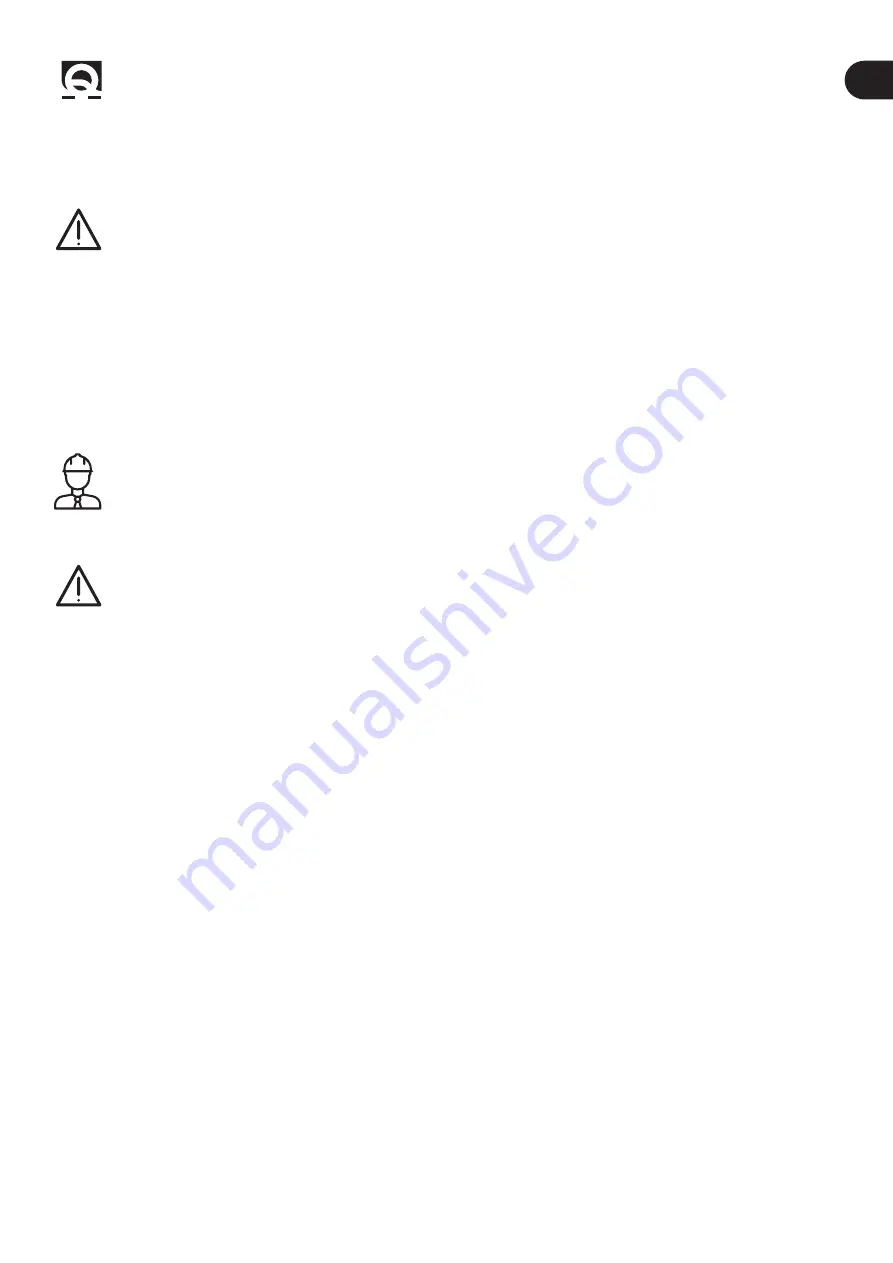
EN
BTR
Series
QUICK
BTR Series
INSTALLATION AND USER’S MANUAL - REV 001C
7
3.1 - Precautions
Quick® thrusters have been designed and constructed only for nautical use.
• Do not use these products for any other type of operation.
• Quick
®
shall not be held liable for direct or indirect damage caused by improper use of the product.
• The product is not designed to support loads generated in particular atmospheric conditions (storms).
• Operate the product from a position where it is possible to supervise the work area.
• Always deactivate the thruster when not being used.
• For improved safety, we recommend installing at least two controls to operate the product in case one is damaged.
• The installer shall bear full responsibility for any problems caused by defective installation of the tunnel.
• This equipment is not intended for use by people (including children) with reduced physical, sensory or mental
capabilities.
•
Do not install the electric motor near easily inflammable objects.
3.2 - Precautions for the installer
CARRY OUT THE INSTALLATION IN GOOD LIGHTING CONDITIONS.
It is advisable to wear suitable clothing and personal protective equipment (PPE).
The product is not suitable for installation in potentially explosive environments and/or atmospheres.
Installation and subsequent inspection or repair work must only be carried out by qualified personnel.
CARRY OUT INSTALLATION/MAINTENANCE WORK MAKING SURE THAT THE PRODUCT IS DISCONNECTED
FROM THE ELECTRICAL SYSTEM.
Quick
®
accepts no responsibility for inadequate connection of users to the electrical system and inadequate safety of
the electrical system.
3.3 - Installation requirements
We recommend you entrust preparation and positioning of the tunnel in the hull to a skilled professional.
These are generic instructions and do not give details of the preparatory operations for installing the thruster, since this is the
competence of the boatyard. The installer shall bear full responsibility for any problems caused by defective installation.
Although all the components and mechanical moving parts are of high quality, the correct installation of the driving unit is an
essential basis for the safe and effective use of the boat as well as the driving unit itself.
The installation of such a unit is an operation that requires experience as well as technical skills. It is recommended that the
installation be carried out by competent personnel and that the manufacturer or naval architects be consulted to fully assess
the scope of the work.
The Quick® retractable thruster has two separate movements.
The main movement
, relative to the driving unit, is of the tilting type. The hinges on which the movement takes place are
designed for assembly high resistance and are located on the plane of the flat flanging that links the pre-assembled structure to
the support integral to the hull.
The secondary movement
relates to the closing movement of the thru-hull from which the tunnel comes out. This tilting
movement is performed around the hinge that has been designed and manufactured for an interference-free opening of the
hatch (if installed as instructed).
Electric motor, gearbox, linkages and all other components are supplied by Quick® already assembled on the GRP
support structure
and do not require adjustments, adaptations or sealing, unless specified in this manual.
The Quick® retractable thruster is sold separately from the counter flange
which can be supplied in different materials
based on the different type of hulls. Quick® can provide stainless steel, aluminium alloy or GRP supports, which are essential for
a fast, sturdy and precise installation.
For fibreglass hulls
, the support must be laminated in the hull in compliance with current regulations on joints.
The driving unit distributes mechanical stresses to the hull through the counter flange. The strength of the joint will be
determined by overlapping laminations, made in a “workmanlike” way.
For aluminium alloy hulls or stainless steel hulls
, the support needs to be welded to the hull.
If well done, the installation of a box structure such as that of the support can give greater strength to the hull. Refer to the
manufacturer, naval architects and/or specialised companies to evaluate additional works such as beams and supporting
structures near the position of the retractable driving unit.
3 - Introduction