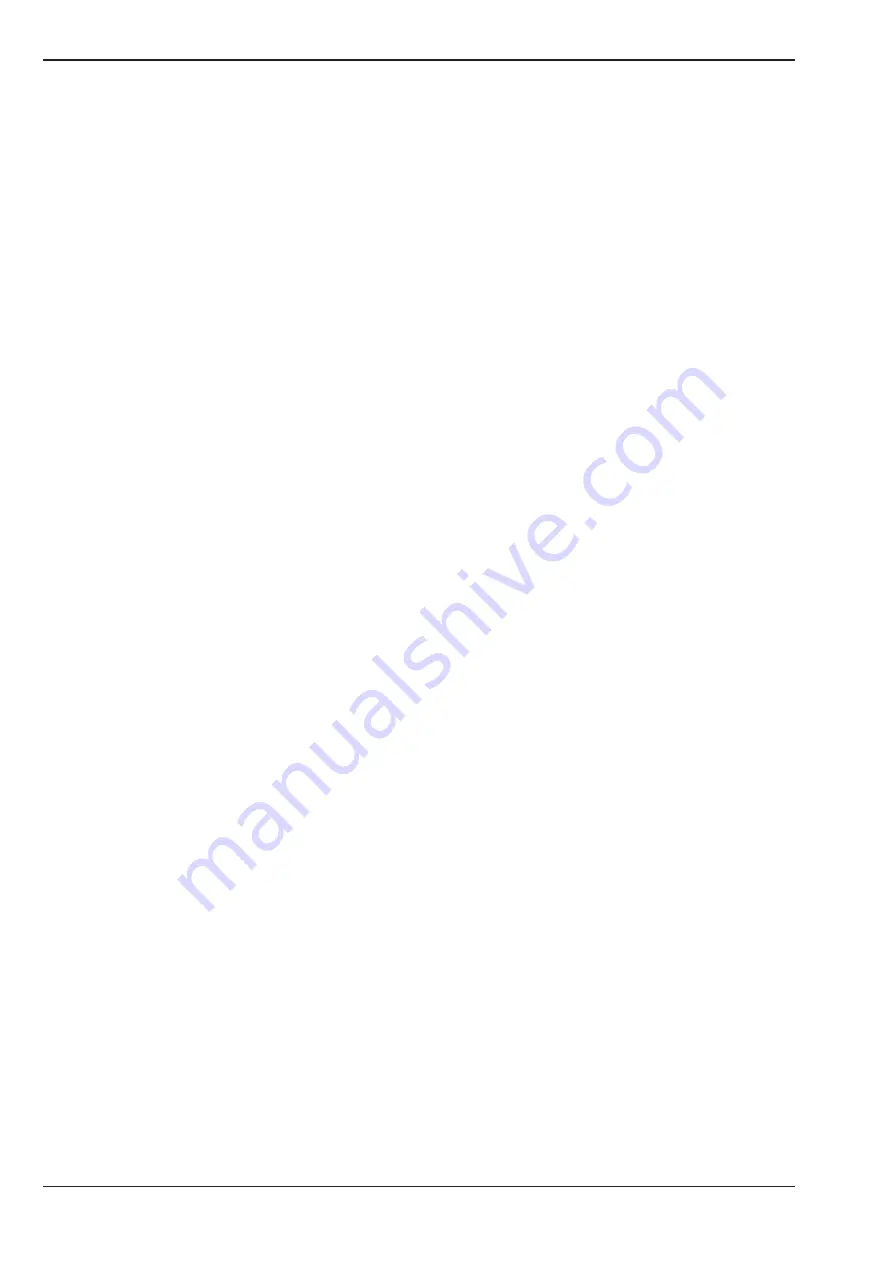
Section 6
Maintenance
6.10
PRONAR T701HP
• Install the brake cylinder fork pin
and washers and secure the pin with
cotter pins.
• Rotate adjustment bolt (4) to the right
until one or two clicking sounds are
heard in the expander arm regulating
mechanism.
• Repeat adjustment activities for the
other brake cylinder on the same
axle.
• Engage the brake.
• Remove previous marks and measure
the brake cylinder piston rod stroke
again.
• If the brake cylinder piston rod stroke
is outside the proper operating range,
repeat the adjustment.
cHEcKiNg THE BRAKE OPERATiON
• After completed adjustment, perform
a trial run.
• Engage the brake several times. Stop
the tractor with trailer and check the
temperature of brake drums.
• If any of the drums is too hot, correct
the brake adjustment and perform
a trial run again.
j.3.2.589.04.1.EN
Summary of Contents for T701HP
Page 2: ......
Page 3: ...INTRODUCTION ...
Page 11: ......
Page 12: ......
Page 15: ...Basic information Section 1 ...
Page 26: ...Section 1 Basic information 1 12 PRONAR T701HP ...
Page 27: ...Safety advice Section 2 ...
Page 44: ...Section 2 Safety advice 2 18 PRONAR T701HP ...
Page 45: ...Design and operation Section 3 ...
Page 60: ...Section 3 Design and operation 3 16 PRONAR T701HP ...
Page 61: ...CORRECT use Section 4 ...
Page 83: ...Technical inspection schedule Section 5 ...
Page 112: ...Section 5 Technical inspection schedule 5 30 PRONAR T701HD ...
Page 113: ...Maintenance Section 6 ...
Page 129: ...Tyre system Section 7 ...
Page 131: ......
Page 132: ......