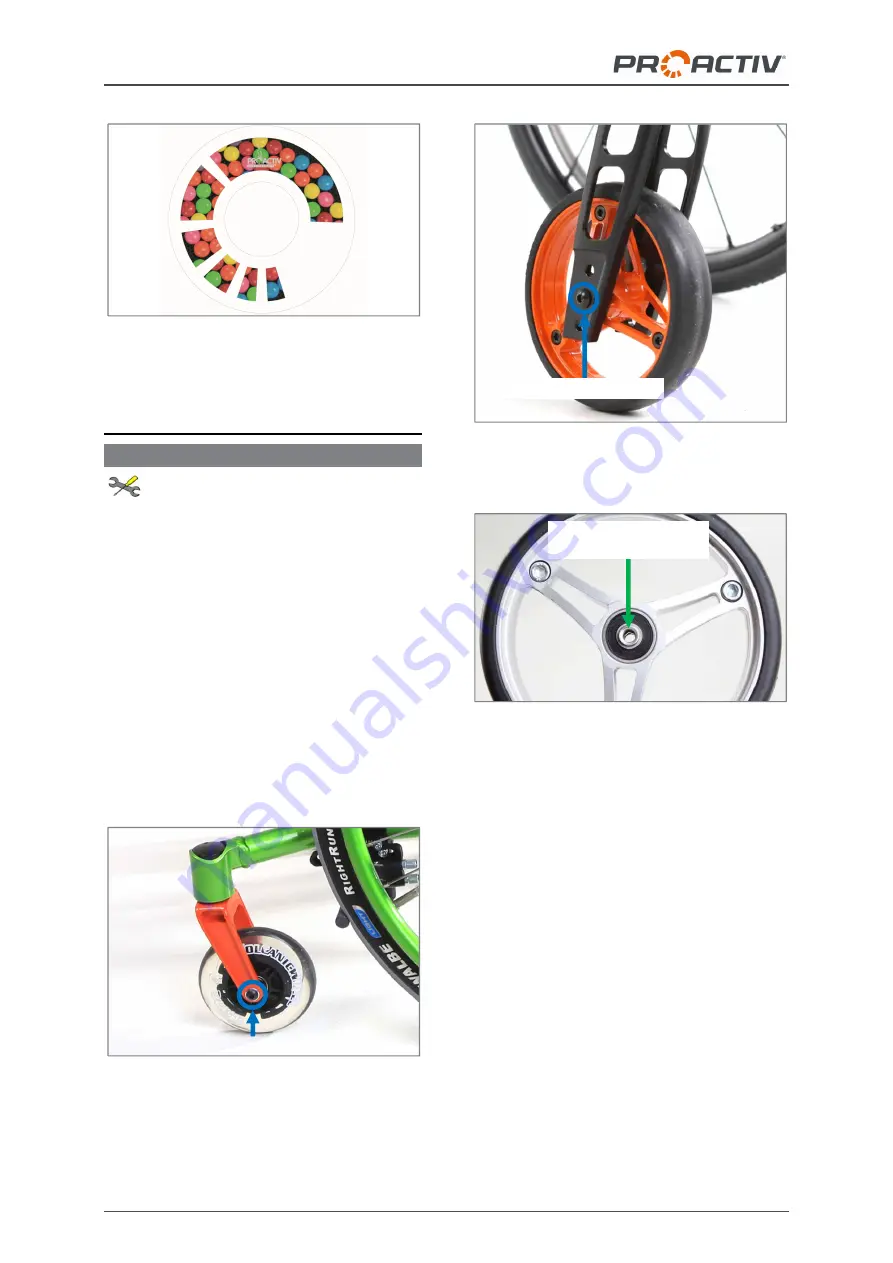
Usage instructions LITTY 4all & 4you
22
Figure 36: Spoke guard for minimising the risk of
hands and fingers getting trapped
19 Caster wheels
19.1 Replacing the caster wheels
The following instructions are intended
for and may only be carried out by a rehabilita-
tion specialist dealer or PRO ACTIV
The caster wheels of the product are, depend-
ing on the type of casters, either fastened with
two M6 axle fixing screws or one M6 axle fixing
screw and a M6 nut.
19.1.1 Replacing the caster wheels when
mounted using two axle fixing
screws
To
remove a caster wheel
, unscrew the M6
axle fixing screws (AF 4 mm) on one side.
Figure 37: M6 axle fixing screw of caster wheel axle
(view from outer side of product)
Figure 38: M6 axle fixing screw of caster wheel axle
(view from outer side of product)
Figure 39: Caster wheel with aluminium hexagon
socket
Now you can see the aluminium axle with a
hexagon socket (AF 4 mm) in the middle of the
axle. This hexagon socket is used to fix the
axle in place, while the second M6 axle fixing
screw (AF 4 mm) is unscrewed. To do this, in-
sert an Allen key (AF 4 mm) into the hexagon
socket on the aluminium axle and hold it still.
At the same time, unscrew the remaining M6
axle fixing screw (AF 4 mm) on the other side.
Now the caster wheel can be removed from
the fork. One spacer each is mounted to the
right and left on the caster wheel that you are
able to remove in order for it to be reused later
when reinstalling the new caster wheel. If you
want to install a different type of caster wheel,
use the enclosed spacers, as these generally
differ depending on the type of caster wheel.
M6 axle fixing screws
M6 axle fixing screws
Aluminium axle with
hexagon socket