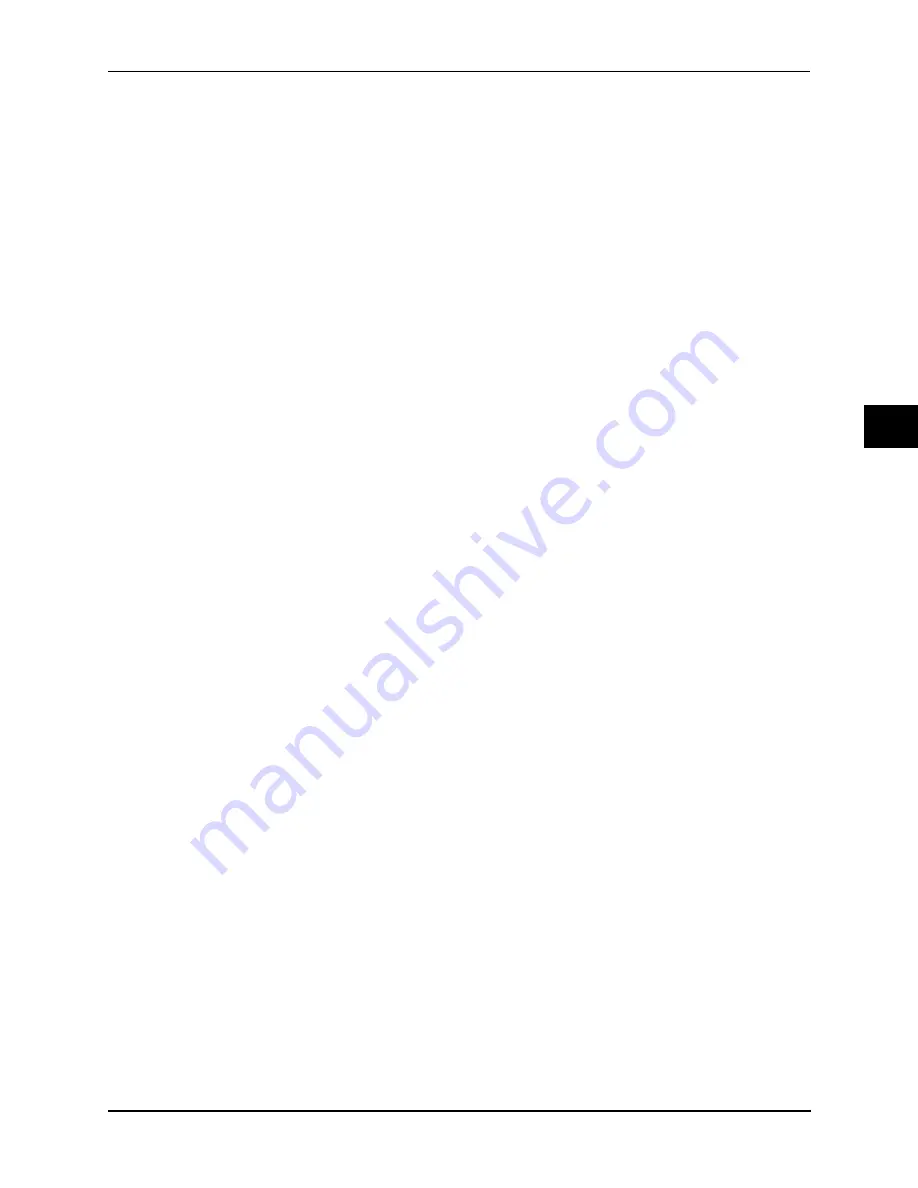
Chapter 6 Maintenance
June 2001
Page 6–3
6
4. Further isolation of faults includes:
• Voltage readings
• Resistance readings
• Signal injection
• Re-alignment
• Sensitivity measurements
• Gain measurements
5. Replace suspected faulty components.
6. Check-out and adjust affected circuits.
6.5.3
Servicing Components
Soldered Directly to Terminals
1. Avoid overheating from soldering by using a
low-wattage soldering iron (60 watt
maximum).
2. Make sure there is no current leakage from the
soldering iron.
You may use an isolation transformer to
prevent current leakage.
3. When soldering leads from transistors or
diodes, use heat sinks, e.g., alligator clips.
4. You can remove molten solder from the board
with a solder-sucker.
5. When removing a multi-lead component from
a printed circuit board, first cut all leads and
then remove the leads individually (to prevent
overheating). If there are only a few leads,
you can use a broad-tip soldering iron.
6.5.4
Servicing Components
Mounted Directly on Heat
Sinks
1. Remove the heat sink and bracket from the
chassis by loosening the securing devices.
2. Remove the transistor, diode, or other device
from the heat sink.
3. When replacing the transistor, diode, or other
device, make certain that the device and the
heat sink make secure contact for good heat
dissipation. Mount a device first on the heat
sink, and then on the board. Also, make sure
that you replace all insulators, washers, spring
washers and other mounting hardware as you
originally found them.
We recommend a very light coating of DC-4
(Dow-Corning 4 Compound Silicon Lubri-
cant) for transistors and diodes that are
mounted on heat sinks. This heat sink
compound promotes efficient dissipation of
heat through the heat sink.
6.5.5
Servicing Metal Oxide
Semiconductor (MOS) Devices
MOS devices may be vulnerable to static changes.
Be sure to observe the special precautions
described below both before and during assembly.
Precautions to take before assembly:
• Avoid wearing silk or nylon clothing, as
this contributes to static buildup.
• Avoid carpeted areas and dry environ-
ments.
• Discharge body static by placing both
hands on a metal, earth-grounded surface.
Precautions to take during assembly to avoid the
possibility of electrostatic discharge:
• Wear a ground strap during assembly
• Avoid touching electrically-conductive
circuit parts by hand
• When removing a module from the chassis,
always place it on a conductive surface
which is grounded through a resistance of
approximately 100 K
Ω
.
• Make sure that all electrically-powered test
equipment is properly grounded.
Summary of Contents for LPA100
Page 2: ...Copyright 2001 Pulsar Technologies Inc...
Page 10: ...Technologies Inc...
Page 50: ...Figure 7 2 LPA50 LPA100 Power Supply Component Location 1617C38...
Page 52: ...Figure 7 3 LPA50 LPA100 Power Supply Schematic 1617C39...
Page 55: ...Figure 8 2 LPA50 LPA100 12 5W PA PC Board 1495B73 8...
Page 56: ...Figure 8 3 12 5W PA Schematic 1606C33...
Page 65: ......
Page 66: ...Technologies Inc...