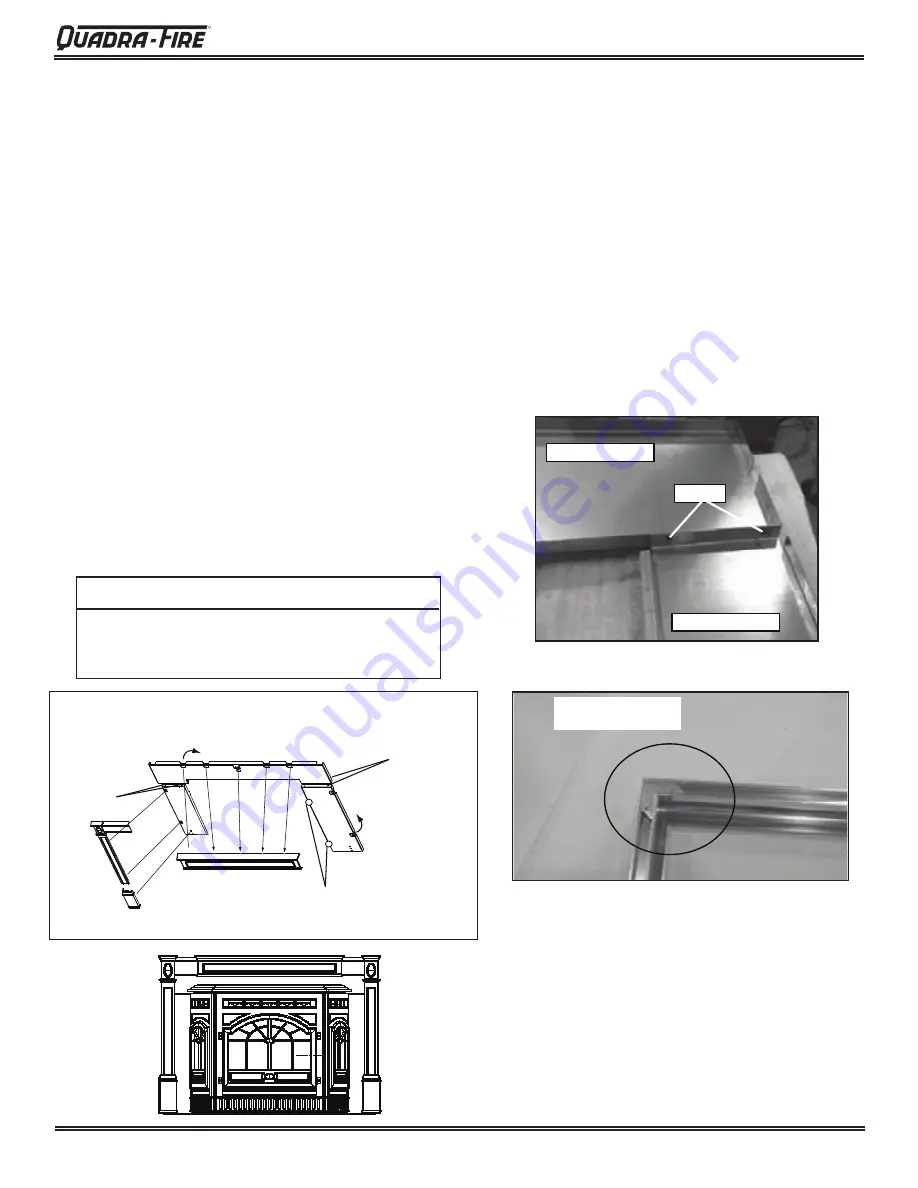
R
August 20, 2009
250-7251G
Page 21
Castile Pellet Insert
E. Panel Set And Cast Trim Set
1. Screw panels
together
2. Bend tabs down
1. Screw panels
together
3. Install Cast Trim Header
2. Bend tabs
down
Mounting tabs on each panel leg
to match up with slots on insert.
Included in Panel Kit:
(2) side panels, left and right; (1)
panel top; (1) fastener package.
Included in Cast Trim Kit:
(2) cast trim legs, left and right; (1)
cast trim header; (2) cast trim footers, left and right; (1) fastener
package.
Tools Needed:
Powered Phillips head screw driver
F. Panel & Trim Set, Econo
1. Secure the top panel to the panel sides with the
screws provided.
Figure 21.3
.
2. Assemble the gold trim with the (2) corner brackets
provided.
Figure 21.4.
3. Slide the assembled trim over the assembled panel
set.
4.
Slide panel and trim over the top of the insert into
place matching the mounting tabs on the panel with
the slots on the insert.
Back of Top Panel
Back of Side Panel
Screws
1. Remove contents from box being careful not to scratch or
damage the cast trim pieces.
2. Lay the panel set face down on protective covering to prevent
scratching the painted surface.
3. Secure the panels legs to top panel with the screws provided.
4. Now bend the tabs down toward the backside of the panel set,
5 on top and 2 on each leg. Leave the panel set face down.
5. Place the corresponding cast trim pieces ( 2 cast trim legs and
1 cast trim header) underneath the panel set, also face down.
6. Place washer provided over tab and secure the trim and panel
together with screw. Continue for all tabs.
7. Secure cast footers with screws.
8. Remove both left and right cast sides from insert,
See Figures
32.1, 32.2 and 32.3 on page 32.
9. Slide panel and trim over the top of the insert into place matching
the mounting tabs on the panel with the slots on the insert.
Included in Panel & Trim Kit:
(2) corner brackets and set
screws; (1) trim set, 3 piece; (2) side panels; (1) top panel;
(4) screws;
Tools Needed:
Powered Phillips head screw driver
•
Do NOT pick up assembled unit by corners.
•
It is too heavy and may damage the panels.
•
Pick up from center.
CAUTION
Figure 21.1
Figure 21.2 - Completed View
of Panel Set & Cast Trim Set
Figure 21.3
Figure 21.4
View of "L" Bracket
installed