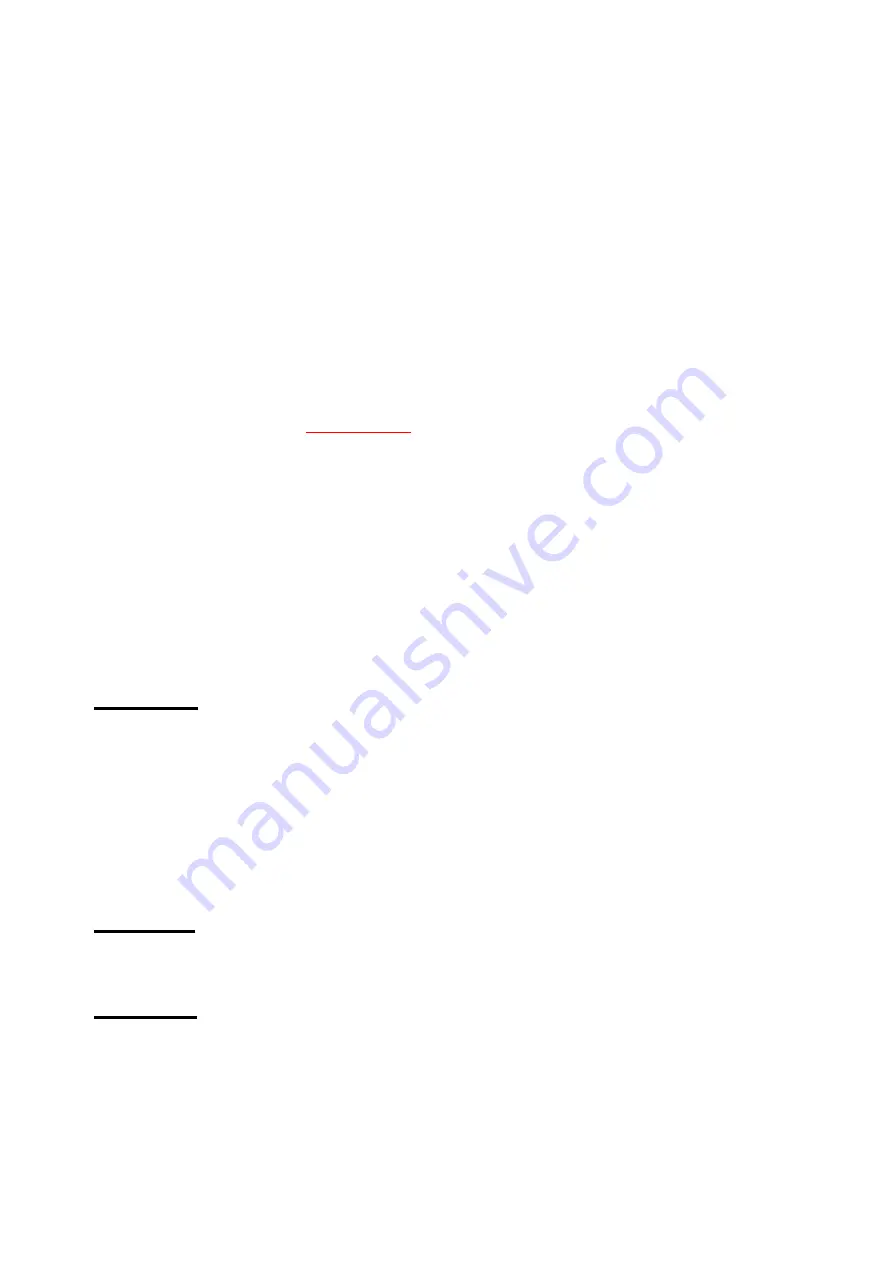
4
2.INSTALLATION
2.1 UNPACKING
•
Carefully
remove
the
cardboard outer shell by cutting the retaining straps then removing
the top and then the side panels.
•
Inspect the machine carefully for any hidden shipping damage. Notify the shipping
company right away if any damage is observed.
•
Remove the machine from the wooden skid. This can be done by two people on the
smaller table top machines. However an approved fork lift will be required for the larger
SC and DC models.
Important note
: Refer to the Moving the Machine Section below.
•
Wipe down the outside of the machine.
2.2 MOVING THE MACHINE
Promax /Promarks chamber style vacuum packaging machines are available in three basic
designs, TC (Table Top), SC (Free Standing Single Chamber) and DC (Double Chamber).
Recommendations for the movement of all three types are listed below.
TC Machines
: Some of the smallest TC units may be lifted off of their wooden skid and moved
manually. However Promax /Promarks recommends that moving even the smallest of their TC
units should not be attempted by one person. The larger TC units should be lifted with the aid of
a fork lift or other approved lifting aid. Prior to lifting with a forklift the forks should be adjusted
to a width that provides the machine with stable support. The proper lifting point for TC machines
is to place the
forks so they come in contact with the units rubber feet located on the bottom of the
machine.
SC Machines
: All SC units should be lifted from their wooden skid and moved to the location
where they will be used with an approved fork lift. Be sure to take note of the points listed below.
DC Machines
: All DC units should be lifted from their wooden skid and moved to the location
where they will be used with an approved fork lift. Be sure to take note of the points listed below.
* Make sure the fork lift forks are properly adjusted for width and use fork extensions if needed.
* Make sure to ascertain the center of gravity and use identified lifting points.
Summary of Contents for Promarks DC-530
Page 19: ...16 ...
Page 23: ...20 5 3 PNEUMATIC DIAGRAM ...
Page 24: ...21 5 4 ELECTRICAL DIAGRAM FB ...
Page 25: ...22 5 3 ELECTRICAL DIAGRAM TB ...
Page 27: ...6 1 BODY 24 DC53100000 Body Diagram ...
Page 29: ...6 2 WORKING BED BOTTOM 26 C C Working bed Bottom Diagram DC53200000 ...
Page 32: ...6 3 1 SEALING BAR BOTTOM FB 29 Cushion Bar Diagram DC532FB000 ...
Page 34: ...6 3 2 SEALING BAR BOTTOM FBG 31 DC532FBG00 Cushion Bar Diagram ...
Page 36: ...6 3 3 SEALING BAR BOTTOM FBPK 33 DC532PK000 Cushion Bar Diagram ...
Page 38: ...6 3 4 SEALING BAR BOTTOM FBPKG 35 DC532PKG00 Cushion Bar Diagram ...
Page 40: ...6 3 5 SEALING BAR BOTTOM FBTB 37 DC532TB000 Sealing Bar Bottom Diagram ...
Page 42: ...6 3 6 SEALING BAR BOTTOM FBTBG 39 DC532TBG000 Sealing Bar Bottom Diagram ...
Page 44: ...6 3 7 SEALING BAR BOTTOM FBTBPK 41 DC532TK000 Sealing Bar Bottom Diagram ...
Page 46: ...6 3 8 SEALING BAR BOTTOM FBTBPKG 43 DC532TKG00 Sealing Bar Bottom Diagram ...
Page 48: ...6 4 CHAMBER LID DIAGRAM 45 Chamber Lid Top Diagram DC53300000 ...
Page 50: ...6 5 1 SEALING BAR TOP FB 47 DC53312A00 Sealing Bar Top Diagram ...
Page 53: ...6 5 2 SEALING BAR TOP PK 50 DC53350A00 Sealing Bar Top Diagram ...
Page 56: ...53 6 6 1 ELECTRICAL BOX FB 6 6 2 ELECTRICAL BOX TB ...