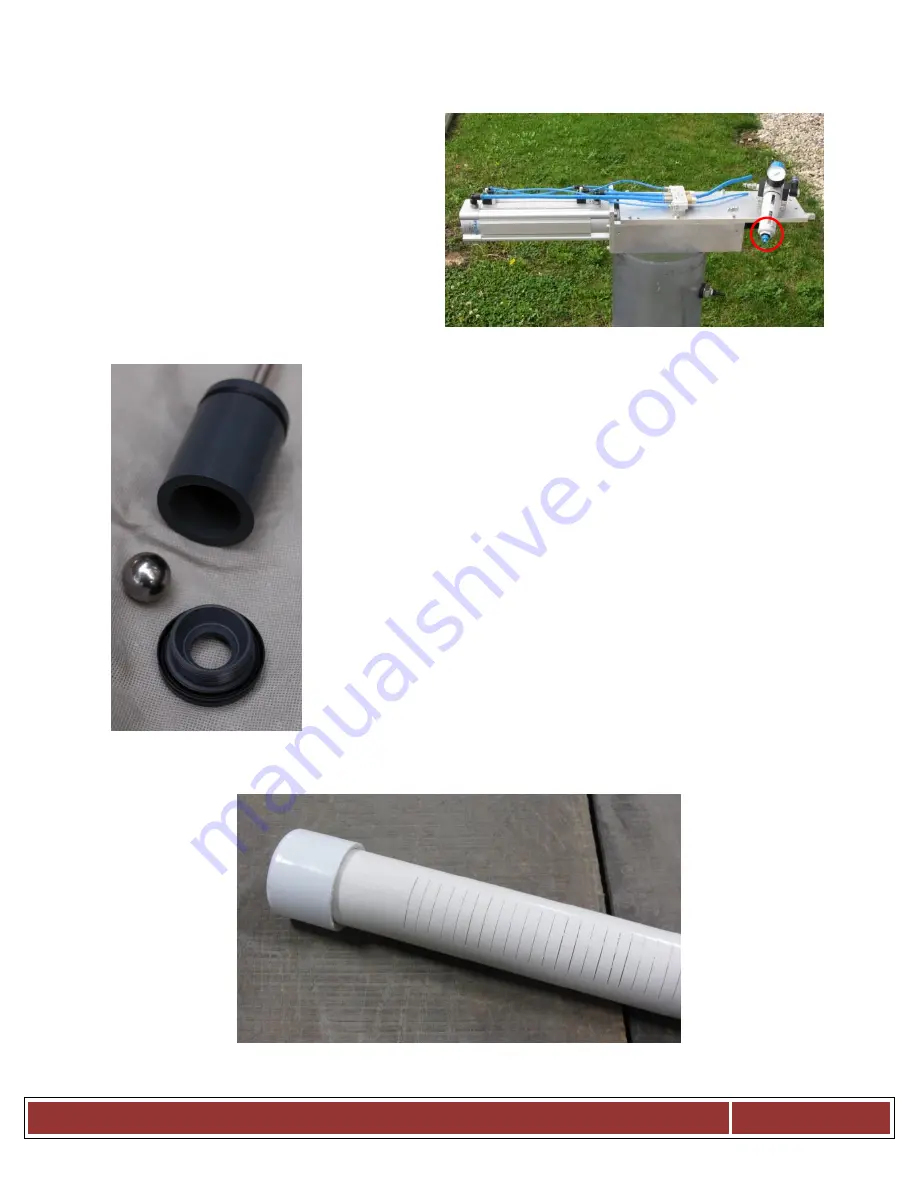
Page 6
PNEUMATIC BACKPLATE ASSEMBLY
The operational lifespan of the pneumatic
backplate assembly depends greatly on the
dryness and cleanliness of the air supply. Drain
water from the filter/regulator housing
regularly by loosening then retightening the
blue vent screw circled at right.
In the event of difficulty with the pneumatic
assembly function, refer to the troubleshooting
steps in Section III.
LOWER PUMP ASSEMBLY
The lower pump assembly includes the PVC Piston and 2 x 316 series
stainless steel balls, which may experience wear over time, especially with
highly abrasive content in the leachate. The PVC piston and one ball are
shown at left.
One of the best methods to reduce wear on the lower pump assembly
and seals is through the use of our optional Intake Screen Filter, shown
below. This simple slotted PVC pipe extends from the lower seat of the
pump and provides an initial filtration of larger particles so as to reduce
the abrasive elements entering the pump.
Should there be high temperatures (>130 degrees F), or a high percentage
of abrasive content in the leachate, such as sand or silica, we recommend
the use of our upgraded high temperature version of our piston,
Part # LP-150-11.
Portion of Intake Screen Filter, typically 24 inches in length