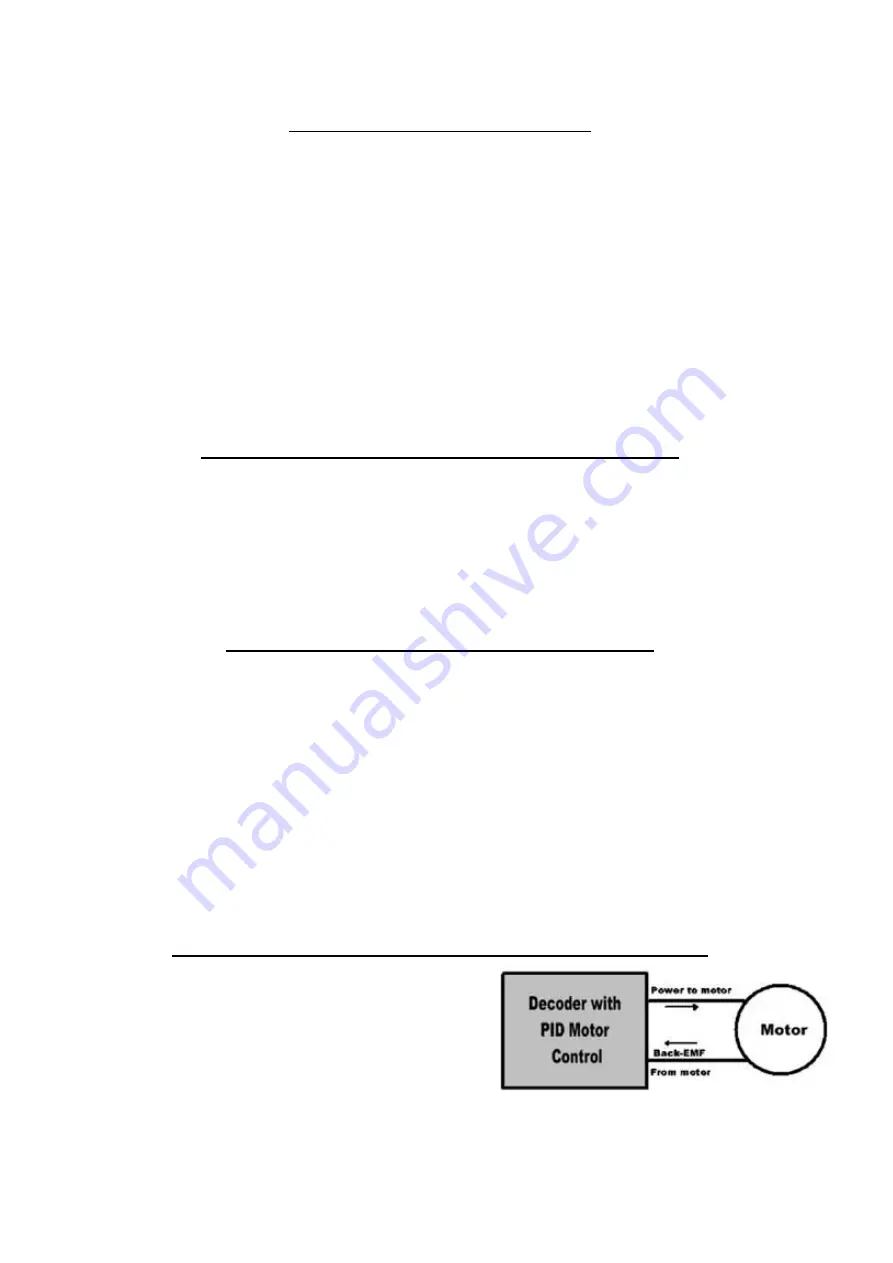
20
5: Fine Tuning Your Performance
The Revolution offers many ways to fine-tune your locomotive for truly revolutionary motor response. This is
accomplished through Regulated
Throttle Control, Back EMF and what are referred to in the DCC industry as PIDs. The
next
section explains what each of these do and how to use them to
really
tune your locomotive for prototypical operation.
Smooth Starts using QSI Decoders.
Some locos tend to jump when they start moving. This can be lessened or eliminated by one of the following:
1)
Make sure the loco is in Regulated Throttle Control (RTC)
2)
Increase the value in CV2 V start. Increase this value by a value of 10 until the loco starts moving
at speed step 1, or 2. If it moves too fast then back it off by 5 until the ideal setting is reached. If CV2
does not fix the problem, increase the value in CV56.5 (RTC Min. BEMF).
3)
If the problem still persists then try increasing the values in the PID Parameters, CV56.18.0 (P Gain)
and CV56.18.2 (D Gain)
Any setting here will also work when the loco is running on DC as well
5a: Back EMF (Back Electro-Motive Force) Explained
One of the better ways to explain BEMF is to compare it to the way an electric motor functions. For example, if you
apply power to a motor, the shaft turns. Conversely, if you turn the motor shaft, the motor will generate power, or in our
case, produce a voltage. Similarly, when a decoder applies power to a motor, it begins to rotate. However, the decoder
applies power in pulses. As a result, there is a time between pulses when no voltage is applied to the motor. During this
time the decoder can “read” the voltage produced by the motor. If the motor slows, the BEMF voltage drops, if speed
increases, the voltage also increases. This is how a BEMF decoder can determine the speed of the motor, sense any
change in motor speed, and respond accordingly to provide realistic load-related variations in speed as trains ascend
and descend grades, for example.
5b: Regulated Throttle Control (RTC) Explained
Regulated Throttle Control (RTC) adds realistic momentum to your train operations. Although it has been available in
analog
from QSI, it has not been available in DCC until now. RTC uses Back EMF to simulate the massive inertial
characteristics of prototype operations. An RTC-controlled locomotive will move through such “obstacles” as tight
turnouts, raised track joints, etc., with little change in speed – and will easily maintain speeds of less than 1 scale mile
per hour! However, if the locomotive encounters a long uphill grade, it will slowly reduce speed just as does the
prototype. Similarly, when a downhill grade is encountered, it will slowly increase in speed like the prototype.
Unlike Speed Control, which is a feature used by many older decoders. RTC is a true, comprehensive throttle control
system, and is controlled by the same CV's that control speed curves, including (CV2, CV3, CV4, CV5, CV23 and
CV24, and all CVs related to the speed curve.
The best news: since RTC-controlled locos slowly adjust their speed based on load, locomotives in consist’s tend to
share power equally. This makes advanced (and truly prototypical) consisting extremely easy since the locomotives can
actually “talk” to each other. Put that helper in the middle of the train, or that pusher at the end – where they belong!
5c: PID (Proportional Integral Derivative) Control Explained
The PID control process is a little like a three ring circus. Each of
its three components play a part in the control process. To
oversimplify, think of PID as a black box with the output as the
power to the motor and the input as the BACK-EMF from the
motor. We “tune” for smoothest operation by changing the CV
values associated with PID parameters. But first, a little more tech.