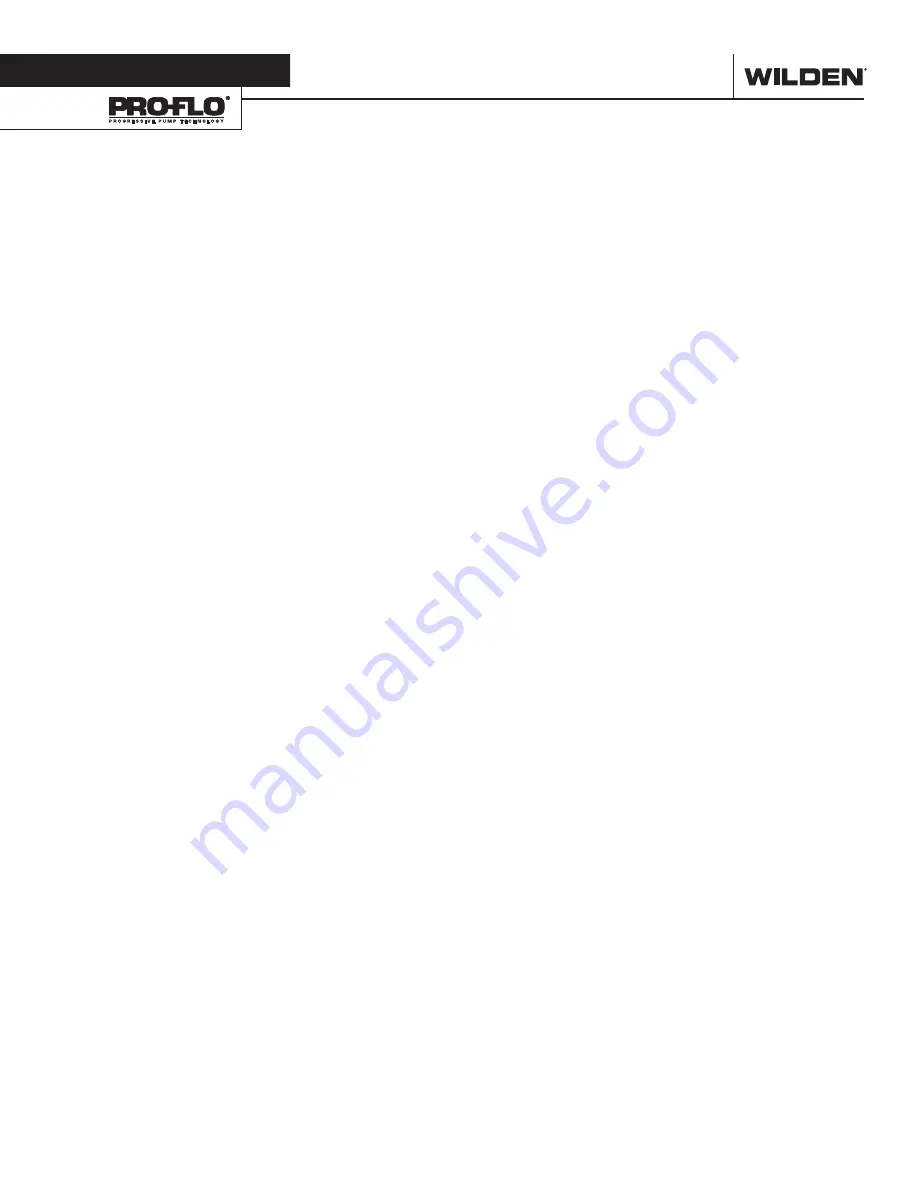
WIL-11160-E-09
7
WILDEN PUMP & ENGINEERING, LLC
The P1500 plastic pump has a 76 mm (3") inlet and 76
mm (3") outlet and is designed for flows to 784 lpm (207
gpm) . The P1500 plastic pump is manufactured with wetted
parts of polypropylene and PVDF . The center block of the
P1500 plastic pump is constructed of polypropylene . PTFE
diaphragms, valve balls, and o-rings are employed to satisfy
chemical compatibility concerns .
The suction pipe size should be at least 76 mm (3") diameter
or larger if highly viscous material is being pumped . The
suction hose must be non-collapsible, reinforced type as
the P1500 is capable of pulling a high vacuum . Discharge
piping should be at least 76 mm (3"); larger diameter can
be used to reduce friction losses . It is critical that all fittings
and connections are airtight or a reduction or loss of pump
suction capability will result .
For P1500 plastic models, Wilden offers 150 lb . standard
flanges (ANSI or DIN) . The following details should be noted
when mating these to pipe works:
• A 60–80 shore gasket that covers the entire flange face
should be used .
• The gasket should be between 0 .075" and 0 .175" thick-
ness .
A non-raised surfaced-flange adapter should be utilized
when mating to the pump’s inlet and discharge manifolds
for proper sealing .
INSTALLATION: Months of careful planning, study, and
selection efforts can result in unsatisfactory pump perfor-
mance if installation details are left to chance .
Premature failure and long term dissatisfaction can be
avoided if reasonable care is exercised throughout the
installation process .
LOCATION: Noise, safety, and other logistical factors usually
dictate that “utility” equipment be situated away from the
production floor . Multiple installations with conflicting
requirements can result in congestion of utility areas, leav-
ing few choices for siting of additional pumps .
Within the framework of these and other existing conditions,
every pump should be located in such a way that five key
factors are balanced against each other to maximum advan-
tage .
ACCESS: First of all, the location should be accessible . If it’s
easy to reach the pump, maintenance personnel will have
an easier time carrying out routine inspections and adjust-
ments . Should major repairs become necessary, ease of
access can play a key role in speeding the repair process
and reducing total downtime .
AIR SUPPLY: Every pump location should have an air line
large enough to supply the volume of air necessary to
achieve the desired pumping rate (see Section 5) .
For best results, the pumps should use a 5µ (micron) air
filter, needle valve and regulator . The use of an air filter
before the pump will insure that the majority of any pipeline
contaminants will be eliminated .
SOLENOID OPERATION: When operation is controlled by a
solenoid valve in the air line, three-way valves should be
used, thus allowing trapped air to bleed off and improving
pump performance . Pumping volume can be set by count-
ing the number of strokes per minute and multiplying by
displacement per stroke .
MUFFLER: Sound levels are reduced below OSHA specifi-
cations using the standard Wilden muffler . Other mufflers
can be used to further reduce sound levels, but they may
reduce pump performance .
ELEVATION: Selecting a site that is well within the pump’s
dynamic lift capability will assure that loss-of-prime troubles
will be eliminated . In addition, pump efficiency can be
adversely affected if proper attention is not given to eleva-
tion (see Section 5) .
PIPING: Final determination of the pump site should not be
made until the piping problems of each possible location have
been evaluated . The impact of current and future installations
should be considered ahead of time to make sure that inad-
vertent restrictions are not created for any remaining sites .
The best choice possible will be a site involving the short-
est and the straightest hook-up of suction and discharge
piping . Unnecessary elbows, bends, and fittings should be
avoided . Pipe sizes should be selected so as to keep friction
losses within practical limits . All piping should be supported
independently of the pump . In addition, the piping should be
aligned so as to avoid placing stresses on the pump fittings .
Expansion joints can be installed to aid in absorbing the
forces created by the natural reciprocating action of the
pump . If the pump is to be bolted down to a solid foun-
dation, a mounting pad placed between the pump and
foundation will assist in minimizing pump vibration . Flex-
ible connections between the pump and rigid piping will
also assist in minimizing pump vibration . If quick-closing
valves are installed at any point in the discharge system,
or if pulsation within a system becomes a problem, a surge
suppressor should be installed to protect the pump, piping
and gauges from surges and water hammer .
When pumps are installed in applications involving flooded
suction or suction head pressures, a gate valve should be
installed in the suction line to permit closing of the line for
pump service .
NOTE: The elbows and tees have bosses that are designed
to be tapped with a 9 .5 mm (3/8") fitting for draining the
pump during maintenance .
If the pump is to be used in a self-priming application, be
sure that all connections are airtight and that suction lift is
within the pump’s ability .
Pumps in service with a positive suction head are most
efficient when inlet pressure is limited to 0 .5–0 .7 bar (7–10
psig) . Premature diaphragm failure may occur if positive
suction is 0 .8 bar (11 psig) and higher .
THE MODEL P1500 WILL PASS 13 mm (1/2") SOLIDS .
WHENEVER THE POSSIBILITY EXISTS THAT LARGER SOLID
OBJECTS MAY BE SUCKED INTO THE PUMP, A STRAINER
SHOULD BE USED ON THE SUCTION LINE .
CAUTION: DO NOT EXCEED 6.9 BAR (100 PSIG) AIR SUPPLY
PRESSURE ON P1500 POLYPROPYLENE PUMPS.
CAUTION: DO NOT EXCEED 8.6 BAR (125 PSIG) AIR SUPPLY
PRESSURE ON PVDF PUMPS.
PUMPS SHOULD BE THOROUGHLY FLUSHED WITH WATER
BEFORE INSTALLING INTO PROCESS LINES.
BLOW OUT AIR LINE FOR 10 TO 20 SECONDS BEFORE
ATTACHING TO PUMP TO MAKE SURE ALL PIPE LINE
DEBRIS IS CLEAR. ALWAYS USE AN IN-LINE AIR FILTER.
S e c t i o n 6
S U G G E S T E D I N S T A L L A T I O N