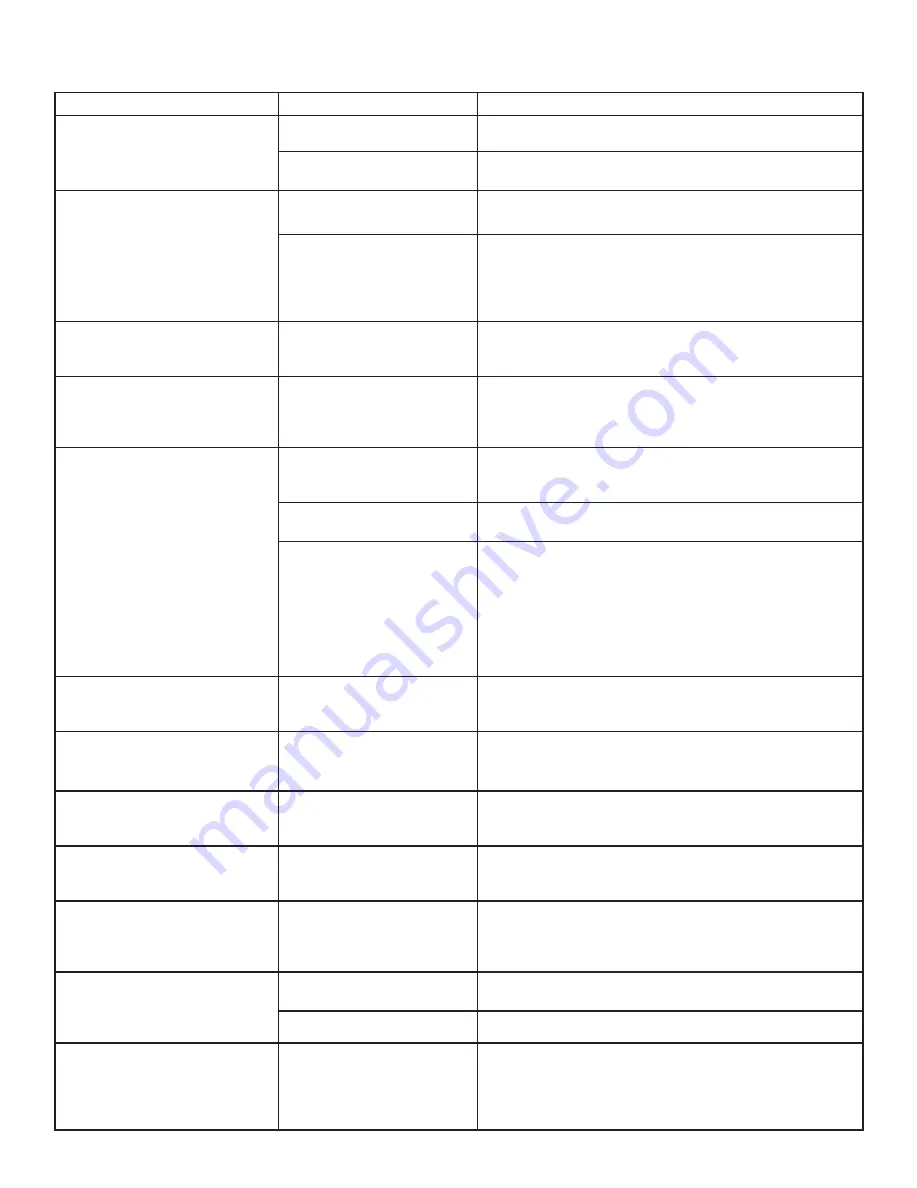
19
Quadra-Fire • QFI30FB-IFT, QFI35FB-IFT Owner’s Manual • 2555-981 Rev. L • 10/20
B. Frequently Asked Questions - IntelliFire Touch Controls (IFT-RC400)
Symptom
Possible Cause
Corrective Action
The appliance does not respond to
commands from the remote control
display does not light up when
screen is touched.
Batteries are depleted.
Verify batteries are new.
Batteries are incorrectly
oriented.
Verify batteries are installed in correct orientation as shown on
batteries receptacle.
The display on remote lights up
when screen is touched but it does
not respond to commands.
Touchscreen has lost
calibration.
Touchscreen needs to be re-calibrated. Call dealer to have
screen re-calibrated.
Child Lock is ON.
Check child lock icon located at the top of the remote display. If
ON, it will show as a ‘locked’ symbol. To unlock, remove battery
compartment door, locate child lock switch and move to ‘unlock’
position. Verify child lock icon on screen is now displayed in ‘un
-
lock’ position.
The remote displays the following
message on-screen:
No dealer info available.
Dealer information not
programmed into remote.
Remote will still provide all available functions, and appliance is
fully available for use. Call dealer to have them program.
The remote displays the following
message on-screen:
Call “Dealer Name & Number” to
schedule maintenance.
300 hours of use. Appliance is
still fully functional.
The appliance has been burning for 300 hours and is due for a
regular maintenance. Call dealer to have them perform mainte-
nance.
The room temperature displayed
on the remote is either slow or
quick to respond while operating in
thermostat mode.
Remote is placed at a very
short distance or too far away
from the appliance.
Try to keep the remote close to the appliance but not directly in
front of it. The remote acts as the thermostat.
Remote is placed in the path of
an air draft or vent.
Move the remote away from the direct path of air flow. The re
-
mote acts as the thermostat.
Flame Modulation
The control system is designed to automatically adjust the
flame intensity based on the difference between the desired
room temperature, and actual temperature. In thermostat
mode, the hearth appliance will start in HI flame, but as the
actual temperature approaches the desired set temperature on
the remote, the flame intensity will automatically decrease. Au
-
tomatic flame modulation will result in more control of the tem
-
perature, and will cause the appliance to cycle OFF/ON less.
The appliance turns OFF the flame
after extended periods of operation. 9 hour safety shutdown timer
This is normal behavior. The appliance has a safety timer that
will automatically turn OFF the flame after nine hours of
uninterrupted operation.
The remote displays the following
message on-screen: Fan will turn
on within 3 minutes.
Functioning as intended.
The appliance has a three minute delay timer before the fan is
turned ON. This allows the air surrounding the appliance to be
heated before being pushed into the room.
The remote displays the following
message on-screen:
“Replace remote batteries."
Low batteries in remote.
Install new batteries in the remote.
The remote is displaying an
incorrect brand.
Remote was programmed
incorrectly.
Call dealer to have them program the remote with correct
branding. Remote is still fully functional and the appliance is
unaffected.
After turning flame ON using
remote, the flame does not turn
ON immediately and instead a two
minute timer is displayed.
Power vent is installed on the
appliance.
This is expected behavior and the two minute timer is called a
pre-purge timer. The flame will turn ON at the expiration of the
timer.
The remote displays the following
message on-screen:
“Remote Control Communication
Error.”
No power to appliance.
Verify home circuit breaker is on and master reset is on (if
equipped).
Power outage.
Install new batteries in battery backup.
The remote displays the following
message on -screen: Sorry your
appliance did not start. Try again
by pressing Flame On.
No power to appliance. No gas
to appliance. Accumulation
of air in gas line from extended
period of appliance inactivity.
Gas control system failure.
Verify that appliance has power and gas. Verify that the appli-
ance accepts flame ON commands with an audible beep, and
successfully turns flame on within 90 seconds. If this failure
persists, contact dealer for service.