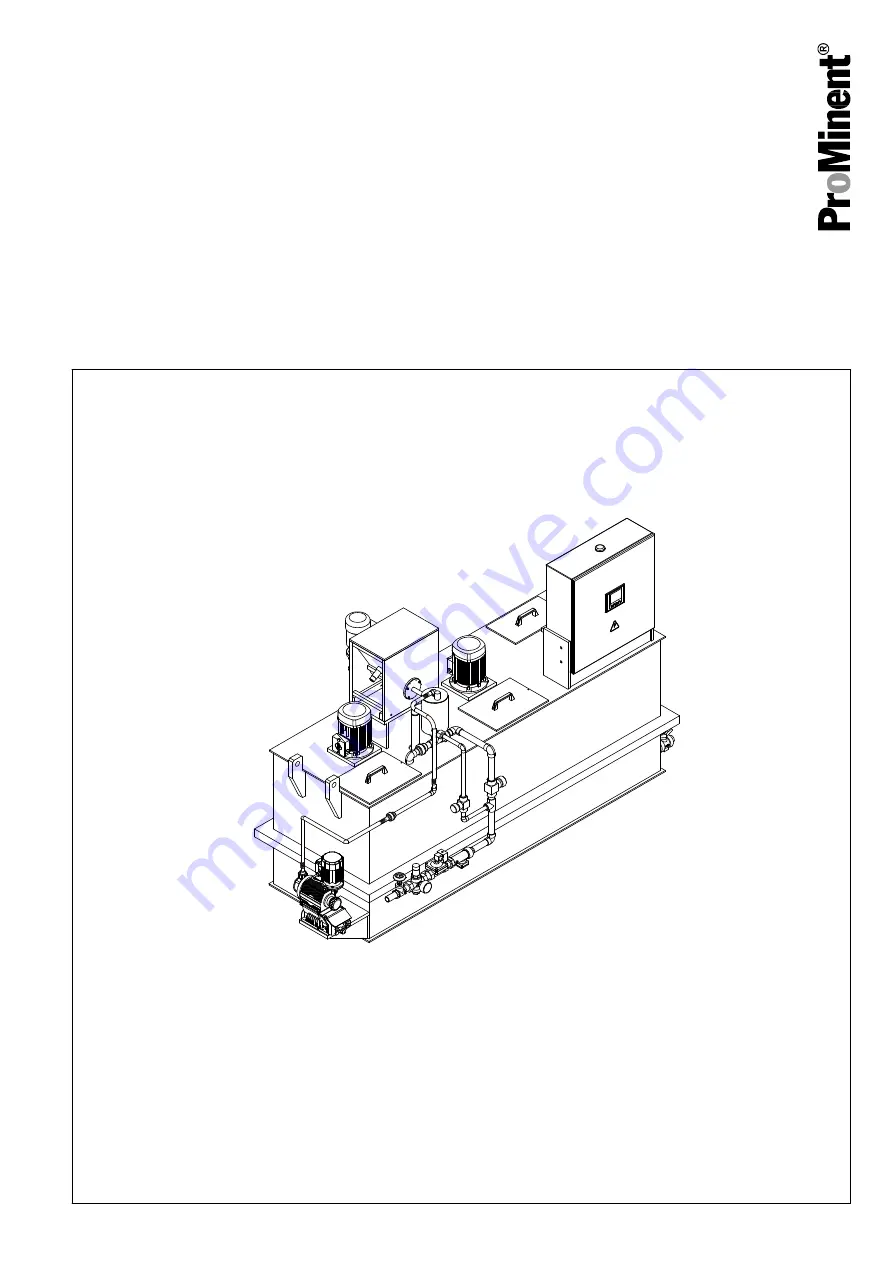
Ultromat
®
ULFa
Continuous Flow System
Assembly and operating instructions
A0777
Original operating instructions (2006/42/EC)
Part no. 985956
BA UL 031 11/13 EN
Please carefully read these operating instructions before use! · Do not discard!
The operator shall be liable for any damage caused by installation or operating errors!
Technical changes reserved.