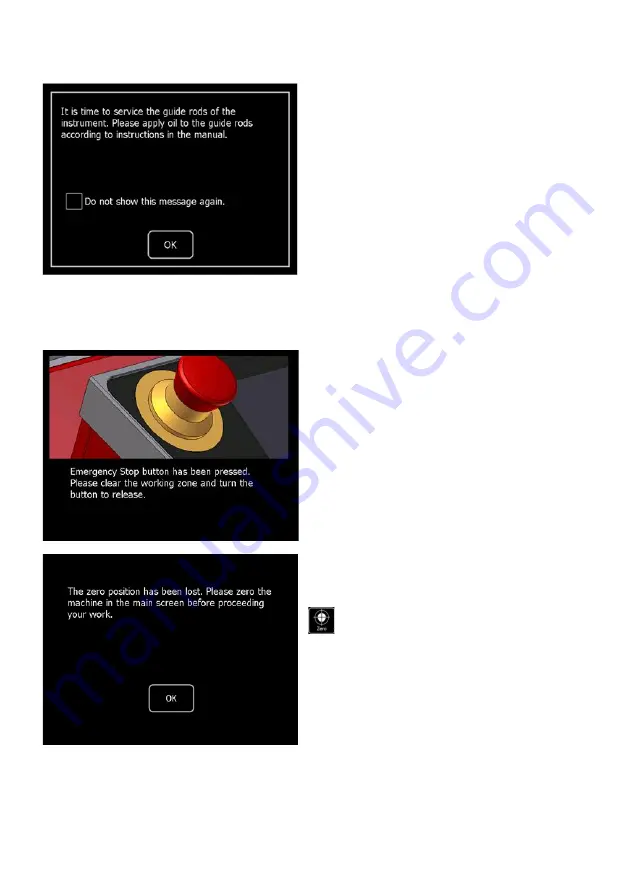
Page 36
7.6.5 Lubrication the guide rods
After a service performance of about
2’000 km a message will appear at
start-up reminding you to lubricate the
guide rods. Carry out the lubrication as
described in chapter 11.3
To switch off the reminder until the next
interval,
choose “Do not show this
message again” and close with “OK”.
7.7 Emergency stop function
Pressing the Emergency Stop button (11) immediately stops the motor. The power
supply of the motor is interrupted so that the tool holder (4) can be moved by hand.
The touch screen and control unit of
the Proceq ZAA 2600 remain active
since only the power supply is
interrupted.
To unlock the Emergency Stop button
(11), turn it counterclockwise.
The following message will be
displayed after unlocking the
Emergency Stop (11):
The Zero position must be reset. Move
the tool holder (4) to the desired
starting position and press the „Zero”
button.