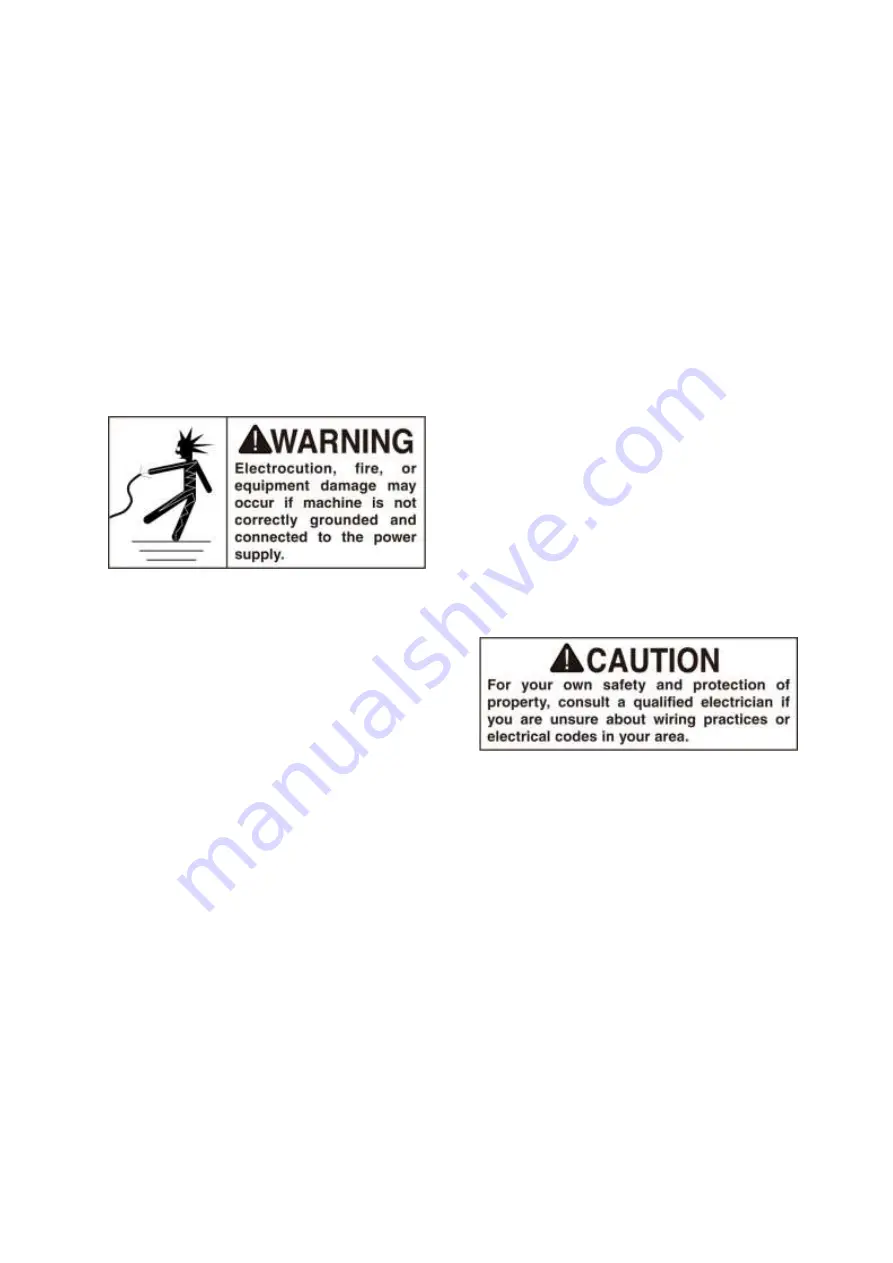
S
ECTION 2: POWER SUPP LY
Availability
Before installing the machine, consider the
availability and proximity of the required
power supply circuit. If an existing circuit
does not meet the requirements for this
machine, a new circuit must be installed.
To minimize the risk of electrocution,
fire, or equipment damage, installation
work and electrical wiring must be done by
a qualified electrician in accordance with
all applicable codes
and standards.
Full-Load Current Rating
The full-load current rating is the amperage
a machine draws at 100% of the rated
output power. On machines with multiple
motors, this is the amperage drawn by the
largest motor or sum of all motors and
electrical devices that might operate at one
time during normal operations.
Full-Load Current Rating at 230V.... 6
Amps
The full-load current is not the
maximum
amount of amps that the machine will draw.
If the machine is overloaded, it will draw
additional amps beyond the full-load rating.
If the machine is overloaded for a sufficient
length of time, damage, overheating, or fire
may result— especially if connected to an
undersized circuit. To reduce the risk of
these hazards, avoid overloading the
machine during operation and make
sure it is connected to a power supply
circuit that meets the requirements in the
following section.
Circuit Requirements
This machine is prewired to operate on a
110V power supply circuit that has a
verified ground and meets the following
requirements:
Voltage..........................................220V/240V
Frequency..............................................50 Hz
Phase...........................................Single-Phase
Power Supply Circuit......................10 Amps
A power supply circuit includes all
electrical equipment between the breaker
box or fuse panel in the building and the
machine. The power supply circuit used for
this machine must be sized to safely handle
the full-load current drawn from the
machine for an extended period of time. (If
this machine is connected to a circuit
protected by fuses, use a time delay fuse
marked D.)
Note:
The circuit requirements listed in this
manual apply to a dedicated circuit—where
only one machine will be running at a time.
If this machine will be connected to a
shared circuit where multiple machines will
be running at the same time, consult a
qualified electrician to ensure that the
circuit is properly sized for safe operation.
8
Summary of Contents for 941VA
Page 3: ...1...