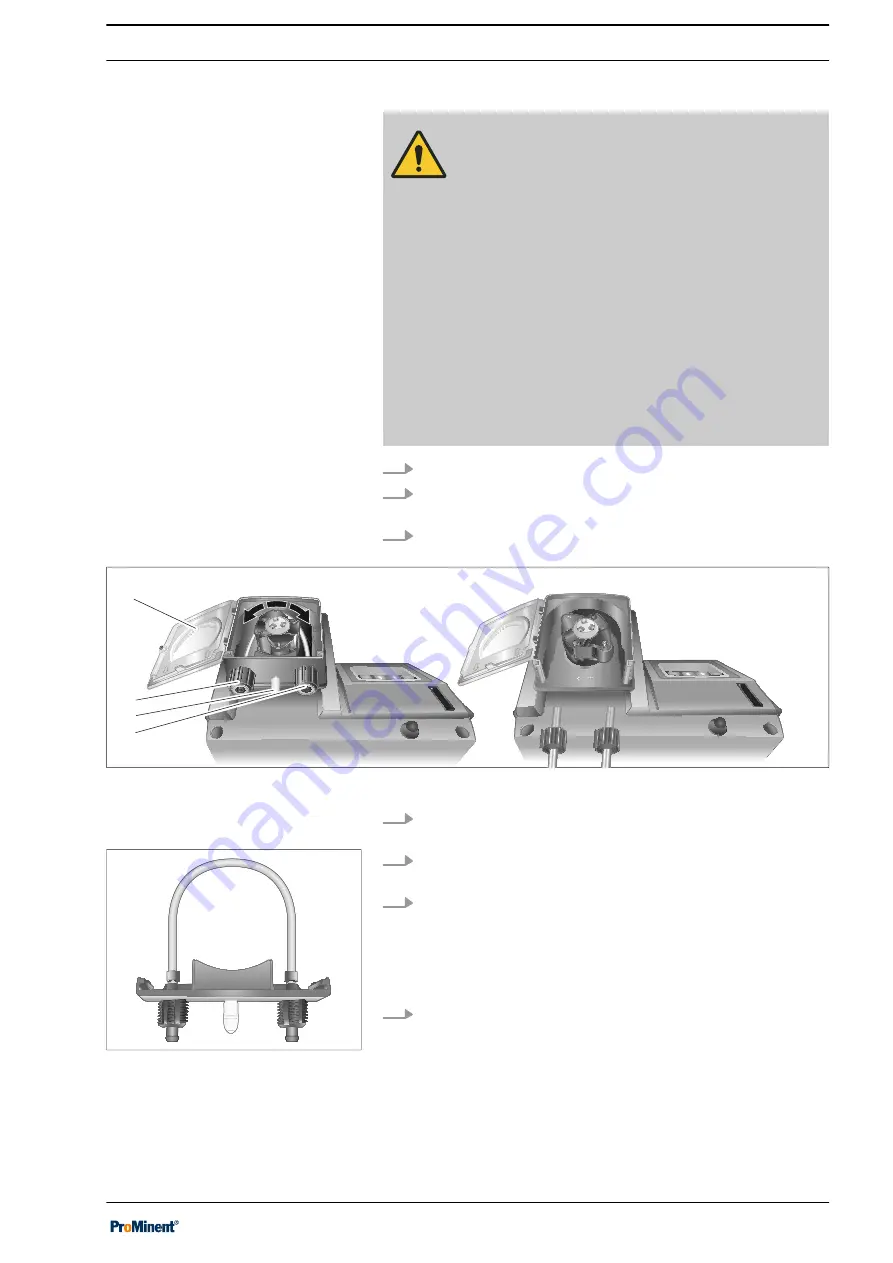
WARNING!
Danger from hazardous substances!
Possible consequence: Fatal or very serious inju‐
ries.
Please ensure when handling hazardous sub‐
stances that you have read the latest safety data
sheets provided by the manufacture of the haz‐
ardous substance. The actions required are
described in the safety data sheet. Check the
safety data sheet regularly and replace, if neces‐
sary, as the hazard potential of a substance can be
re-evaluated at any time based on new findings.
The system operator is responsible for ensuring
that these safety data sheets are available and that
they are kept up to date, as well as for producing
an associated hazard assessment for the worksta‐
tions affected.
1.
Stop metering operation by pressing the Start/Stop key.
2.
Use a suitable flushing medium to flush the pump, referring
to the material safety data sheet for the feed chemical.
3.
Use an on-site depressurisation option to depressurise the
pump.
Pr
o
M
i
nen
t
R
S TOP
S TART
P
Pr
o
M
i
nen
t
R
S TOP
S TART
P
A2564
1
4
3
2
Fig. 21: Replacing the pump hose
4.
Loosen the suction line (3), the discharge line (1) and, if
fitted, the leakage line (2) from the pump connectors.
5.
Loosen the fixing bolt on the transparent cover (4) and
remove the transparent cover.
6.
Pull the hose bearing (= plug-in lower part of the liquid end)
together with the hose forwards out of the liquid end.
Press both
[arrow keys] simultaneously when the rotor is
turning.
ð
The motor supports the rotor.
7.
Slide the new hose bearing with the new pump hose into the
liquid end.
Replacing the pump hose
A2561
Fig. 22: Hose bracket (= plug-in lower
part of the liquid end)
Maintenance
51
Summary of Contents for DULCOflex DF4a
Page 36: ...7 3 1 Operating menu overview Fig 18 Overview of DF4a operating menu Setting 36...
Page 69: ...69...
Page 70: ...70...
Page 71: ...71...