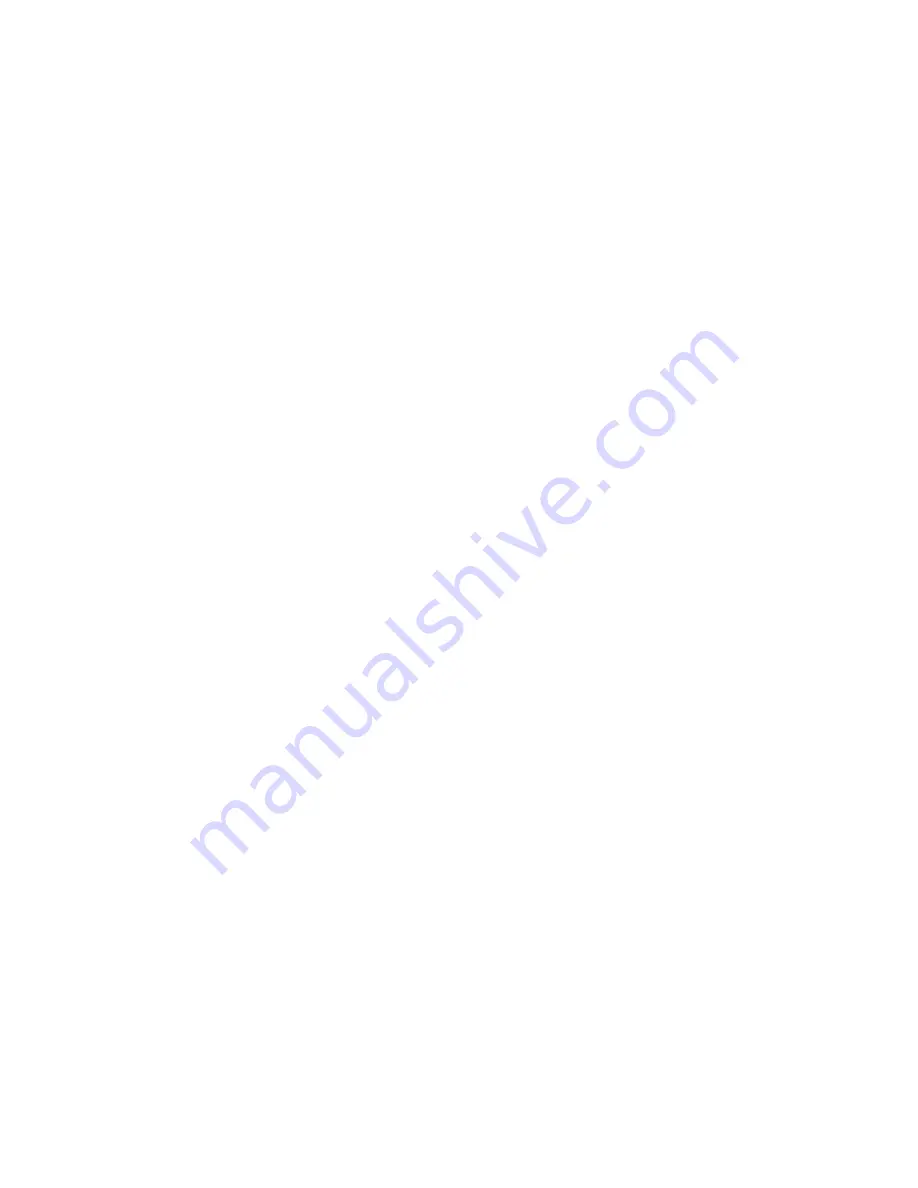
11
d. Repeat steps b and c until 4-20 mA is output from the circuit when 0%
and 100% is dialed in and/or meter reads minimum and maximum.
5.5 Ratio Control
Due to highly tolerance components, no adjustment is necessary.
5.6 Pneumatic Input
See figure 5
a. With the override toggle switch in the “man” position, wire the actuator per
the supplied wiring diagram.
b. Connect the negative lead of a voltmeter to TB1-1. This point is a circuit
board common.
c. Locate the positive lead of a voltmeter to J6 of the option board.
d. Input a 3 psi signal into the ¼” NPT port and adjust the zero adjust until a
1 volt reading is obtained.
e. Input a 15 psi input and adjust the span adjust on the option board until a
5 volt reading is obtained.
f. Repeat steps d and e until a 1-5 volt reading is obtained.
g. Remove the pneumatic signal from the board and place the override
toggle switch in the “remote” position.
h. Located the positive lead of the voltmeter to the wiper terminal (black
lead) of the feedback potentiometer.
i. With the micrometer hand knob at the 0% stroke setting adjust the “low
Cal” trim potentiometer until a 1 volt reading is obtained.
j. Turn the knob to the 100% setting and adjust the “High Cal” trim
potentiometer until a 5 volt reading is obtained.
k. Repeat steps I and j until the voltages from the feedback wiper stabilize at
1 and 5 volts.
l. Reconnect the pneumatic signal and place the override toggle switch to
auto. Verify pr4oper operation. If the actuator fails to fully adjust to either
endpoint and does not switch off then readjust the “Low” or “High Cal”
trim potentiometer depending on which endpoint is off, until proper
adjustment is achieved.
5.7 Protection Circuitry
The signal protection circuitry determines how the actuator responds in the event of
a loss of signal or over signal condition. Once the unit has been calibrated to a
specific input signal it recognizes any signal which is less than the calibrated low end
signal as a loss of signal and any signal greater than the calibrated high end signal
as an over signal. Responses are determined by the setting of the 3 position DIP
Summary of Contents for ELMA NEMA 4X
Page 15: ...13 ...
Page 22: ...20 7 1 NEMA Type 4X Cross Section ...
Page 23: ...21 7 2 NEMA Type 4X Exploded Isometric ...
Page 24: ...22 7 3 NEMA Type 7 Cross Section ...
Page 25: ...23 7 4 NEMA Type 7 Exploded Isometric ...
Page 26: ...24 ...