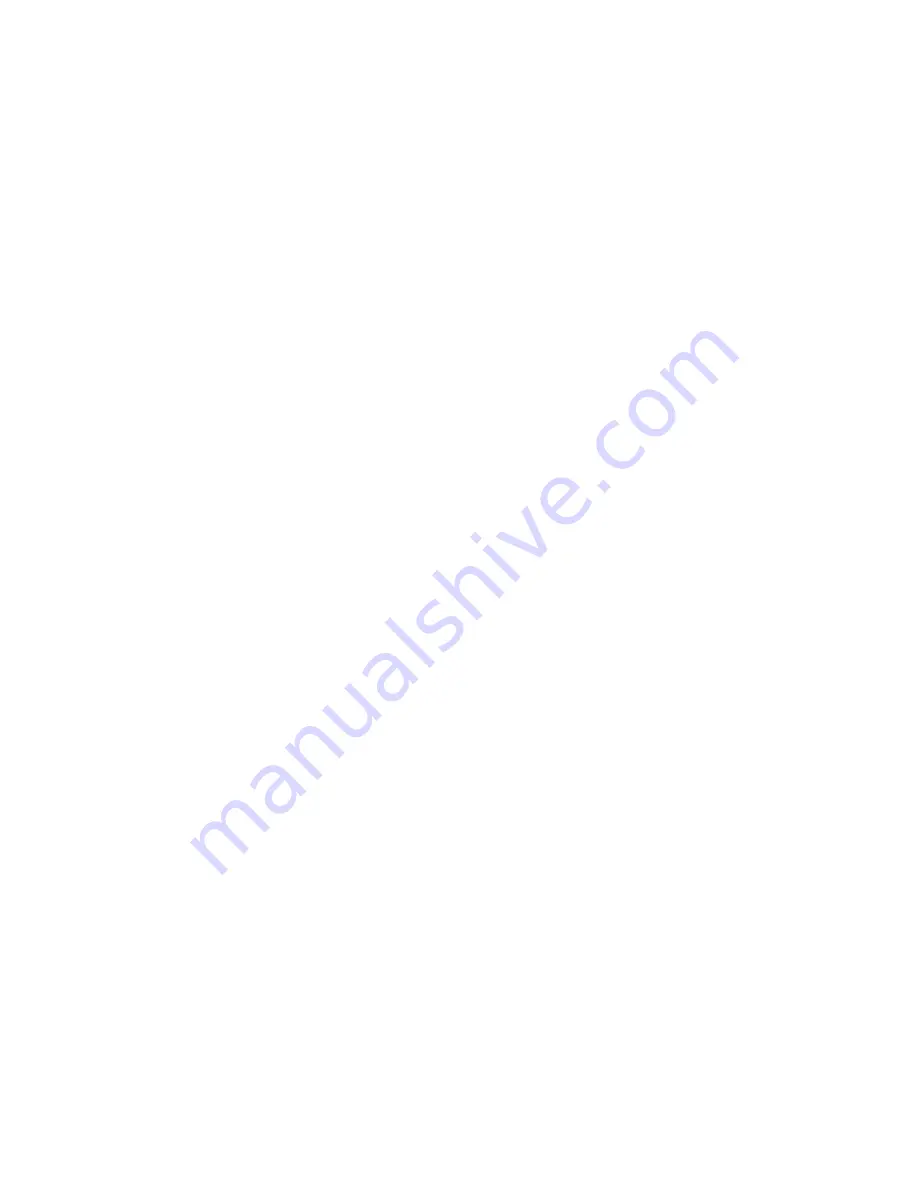
QL-800 High Volume
Maintenance Guide
Part Number 9006-0000004
Revision 1.0
4/2019
QuickLabel, An AstroNova™ Division
World Headquarters
600 East Greenwich Ave., West Warwick, RI 02893
Tel: (877) 757-7978 Fax: (401) 822-2430
E-mail: [email protected]
www.QuickLabel.com
Technical Support
Tel: (877) 757-7310
E-mail: [email protected]
www.QuickLabel.com/support/