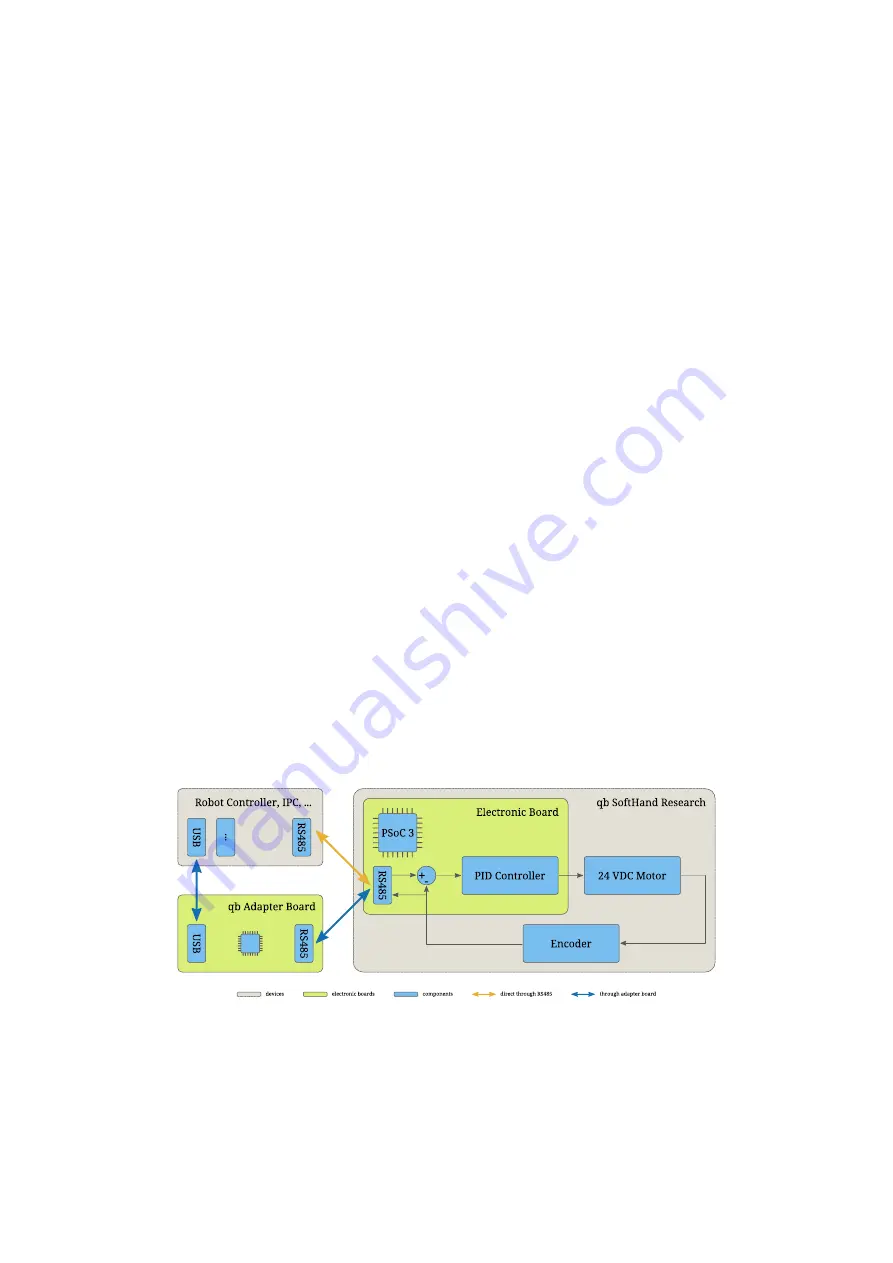
12
—
DESCRIPTION
RELEASE 1.0.1 — 15 JULY, 2020
4 Description
4.1 General
qb SoftHand Research is an anthropomorphic robotic hand based on soft-robotics technology. It is
flexible, adaptable and able to interact with the surrounding environment, objects, or even humans while
limiting the risk of injuring operators, spoiling products, or damaging the robot itself.
Thanks to its soft nature the SoftHand by qbrobotics exploits the principles of synergies in an intrinsically
intelligent design that is not only safe w.r.t. unexpected human-robot interaction, but also adaptable to
grasp different shaped objects without any change in the control action
—
i.e. showing an unparalleled
level of simplicity and flexibility.
The combination of these innovations results in a flexible prehensile device that can grasp a wide variety
of objects. The single-motor actuation makes the hand plug-and-play, simple to control (one single motor
requires one single control signal to either close or open the whole hand), and affordable.
The custom-made electronic board inside the qb SoftHand Research is composed of a logic stage for
communication and low-level computation, and a power stage for motion control. This, together with a
DC motor and its absolute encoder, establishes a simple position and current control feedback regulated
by a properly tuned PID controller.
The intelligence is delegated to a Cypress PSoC 3 microcontroller
—
i.e. a programmable embedded
system-on-chip
—
which runs a custom firmware provided by
qbrobotics that
enables an RS485 serial
communication channel.
If the robot controller or the IPC used does not support direct RS485 communication, it is possible to add a
qb Adapter Board (generally referred as
qbdummy
) which acts as a transparent converter from µ-USB to
the RS485 differential line. In such a case the qb Adapter Board must be connected to a 24 VDC PSU.
The qb SoftHand is generally shipped with a qb Adapter Board equipped with a 3 meter-length cable.
Figure 6. —
qb SoftHand hardware simplified scheme
The qb SoftHand Research does not use Common Industrial Protocols (CIP) or other industrial standards
for I/O communication due to historical design and technical reasons.
I/O data basically refers as measurements from the device, commands to the device, and parameters
from/to the device. These are handled in a custom package format as follows