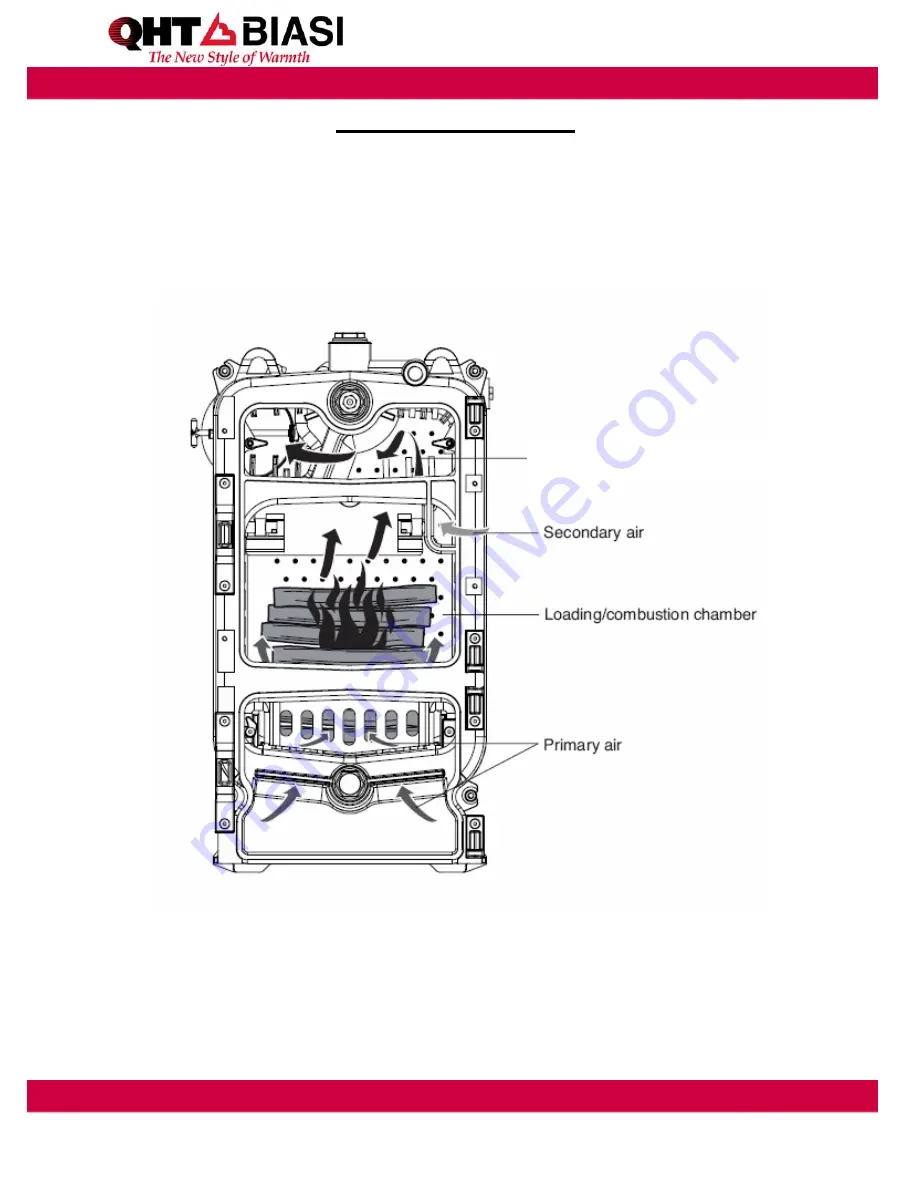
14
The
3WOOD
Boilers are hot water generators that operate by combustion of hard wood or soft coal.
They feature a high quality and extremely thick ASME class 20 cast-iron body, protected by high-density
insulation that limits
heat loss.
The large heat exchange surface and the fins in the flue gas path ensure exceptional resistance to
corrosion and very high
efficiency that remains constant over time (self-cleaning effect).
The combustion chamber and the upper door for loading the wood are sufficiently large to maximize the
burn time
and limit the number of times the door needs to be opened for refueling.
The front air grille for secondary air in the upper door and the flue gas damper are easily adjusted for
tending the fire.
Technology with 3 Pass:
1
st
Pass
The combustion chamber gasses are carried by a special passage in the rear element. In the same area,
very hot secondary air is combined with combustion gases which enhance their oxidation.
2
nd
Pass
The gases from the rear element are reburned in the secondary combustion chamber,
3
rd
Pass
The third Pass consists of a wide-finned, self-cleaning zone which directs the smoke towards the flue
attachment with adjustment shutter and door cleaning.
The 3WOOD Design
Secondary combustion chamber