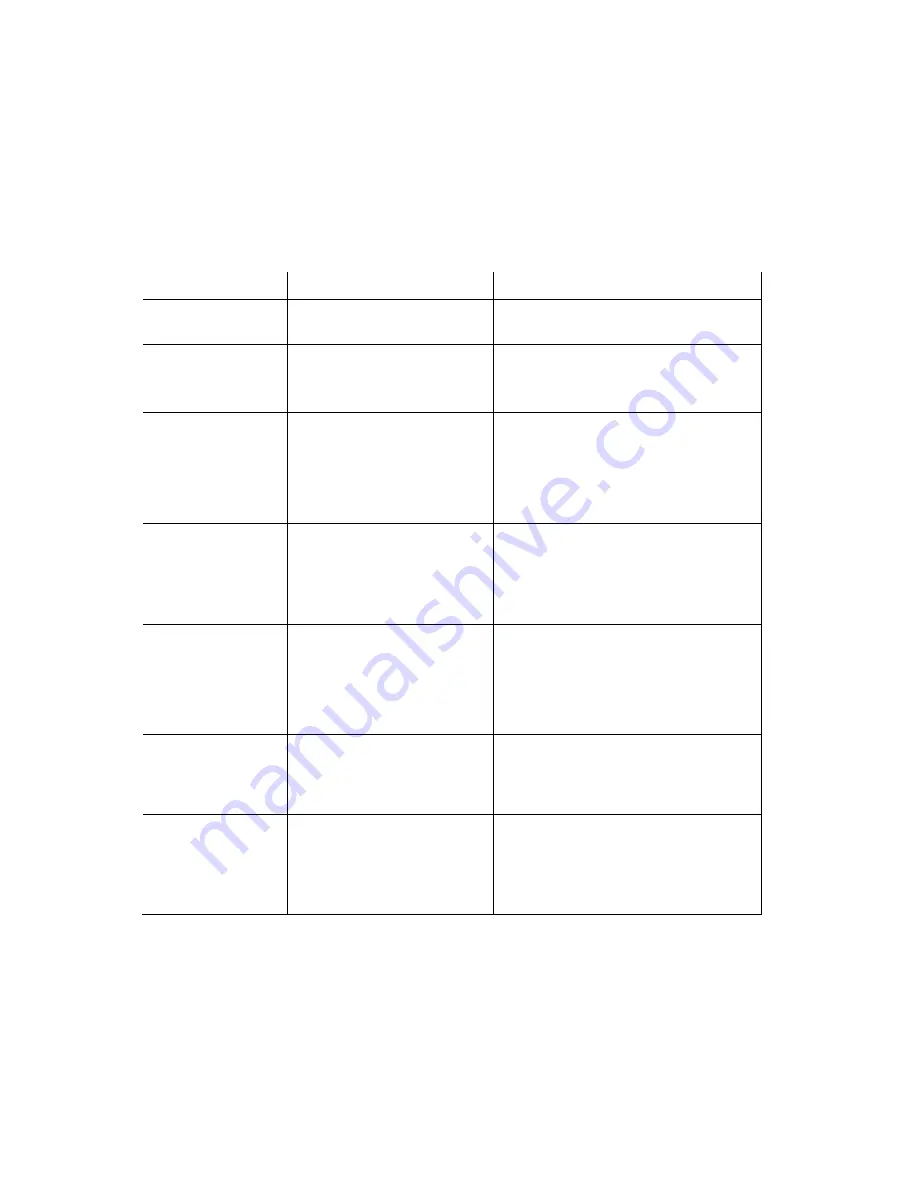
17
The second column labeled possible cause lists the obvious external possibilities that may contribute to the
machine symptom
Step 3 Recommended course of action
This column provides a course of action for the possible cause, generally it states to contact welding
for repair of machine.
Troubles
Cause
Remedy
1.Fan not works
properly
1.the fan line lose
2.Fan breakage
1.Connect the line
2.Change the fan
2.No indicating on
the front panel
1.the power line lose
2.Indicating light broken
3.the fuse or IGBT broken
1.Check the power,Connect the line
2.Change it(
φ
8)
3.Change the fuse 5A/250Vor Contact with
the namufacturer .
3.Over heating light
on(warning led lights
red or yellow color)
1.aeration is not good
2.The temperature is too high
3.over-load use
4.Thermostat broken
5.Control plate broken
1.get rid of the bar 0.5m around
2.Reduce the temperature
3.Reduce the use loading
4.Change the thermostat(JUC-OF)
5.Check and change the control plate
4.Over-current light
ON (warning led
lights green color)
1.IGBT broken
2.output diode broken
3.Drive plate broken
4.Control plate broken
5.over current welding
Contact the manufacturer
5.Wire
feeder
not
work ( welding current
not adjustable)
1.the fuse broken
2.Potentiometer line fall down
or Potentiometer broken
3.the wire blocked
4.the drive circuit broken
5.other reasons
1.Change the fuse 5A/250V
(on left panel,open wire feeder case)
2.Connect the lines or Change it
3.Check the gun
4.Change the control panel
5.Contact with the namufacturer
6.Welding Voltage
not adjustable
1.Potentiometer line fall down
2.Potentiometer broken
3.The circuit broken
1.Connect the lines
2.Change it
3.Change the control pcb
7.Welding stops, and
warning light is on
Self-protection has engaged
1.Display "801"
2.Display "802"
3.Display "804"
4.Display "805"
1.over-voltage, lower-voltage
2. over-temperature,
3.over-current,
4.torch switch always close
Summary of Contents for POWER MTS175S
Page 1: ...CC CV MULTI PROCESS WELDING MACHINE GMAW GTAW SMAW POWER MTS175S OPERATION INSTRUCTIONS...
Page 19: ...19 MAIN UNIT Wiring diagram...
Page 20: ...20...
Page 21: ...21...
Page 22: ...22...