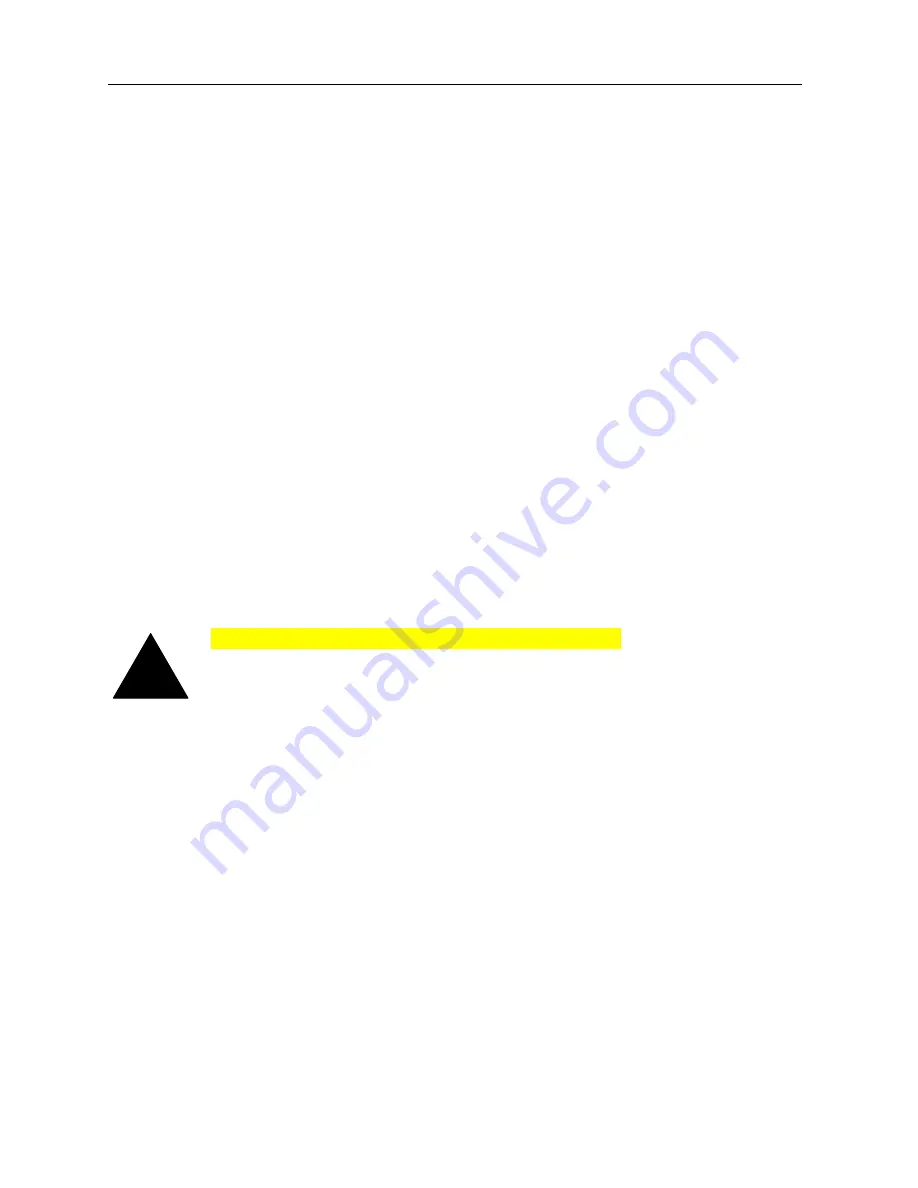
B E L 2 5 2 F u l l y A u t o m a t i c U n i f o r m C a s e T a p e S e a l e r
24
65-06-11 5/18/2007
Section 4 - General Taping Conditions
Problem
:
Tape Does Not Stick To Case Surface
.
The tape is not bonding to the corrugated board of the flaps or ends of the case to provide a secure seal.
Look for the following conditions:
•
Under-filled Case
. Check that product provides support under the top flaps so that they are not
simply pushed down or away from the tape head rather than having the tape rolled onto the surface.
•
Overlapping flaps
. If the outside (major) flaps are allowed to overlap the “step” created results in an
uneven taping surface causing poor tape adhesion that can release during shipping and handling. See
comments on flaps under Troubleshooting section 1,
Corrugated Case Quality & Specifications
•
Tape head roller contact
. Check that the tape head contact or wipe-down rollers are making good
contact with the box and that the roller spring tension is correct.
•
Dust or dirt
. Large amounts of dust or dirt gathering on boxes or in the air will impair adhesive
effectiveness.
•
Temperature
. Hot or cold temperature may require tapes with appropriate adhesive formulations for
good initial bond and permanent sealing performance.
•
Tape adhesive
. Check presence and quality of tape adhesive.
Problem
:
Tape is not cut uniformly.
The tape is not cut properly every time, in the worst situations several boxes may be taped together.
Check the following conditions:
•
Tape head position
. If the top tape head is set too high the cut off knife will not be fully activated
resulting in poor cut off. The tape head side plates should be within 1/16 to 1/8” of the case. Check
also that cases ride fully down between the conveyor belts to provide proper contact with the bottom
head cut off knife.
•
Knife extension
. Be sure that knife extends enough to fully contact the tape during the cutting
stroke.
•
Tape tension
. Unroll tension should be smooth and not too tight as a ‘snap back’ caused by stretched
tape can cause a jagged cut off and tape pieces to stick to the blade.
•
Clean knife
. Clean the blade and apply a little silicon or oil to avoid adhesive build up on the sharp
points.
•
Knife blade wear or damage
. Blades must be very sharp to work well. The points are easily
damaged if contacted by any hard material. Replace the blade if it seems dull.
•
Cut-off spring tension
. Check to ensure the spring that provides power to cut off arm has enough
tension to cut through the tape. Replace the spring if it is too weak.
SAFETY CAUTION –
Tape Head knife is very sharp
!