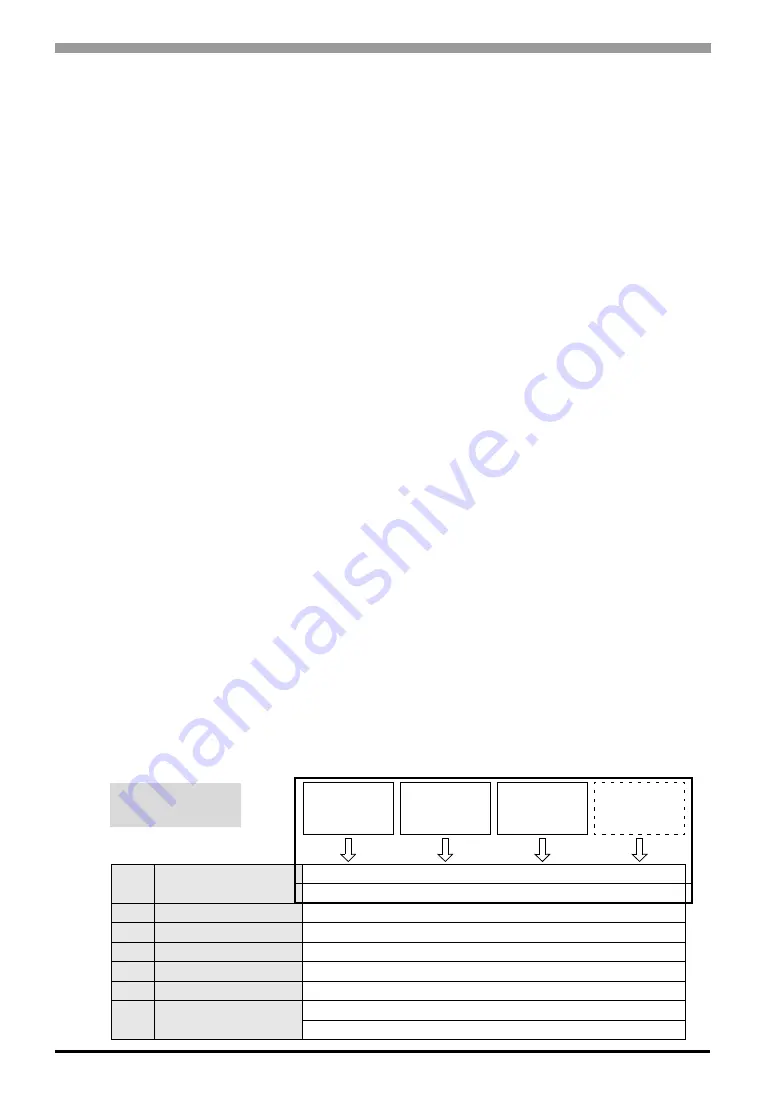
Hybrid Terminal Block Hardware Manual
1-2
1.1
About CANopen
1.1.1
Introduction
CANopen is an open fieldbus protocol for industrial control systems. It is particularly well suited to real-time
control, as it provides an effective, low-cost solution for integrated industrial applications.
1.1.2
The CANopen Protocol
The CANopen protocol was created as a subset of CAL (CAN Application Layer). It is widely utilized to
connect industrial components.
The CANopen standards are managed by CiA (CAN in Automation), promoting the adoption of various
applications. In Europe, CANopen is now the recognized standard for embedded systems in networks.
1.1.3
CANopen Profiles
The communication profile
The CANopen communication profile is specified into four message types by the CiA DS-301.
•
Real-time Data (PDO: Process Data Objects)
•
Configuration Data (SDO: Service Data Objects)
•
Special Function (Time Stamp, Sync Message, Emergency Message)
•
Network Administration Messages (Boot-up Message, NMT Message, Error Control)
For the details, please see the GP- Pro EX Reference Manual “Controlling External I/O”
The device profile
The most important types of devices used in factory automation are described in the “Device profiles”. They
also define device functionalities.
Examples of the standard devices described are:
•
digital and analog input/output modules (DSP-401),
•
motors (DSP-402),
•
measurement device (DSP-404),
•
other devices (DSP-4xx).
CANopen
is based on CAL
7
APPLICATION
CiA DS-301 = Communication profile
CAL = CAN Application Layer
6
PRESENTATION
EMPTY
5
SESSION
EMPTY
4
TRANSPORT
EMPTY
3
NETWORK
EMPTY
2
LINK = LLC + MAC
CAN 2.0 A and B + ISO11898
1
PHYSICAL
CAN 2.0 A and B = ISO11898-1 and 2
ISO 11898 + DS-102
Device Profile
CiA DSP-401
I/O modules
Device Profile
CiA DSP-402
Drives
Device Profile
CiA DSP-404
Measuring devices
Device Profile
CiA DSP-4xx