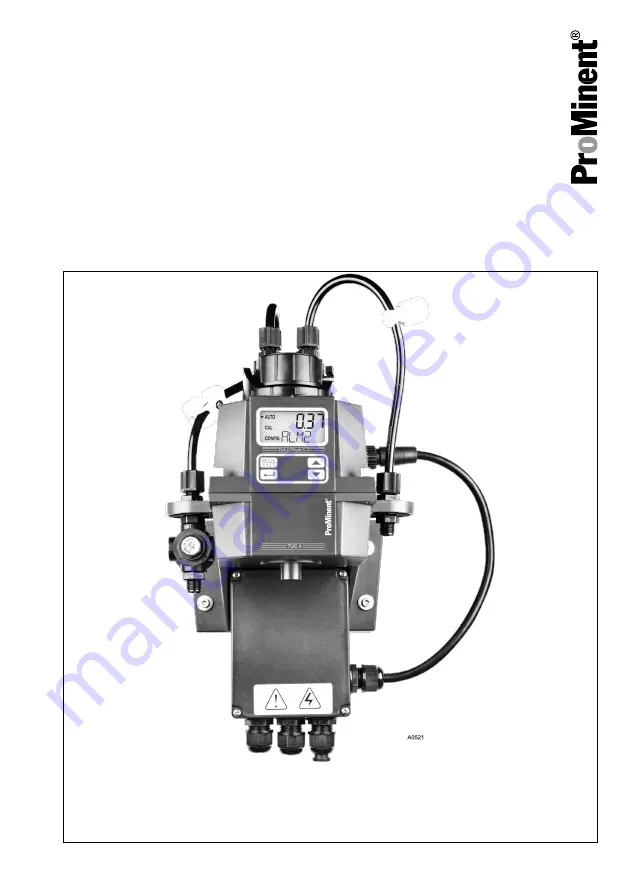
DULCO
®
turb C Measuring Device for Tur‐
bidity
Types: TUC 1, TUC 2, TUC 3, TUC 4
Assembly and operating instructions
EN
Part no. 986062
BA DT 053 08/16 EN
Please carefully read these operating instructions before use. · Do not discard.
The operator shall be liable for any damage caused by installation or operating errors.
The latest version of the operating instructions are available on our homepage.