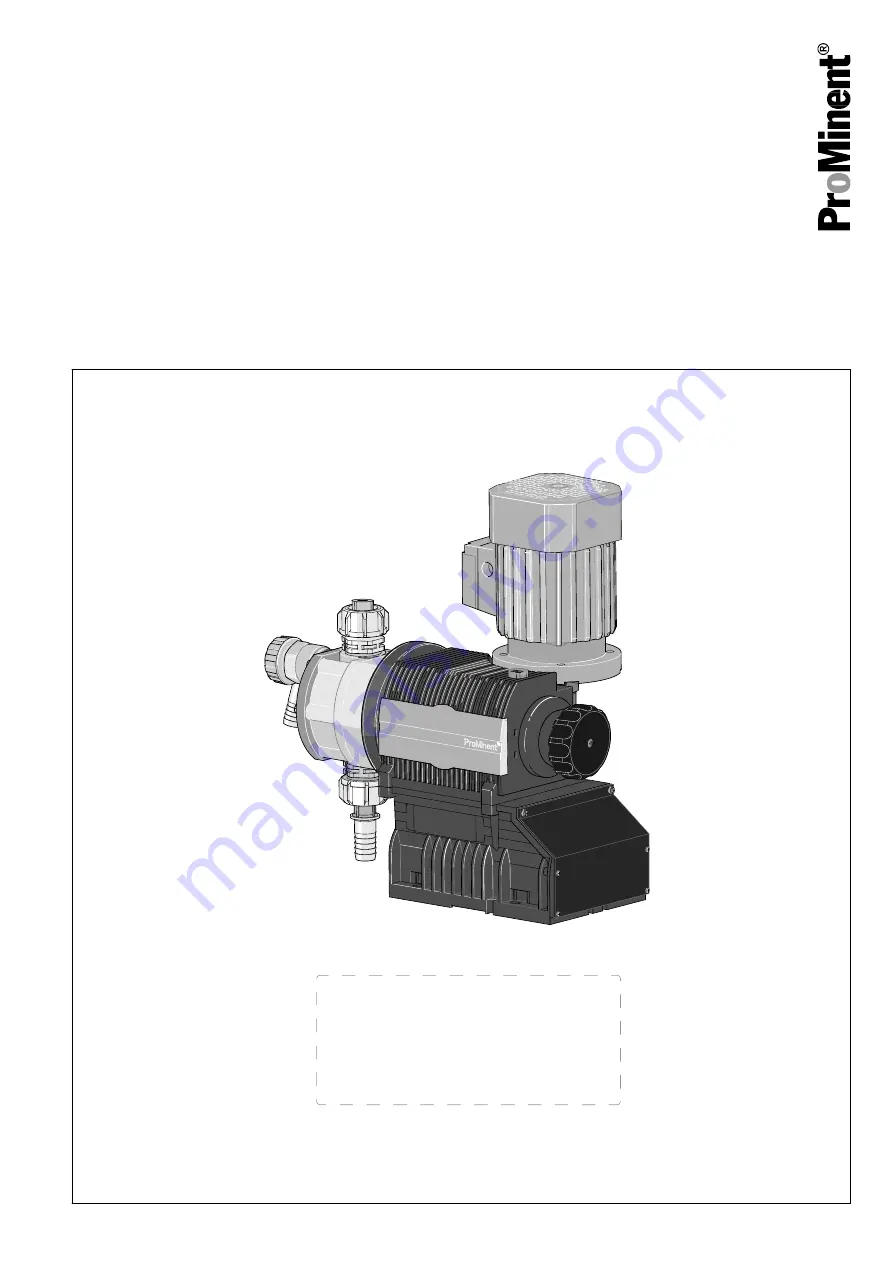
Diaphragm Motor-driven Metering Pump
Sigma/ 1 Basic Type S1Ba
Operating instructions
P_SI_0039
EN
Original Operating Instructions (2006/42/EC)
Part no. 985911
BA SI 075 09/17 EN
Please carefully read these operating instructions before use. · Do not discard.
The operator shall be liable for any damage caused by installation or operating errors.
The latest version of the operating instructions are available on our homepage.