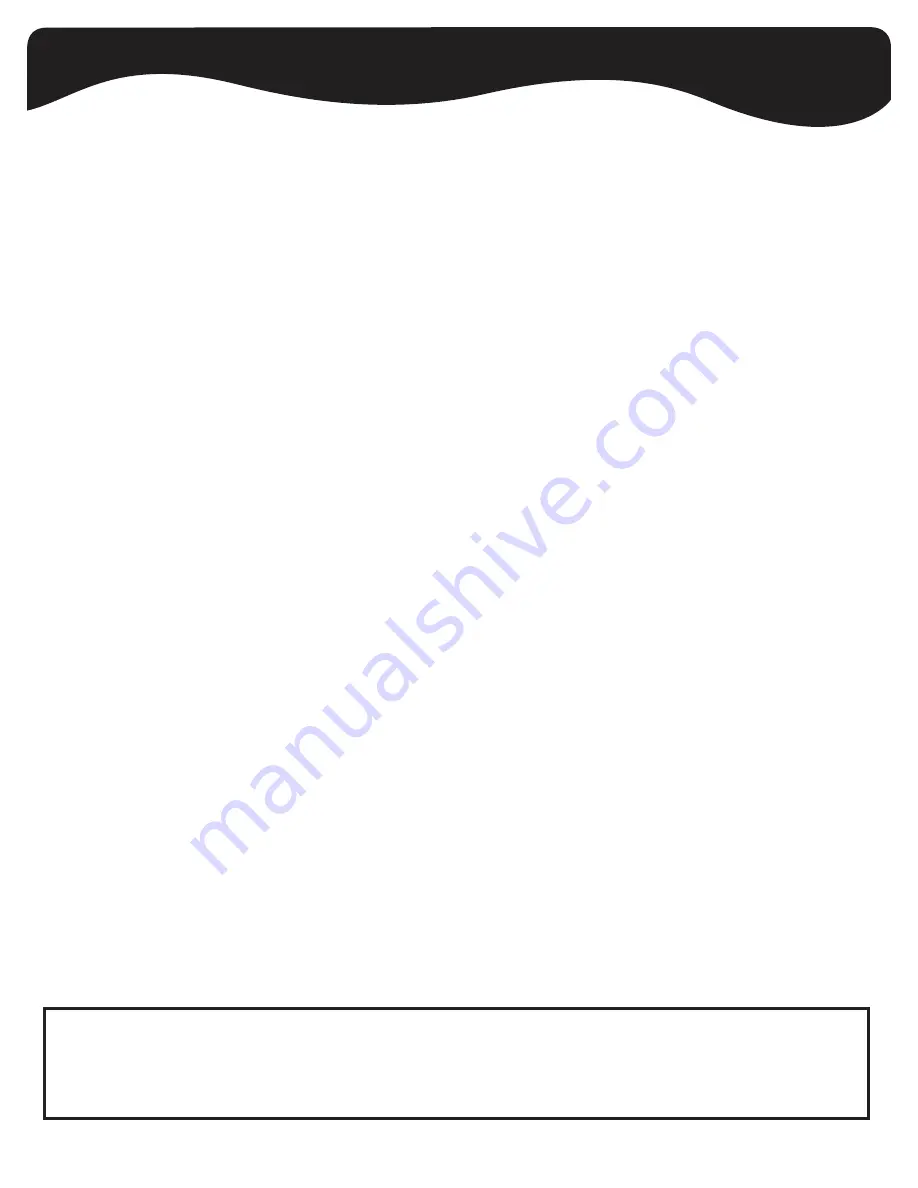
General Installation Instructions
Proper installation of your RK2 System pump will help insure years of trouble free service.
1. Position the pump as near to the water and as low as is practical. This will help reduce cavitation and maximize your pumps output.
2. Protect the motor from excessive heat and moisture. It is best to provide shade from direct sun, and insure that it has proper ventilation.
Excessive heat will shorten the motors life and void the warranty.
3. Protect the motor against dirt, water, corrosive salt build up, and all foreign matter. If the motor has been flooded, shut off power and
do not operate it until it has been checked by an authorized motor technician, and it has been certified safe to operate. If the motor is
damaged by dirt or moisture it voids the warranty.
4. Mount the motor to a stable base where it won’t get submerged.
5. The pump ports are 1 1/2” NPT female on both the inlet and discharge. The fittings used to connect to the housing should be plastic. All
plumbing lines should be self supported and properly aligned. This will prevent undue stress to the housing. Use teflon paste (not tape) to
connect your fittings to the pump.
6. The intake to the pump should not be restricted. Keep your suction lines as free of elbows, fittings and valves as possible. The use of larger
diameter pipe will help minimize friction loss.
7. This is a non self-priming pump and is best suited with a flooded suction. Do not run the pump dry. The pump housing, and the entire
suction line must be filled with fluid for it to operate properly.
Electrical
1. If you are not competent to wire an electric motor, hire someone who is!
2. Make sure the power is disconnected at the breaker before wiring the motor.
3. Make sure that the motor is wired internally so that it matches the supply voltage. If they do not match it will damage your motor and void
the warranty. Ex. if you are connecting it to a 115V breaker, make sure the motor connections match the 115V (low) wiring diagram found
on the motor. Always follow the schematic on the motor for all electrical connections. NOTE: Baldor motors have separate wiring
schematics for low (115V) and high (230V) applications. Both schematics are shown for dual voltage motors.
AO Smith motors use a switch to change between low (115V) and high (230V) on dual voltage motors. This switch is located under the rear
cover on the back of the motor. The wiring schematic is the same for these motos since the switch determines the voltage selected.
4. Use a supply wire of adequate gauge to prevent electrical line losses. This will allow the motor to run cooler and more efficiently,
by eliminating excessive line voltage loss.
5. Make sure all connections are clean and tight. Properly ground the motor. (There is normally a green ground terminal located inside the
motor connection box.) Make sure the ground wire is properly connected to an electrical service ground.
6. Connect the pump permanently to an adequately sized circuit. It is best to have a dedicated circuit that won’t suffer voltage drop
from other loads.
7. Insure proper motor rotation. When viewed from the shaft end, the motor must rotate counterclockwise. Incorrect rotation will destroy the
pump and motor.
Note: The motor leads must be energized in the correct order. If you are not sure of the sequence of your incoming supply line,
remove the volute from the pump, connect the power and check rotation. When the rotation is correct, reinstall the volute.
Do not test with volute in place! Never test rotation by bumping a switch!!! This will destroy the pump and void the warranty!!!
If it is incorrect, exchange any two of the connected leads and retest.
INSTALLATION