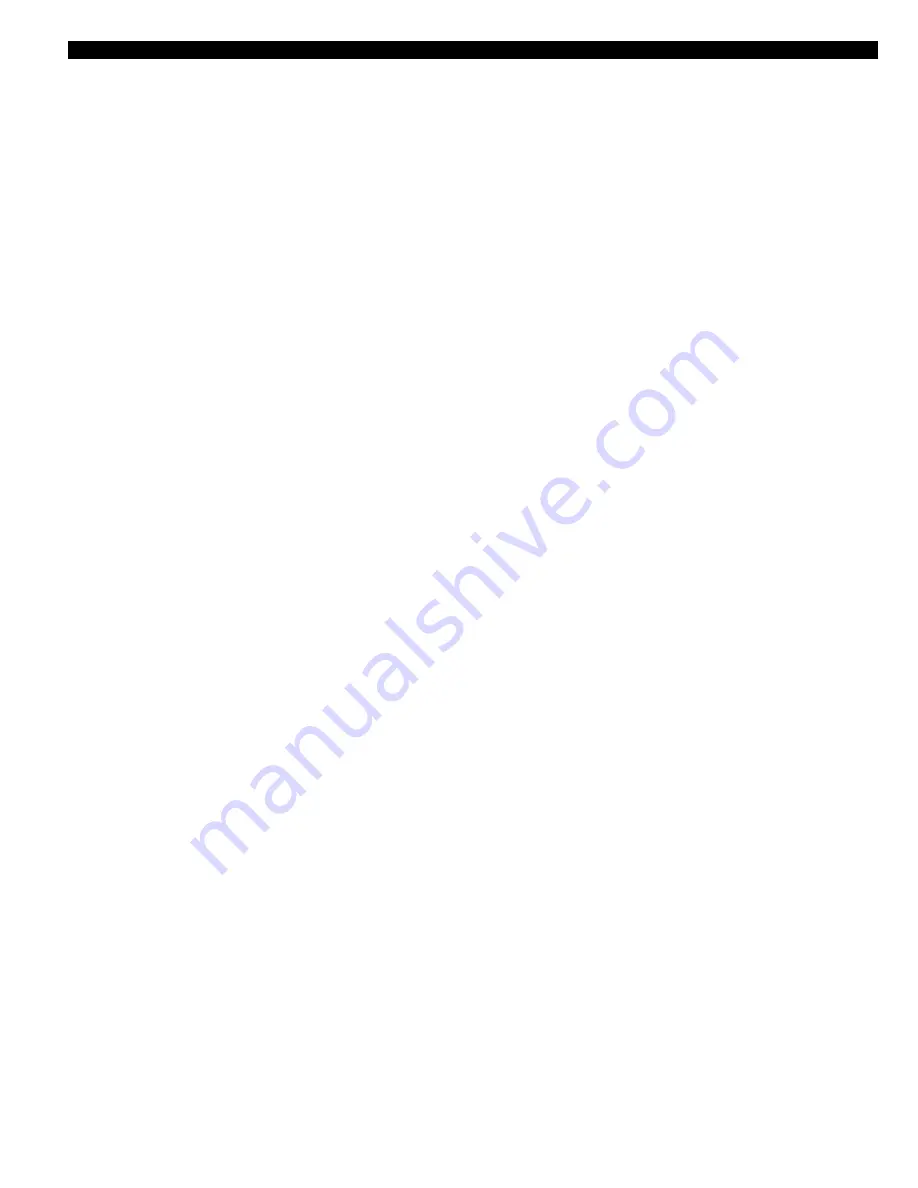
5
Introduction and General Information
The Q-Matic nut plate drill motor has been developed for
drilling an countersinking the two holes required for attach-
ment of nut plate fasteners.
Utilizing an air/hydraulic system, and expanding collet grips
the work with 240 lbs. holding force during the complete drilling
and countersinking operation.
The air powered motor develops 1HP and consumes 35 CFM
at 90 psi, the recommended air line pressure. The tool developes
200 lbs. of drilling thrust, and is capable of drilling holes up to
.128 in. diameter in aluminum. Total feed stroke is .562 in.;
maximum colleting stroke is .400 in.
Each Q-matic nut plate drill can be used to drill holes for all
three types of nut plate fasteners: single wing, double wing and
Mickey Mouse. By simply changing the front bearing support
block, lift finger and pressure foot, one tool can be used for all
types of nut plate fasteners. This feature eliminates the need
for a specific tool to drill and countersink the varied nut plate
configuration.
Depth Control
Individual spindle adjustment knobs located at the rear of the
tool controls the countersink depth accuracy to or -
.001 in.
Depending upon the hardness of the material being drilled,
drilling cycle time can be adjusted from 1.5 sec. to 34 sec. by
means of an externally mounted feed control valve.
The Q-Matic nut plate drill is available in three speed models:
600 rpm, 6,000 rpm and 20,000 rpm. An adjustable throttle
control valve located in the handle enables the tool spindle
speed to be reduced as much as 50%, allowing the tool rpm to
be matched to the material being drilled, thereby providing
optimum drill bit life.
An optional externally mounted pneumatic booster pump is
available for use on the 600 rpm models. This optional pump
increases both thrust and clamping force of the tool by as much
as two and one-half times.
Tool Start-Up
The Q-Matic nut plate drill motor is shipped from the factory
equipped to the customer's specifications; spindle RPM, nut
plate styles, drill spindle spacing and optional booster pump (if
needed). Collets, mandrels and drills can be supplied for
customers with start-up nut plate drilling applications.
After unpacking, examine the customer specified equipment
on the Q-Matic tool to verify style and size of components.
Attach air line to 1/4" NPT inlet bushing. If 1/4" quick discon-
nect plugs are minimum recommended size for standard units
and 3/8" quick disconnect fittings are minimum recommended
size for units with booster pumps, the recommended air hose
size is 3/8" inside diameter equipped with in-line filter and
lubricator.
With air line attached, pull trigger to start tool and allow tool to
run through a full cycle with drills in fully extended position.
When trigger is released, drills return to original position and
collet extends to open position.
To adjust depth of countersink, turn the spindle adjusting
knobs at the rear of the tool to the appropriate depth. Turning
the knobs counterclockwise reduces depth; clockwise in-
creases depth.
Testing the tool on a separate piece of material will insure that
the tool is operating properly and that the countersink depth
has been accurately set.
Use a conventional drill to drill the pilot hole in the material. The
size of this pilot hole should match the diameter of the collet
and mandrel selected for the tool.
Insert the collet in the pilot hole while holding the pressure foot
firmly against the surface to be drilled, and actuate the trigger.
The collet will retract and clamp the tool firmly against the work
while the two drills will begin feeding into the material. The
drilling cycle is complete when the drills have reached the
maximum pre-set depth. Releasing the trigger will cause the
drills to retract and the collet to release.
The tool is now ready to begin another cycle.
Tool Operation
Optimum performance of the Q-Matic nut plate drill motor
requires a supply of clean, 90 psi air at 35 cfm. Using an in-line
lubricator will provide the proper lubrication for the air motor
and will significantly increase tool life expectancy.
Because O-rings are extensively used to seal systems within
the tool, the elimination of foreign particles and other contami-
nants will reduce the possibility of damage to these parts.
Always inspect O-rings for damage or wear, and replace as
required. The use of silicone O-ring lubricant is strongly
recommended during reasembly. The addition of oil in the air
line will also increase motor and valve life as well as the life of
the O-rings.