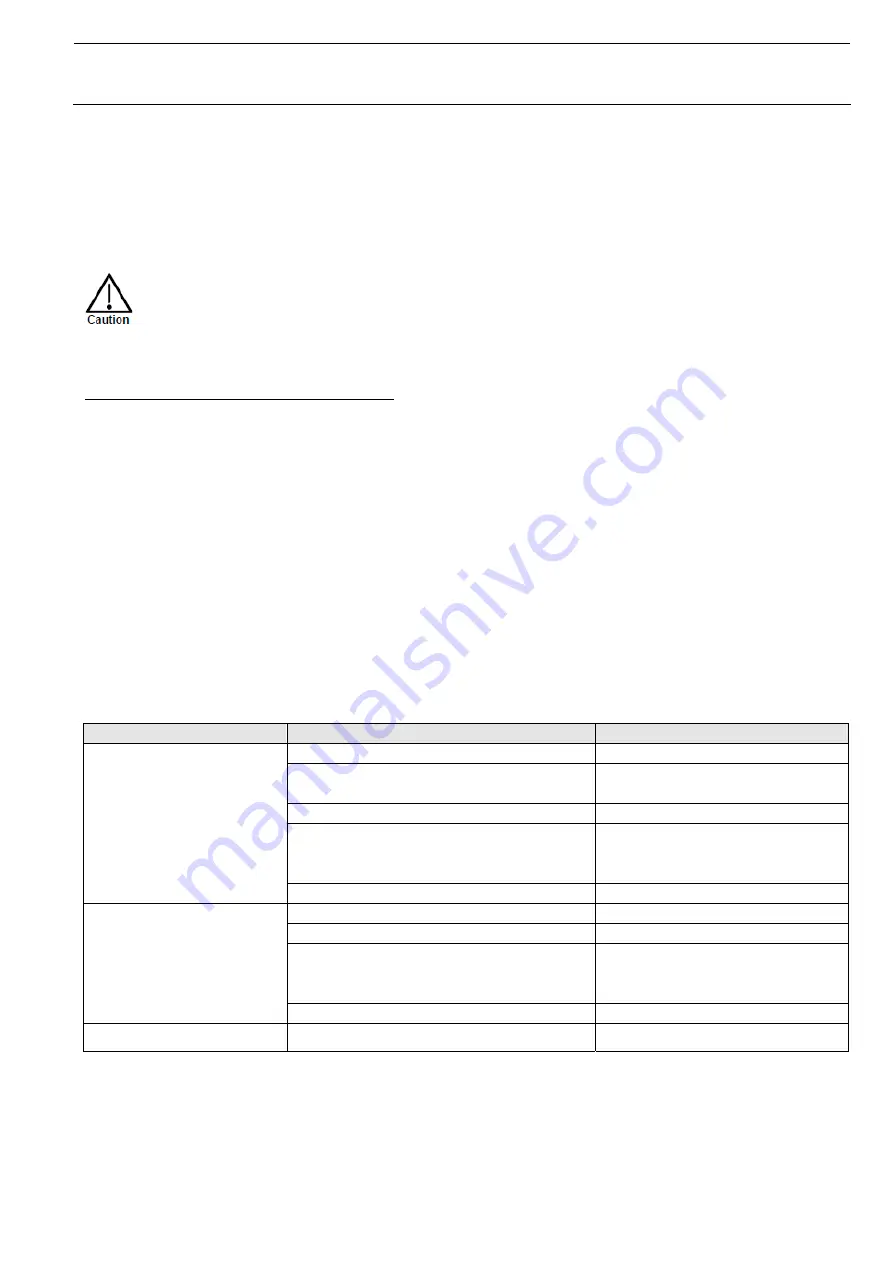
Operating Instructions
Warning Device (audible, battery-operated)
BA 30.12.01.00076
Last updated May 2010 / Index 00
Page 3/3
(42500190)
5.
Maintenance
In order to maintain the device, perform the prescribed function test daily or before starting work.
Remove the batteries from the device if it is to be idle for an extended period.
The vacuum hoses must be checked for leaks and damage on a monthly basis.
The batteries must be replaced if the function test fails or cannot be performed, or if the
alarm generator becomes quieter. Replacing the batteries does not mean that the function
test does not have to be performed.
The replacement interval depends on use conditions and the frequency of alarms.
Note on accident prevention inspections:
It is recommended to replace the batteries of the warning device during the yearly accident prevention inspection
of the entire lifting unit.
Additionally, a complete lifting procedure with simulation of a leakage should be carried out during the yearly
accident prevention inspection.
Replacing the batteries
1. Unscrew the housing cover.
2. Replace the D batteries with new ones of the same type. Observe the polarity.
Do not use lithium-ion or rechargeable batteries.
3. Dispose of batteries in accordance with the existing regulations.
4. Screw the housing cover shut.
5. Perform the function test. The device is now ready for operation.
6.
Troubleshooting
Problem
Cause
Solution
Button was not held long enough
Press button for approx. 1 second
Button is pressed continuously (e.g. jammed,
stuck in place)
Free the button and press it again
Batteries dead
Replace batteries
Battery contacts are corroded or dirty
Clean the battery contacts and the
contact surfaces of the battery
holder
Alarm generator does not
sound when button is pressed
(see function test for
procedure)
Electronics fault
Replace entire warning device
Vacuum hose plugged, kinked or ruptured
Replace hose
Batteries dead
Replace batteries
Battery contacts are corroded or dirty
Clean the battery contacts and the
contact surfaces of the battery
holder
Alarm generator does not
sound on vacuum drop
Electronics fault
Replace entire warning device
Alarm generator is quiet
Battery voltage too low
Replace batteries immediately.
We reserve the right to make technical changes. No responsibility is taken for printing or other types of errors.